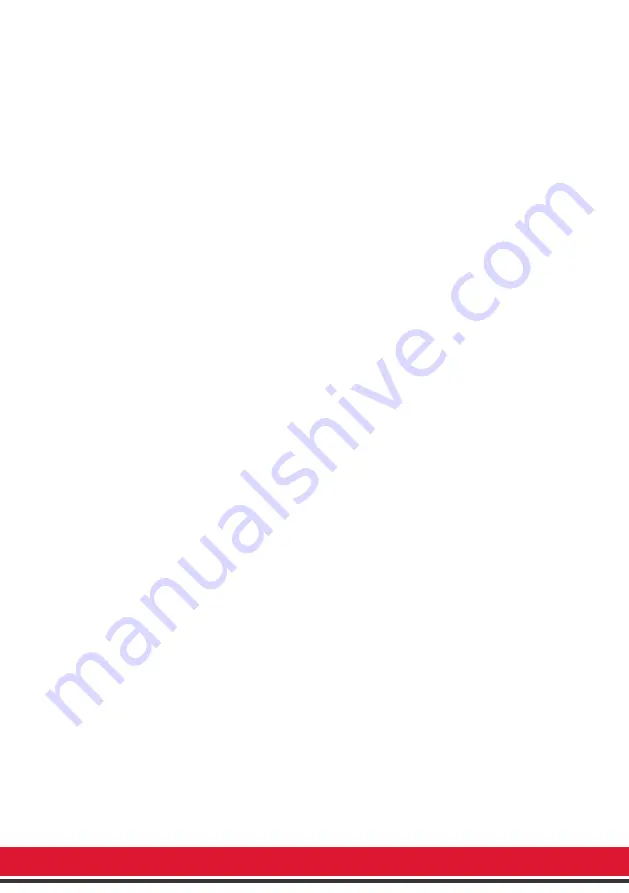
· 29
GLOBE RM410 PISTON AIR MOTOR MANUAL| INCLUDING AUXILIARIES | ATEX Certified
RM110 Motors
Lift the spacing washers (31/34) out. Slightly rotate the shaft backwards and forwards and inspect
the amount of wear which is present on the big end assembly. Remove the top retaining ring (part
no. 74). All the connecting rods can then be lifted upwards and pushed outwards towards the cylin-
ders. Remove cylinder bolts (37) and the entire piston assembly can be withdrawn from the motor
unit.
RM510 and 610 Motors
Remove bolts (58) holding the output shaft assembly. Remove bolts (57) and the output flange (24
A/B). This will then expose the inside of the motor. Turn the crankshaft so that one rod is at T.D.C.
Remove that cylinder, the circlip and gudgeon pin. Push out from the piston and the entire assembly
can be removed. Repeat this procedure in turn until all the pistons have been removed. On this motor
the balance weight and crank assembly is built as one item and this can now be removed. Remove
locking nut (22) and the tapered pin (21). Both balance weights (part no. 20A and 20B) can now
be disengaged. This will expose the king rod and queen rod assembly. To remove the queen rod
remove the pivot pin (29).
RM210/310/410 Motors
These units are of the king rod variety and again it is wise to slightly rotate the crankshaft (part no.
20 A/B) in direction to test any excessive wear on either the king rod bearing or the pivot pins (part
no. 29). Having first removed the outer spacing washer (31/34) withdraw pivot pins (part no. 29).
This procedure is usually done with a bent rod withdrawing the pins from the inside outwards. Remo-
ve all cylinder cap bolts (part 37) and by pushing the queen rods (part 30) outwards the entire pis-
ton and rod assembly can be removed from the motor. Turn the motor unit over to extract the crank
bearing bearings (part no. 48). The main king rod (part no. 12) can then be lifted upwards and
ilted over the top of the crankshaft. Remove the main king rod, piston and cylinder from the motor.
Remove the output shaft circlip (14), spacer (15) and shims (16). Remove the counter sunk bolts (52)
holding the output flange (24 /A B) on to the engine case (part no. 27). The engine case (27) can
be Drift the crankshaft inwards from the flange plate (24A). To remove the outer shaft bearings (55
and 56) drift to their respective sides as they are located inwardly on the two circlips (part no. 18).