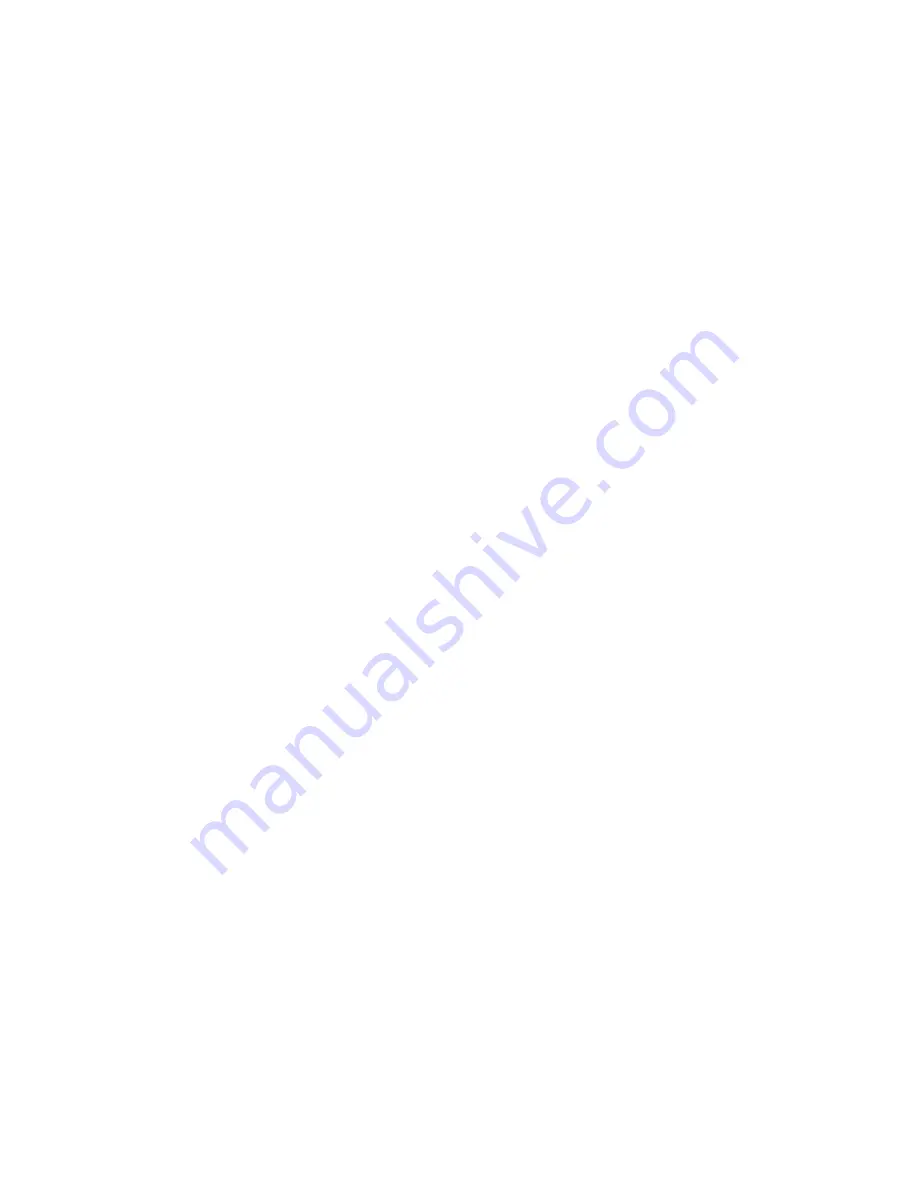
GOW-MAC Instrument Co. Series 400 / 402 Gas Chromatograph Operating Manual
May 2017, Rev. 7
14
Detector Oven
Temperature Range:
Ambient to 400 °C
Temperature Control:
solid state, time proportioning, RTD sensors, direct reading, ambient
to 400 °C
Temperature Readout:
3-1/2 digit LCD digital meter
Operating Temperature: 15 °C higher than the column temperature
Detector
Type:
Thermal Conductivity (TCD)
Design:
Flow-through
Elements:
Four (4) Rhenium-tungsten (WX) on standard 9225 mount, tube nut
closure (standard unit)
Response Time:
0.5 seconds
Noise:
10
V maximum within operating parameters
Drift:
40
V hour maximum
Carrier Gas:
Helium or Nitrogen
Max. Current Limit
100 mA with He
Refer to the General Service Bulletin
at ambient temp:
120 mA with N
2
Detector Power Supply
Line operated, solid state, integrated circuit regulated, constant current
55 Vdc (max.), 300 mA (max.)
Ripple and noise:
< 5 mV rms
Injection Ports
Dual injection ports
Low Volume
Injection Method:
direct on-column or gas sample valve injection
Septums:
standard 9 mm
Operating Temperature: 0 - 400 °C
Temperature Control:
solid state, time proportioning, RTD sensors, direct reading, ambient
to 400 °C
Temperature Readout:
3-1/2 digit LCD digital meter
Gas Flow
Flow System:
dual column with dual injection ports and exits
Flow Control:
two (2) metering valves for independent fl ow control to each column
Filament protector pressure switch in carrier inlet line.
Thermal Conductivity Bridge Control
Polarity Switch
Bridge Zero Adjust
Current Adjustment:
continuous adjustment to 300 mA (using He carrier)
Attenuator:
12 positions to 1024 plus infi nity (
)
Содержание 400 Series
Страница 2: ...GOW MAC Instrument Co Series 400 402 Gas Chromatograph Operating Manual May 2017 Rev 7 2 ...
Страница 4: ...GOW MAC Instrument Co Series 400 402 Gas Chromatograph Operating Manual May 2017 Rev 7 4 ...
Страница 8: ...GOW MAC Instrument Co Series 400 402 Gas Chromatograph Operating Manual May 2017 Rev 7 8 ...
Страница 34: ...GOW MAC Instrument Co Series 400 402 Gas Chromatograph Operating Manual May 2017 Rev 7 34 ...
Страница 40: ...GOW MAC Instrument Co Series 400 402 Gas Chromatograph Operating Manual May 2017 Rev 7 40 ...
Страница 56: ...GOW MAC Instrument Co Series 400 402 Gas Chromatograph Operating Manual May 2017 Rev 7 56 ...
Страница 58: ...GOW MAC Instrument Co Series 400 402 Gas Chromatograph Operating Manual May 2017 Rev 7 58 ...
Страница 60: ...GOW MAC Instrument Co 60 ...
Страница 62: ...GOW MAC Instrument Co Series 400 402 Gas Chromatograph Operating Manual May 2017 Rev 7 62 ...
Страница 64: ...GOW MAC Instrument Co Series 400 402 Gas Chromatograph Operating Manual May 2017 Rev 7 64 ...