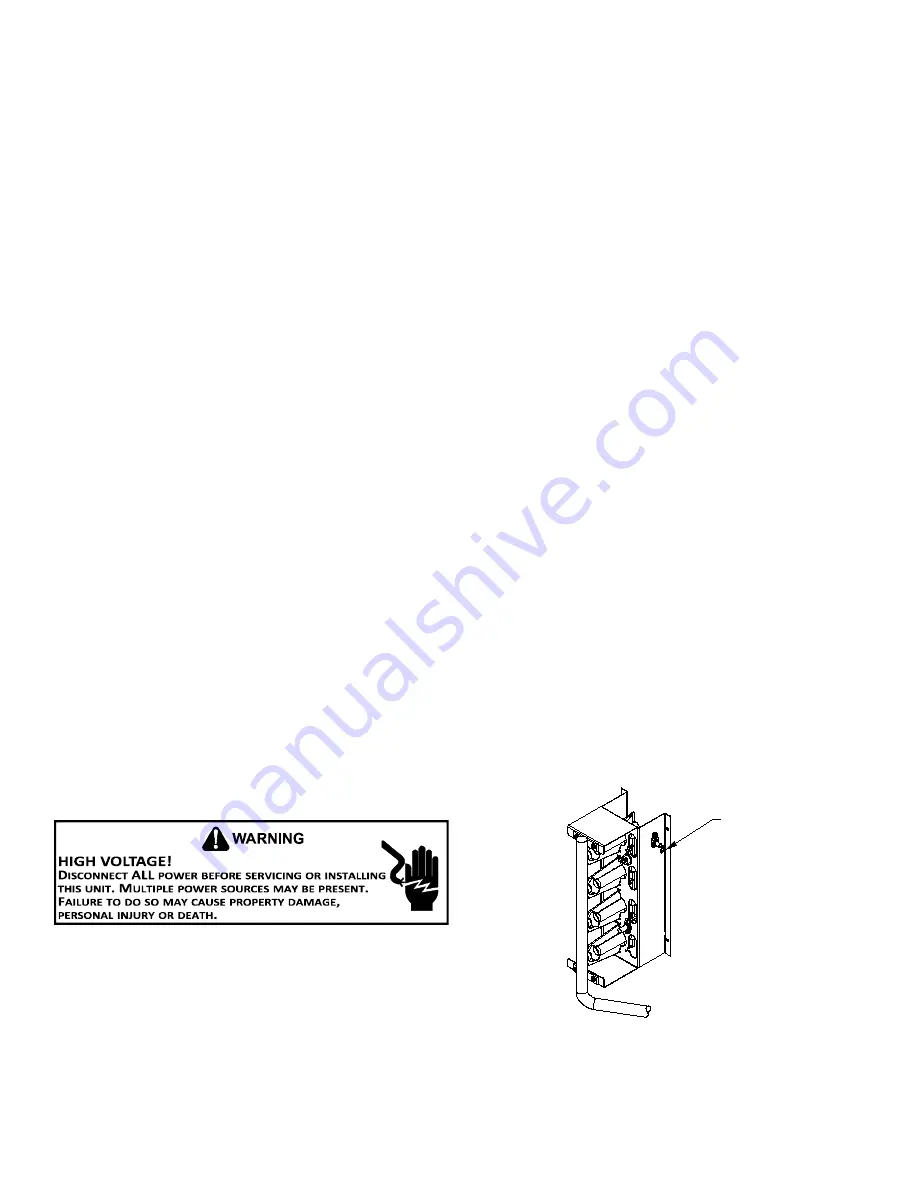
19
Low Flame Signal
Under some conditions, the fuel or air supply can create a
nearly invisible coating on the flame sensor. This coating
acts as an insulator causing a drop in the flame signal. If the
flame signal drops below a predetermined value, the ignition
control will display an error code of (1) flash on the amber
diagnostic LED. The unit will continue to operate until the
control can no longer detect flame.
Abnormal Operation - Cooling
Short Cycle Compressor Delay
The automatic ignition control has a built-in feature that pre-
vents damage to the compressor in short cycling situations.
In the event of intermittent power losses or intermittent ther-
mostat operation, the ignition control will delay output to the
compressor contactor for three minutes from the time power
is restored or thermostat call for cooling is restored. (Com
-
pressor is off a total of three minutes). The diagnostic red
LED will flash six (6) times to indicate the compressor con
-
tactor output is being delayed.
NOTE:
Some electronic thermostats also have a built-in
compressor short cycle timer that may be longer than the
three minute delay given above. If you are using an elec-
tronic thermostat and the compressor has not started after
three minutes, wait an additional five minutes to allow the
thermostat to complete its short cycle delay time.
High Pressure Switch/Loss of Charge Switch
Some models include a high pressure cutout switch and/
or a loss of charge cutout switch. The high pressure cutout
switch protects the refrigeration system from excessive op-
erating pressures. The loss of charge cutout switch protects
the refrigeration system from very low operating pressures
due to a loss of refrigerant. Compressor operation will be
disabled if either of these devices opens. If either devices
opens, the diagnostic red LED will flash (9) times to indicate
that a refrigeration system pressure switch is open.
MAINTENANCE
Have the gas heating section of the unit checked at least
once a year before the heating season begins, to be sure
that the combustion air inlet and flue outlet hoods are not
blocked by debris, which would prevent adequate combus-
tion air and a properly operating vent system.
Filter Replacement or Cleaning
A return air filter is not supplied with this unit; however, there
must be a means of filtering all of the return air. The filter(s)
may be located in the return air duct(s), or return air filter
grille(s). Consult with your installing dealer for the actual lo
-
cation of the return air filter(s) for your unit.
Dirty filters are the most common cause of inadequate heat
-
ing or cooling performance. Filter inspection should be made
at least every two months; more often if necessary because
of local conditions and usage.
Dirty throwaway filters should be discarded and replaced
with a new, clean filter. Dirty permanent filters should be
washed with water, thoroughly dried and sprayed with a filter
adhesive before being reinstalled. (Filter adhesives may be
found at many hardware stores.) Permanent filters should
last several years. However, should one become torn or un-
cleanable, it should be replaced.
Cabinet Finish Maintenance
Use a fine grade automotive wax on the cabinet finish to
maintain the finish’s original high luster. This is especially
important in installations with extended periods of direct
sunlight.
Clean Outside Coil (Qualified Servicer Only)
The coil with the outside air flowing over it should be inspect
-
ed annually and cleaned as frequently as necessary to keep
the finned areas free of lint, hair and debris.
Condenser, Evaporator, and Induced Draft Motors
Bearings on the air circulating blower motor, condenser mo-
tor and the combustion fan motor are permanently lubricat-
ed. No additional oiling is required.
Flame Sensor (Qualified Servicer Only)
A drop in the flame current can be caused by a nearly invisi
-
ble coating on the flame sensor. This coating, created by the
fuel or combustion air supply, can be removed by carefully
cleaning the flame sensor with steel wool.
Flame
Sensor
NOTE:
After cleaning, the microamp signal should be stable
and in the range of 4 - 6 microamps DC.
Содержание GPG 16 M Series
Страница 30: ...30 THIS PAGE LEFT INTENTIONALLY BLANK...
Страница 31: ...31 THIS PAGE LEFT INTENTIONALLY BLANK...