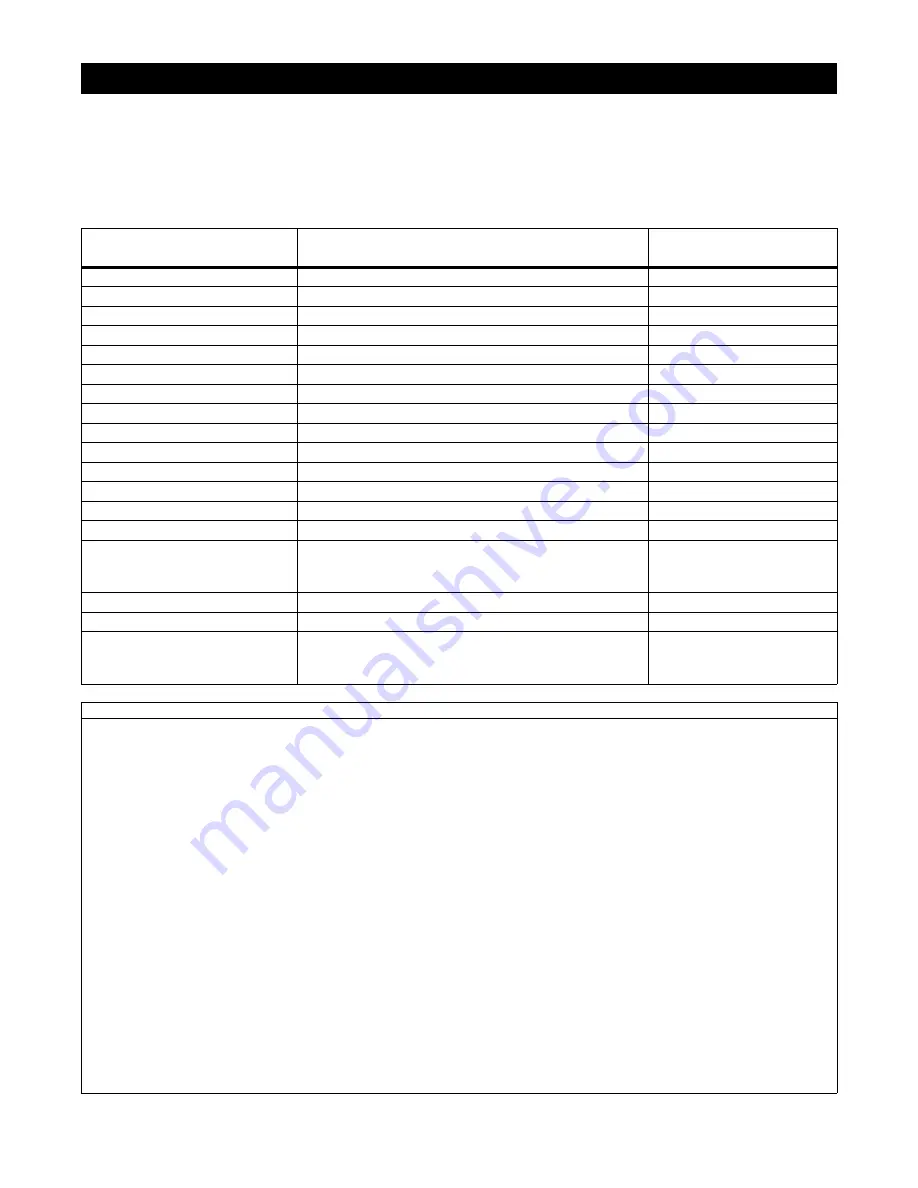
5 - 11
5.1 ENGINE TROUBLESHOOTING
The following troubleshooting chart is to be used to
isolate engine problems and give possible causes and
corrective action responses.
The troubleshooting key is generic and can be used for
several types of engines. Use only those possible
causes and corrective actions that apply to the
unit.
SECTION 5 - ENGINE
TROUBLE
POSSIBLE CAUSES
(Refer to Key Below)
CORRECTIVE ACTION
Black Exhaust
1, 20, 22, 25, 29, 31, 32, 33
repair or replace
Blue/White Exhaust
4, 20, 25, 31, 33, 34
repair or replace
Difficult Starting
1, 5, 7, 8, 9, 10, 20, 21, 22, 29, 31, 32, 33
repair or replace
Erratic Running
1, 7, 8, 9, 10, 20, 21, 23, 26, 29, 33, 59, 62
repair or replace
Excessive Fuel Consumption
1, 20, 22, 23, 25, 29, 31, 32, 33
repair or replace
Excessive Crankcase Pressure
25, 31, 33, 34, 45, 55
High Oil Pressure
4, 41
repair or replace
Knocking
22, 26, 29, 31, 33, 36, 46, 59
repair or replace
Loss of Power or System
1, 8, 10, 20, 21, 22, 23, 25, 26, 31, 32, 33
repair or replace
Low Cranking Power
2, 3, 4, 11
repair or replace
Low Oil Pressure
4, 36, 37, 39
repair or replace
Misfiring
10, 20, 25, 26, 28, 29, 32
repair or replace
Overheating
1, 19, 25,
repair or replace
Poor Compression
25, 28, 29, 31, 32, 33, 34,59,
repair or replace
Starts and Stops
1, 6, 10, 62
repair or replace
see electrical systems
see engine service manual
Vibration
20, 23, 25, 26, 29, 33, 45, 49
repair or replace
Will Not Crank
2, 11, 45
charge battery or replace
Will Not Start
1, 10, 62
repair or replace
see electrical systems
see engine service manual
TROUBLESHOOTING KEY
1
Restriction in air cleaner
22
Incorrect grade of fuel
43
Faulty suction pipe
2
Bad electrical connection
23
Sticking throttle/restricted movement
44
Choked oil filter
3
Faulty starter motor
24
Exhaust pipe restriction
45
Bad solenoid switch
4
Incorrect grade of lubricating oil
25
Leaking cylinder head gasket
46
Incorrect piston height
5
Low cranking speed
26
Overheating
47
Damaged fan
6
Fuel tank empty
27
Cold running
48
Faulty engine mounting
7
Controls not in correct operation
position
28
Incorrect tappet adjustment
49
Incorrectly aligned flywheel and/or
flywheel housing
8
Blocked fuel feed line
29
Sticking valves
50
Faulty thermostat
9
Faulty fuel lift pump
30
Incorrect high pressure pipes
51
Restriction in water jacket
10
Choked fuel filter
31
Worn cylinder bores
52
Loose fan belt
11
Battery capacity low
32
Pitted valves and seats
53
Choked radiator
12
Air in fuel system
33
Broken, worn or sticking piston ring(s)
54
Faulty water pump
13
Faulty fuel injection pump
34
Worn valve stems and guides
55
Choked breather pipe
14
Faulty fuel injectors or incorrect
type
35
Restriction in air cleaner
56
Damaged valve stem oil deflector (if
fitted)
15
Incorrect use of cold start
equipment
36
Worn or damaged bearings
57
Coolant level too low
16
Faulty cold start equipment
37
Insufficient oil in sump
58
Blocked sump strainer
17
Broken fuel injection pump drive
38
Bad/defective oil temperature switch
59
Broken valve spring
18
Incorrect fuel pump timing
39
Oil pump worn
60
Exhaust or vacuum pipe leak
19
Incorrect valve timing
40
Pressure relief valve sticking open
61
Bad or defective water temperature
switch
20
Poor compression
41
Pressure relief valve sticking closed
62
Bad spark plug(s)
21
Blocked fuel tank vent
42
Broken relief valve spring
Содержание 990014
Страница 1: ......
Страница 20: ...8 20 PF1643 Figure 17 1 Drive Coupler 2 Hydraulic Tank 3 Hydraulic Pump 4 Housing 1 2 3 4...