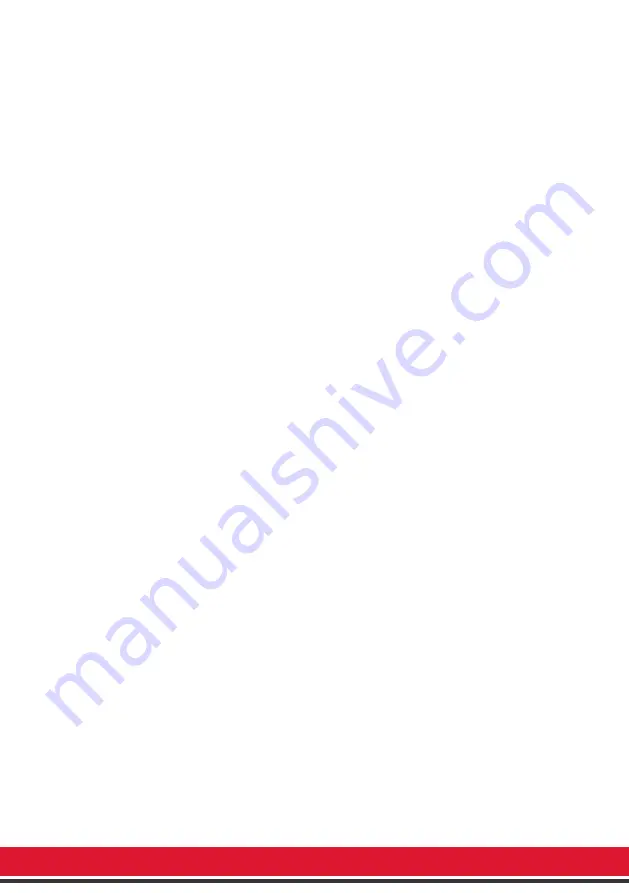
28 · GLOBE RM410 PISTON AIR MOTOR MANUAL| INCLUDING AUXILIARIES | ATEX Certified
All Motors
Inspect the clearance of the pivot pins (29) in queen rod (30) and king rod(12). Inspect the gudgeon
pin in both the piston and all rods. Check for wear on the main crankshaft (20A, 20B) and on the
main big end bearing (no. 48). The wear in the cylinder bores can be checked by removing each
compression ring (10) and pushing it into the cylinder bore (8). The ring gap should be in the region
of 0.003 to 0.004” (0.075 - 0.010 mm). Bore wear cause loss of power and inject high pressure air
into the case & oil could be ejected from the breather plug (part no. 46). All other parts should
thoroughly cleaned and inspected for wear. Spare parts can be found from the spare listings. The
motor number and its code should be incorporated in any spares order. This is always stamped on
the main flange plate (24) located near the breather plug hole 46, i.e. 230 Hx. GLOBE provide a
seal kit for each motor and it is strongly recommended that new oil seals, seals and gaskets are used
throughout.
A: Disassembly motor
Note!
For the clarification of the part numbers please refer to the Spare Parts Lists in the appendix.
Preparation for disassembly
Remove the motor from its operating position to a clean working surface ready for stripping, exter-
nally clean the motor ready for opening. Drain the oil from the motor casing by removing the drain
plug (26). Stripping and re-assembly will be simplified if the crankshaft (20/A/B) or output shaft
(67) RM510 and RM610 is vertically in a soft-jawed vice or supported on a suitable packing to
raise the shaft clear of the working surface.
Removal of Rotary Valve Housing
»
Remove inlet / exhaust adaptor plate (72) or control valve fitted).
»
Remove valve cover
»
Release bolts (38) and valve bush housing (3) can be eased upward.
»
On RM110 to 410 motors remove grub screw (49) together with the valve side balance weight
(number 35).
»
All motors - carefully remove rotary valve (2) from housing (3). This can generally done from
the inside outwards and inspect both the rotary valve and the housing for wear. The normal
clearance at manufacture between these two components is 0.002 - 0.003” (0.05 - 0.075
mm). Excessive wear will cause air leakages and loss of efficiency of the unit.
Servicing Motor