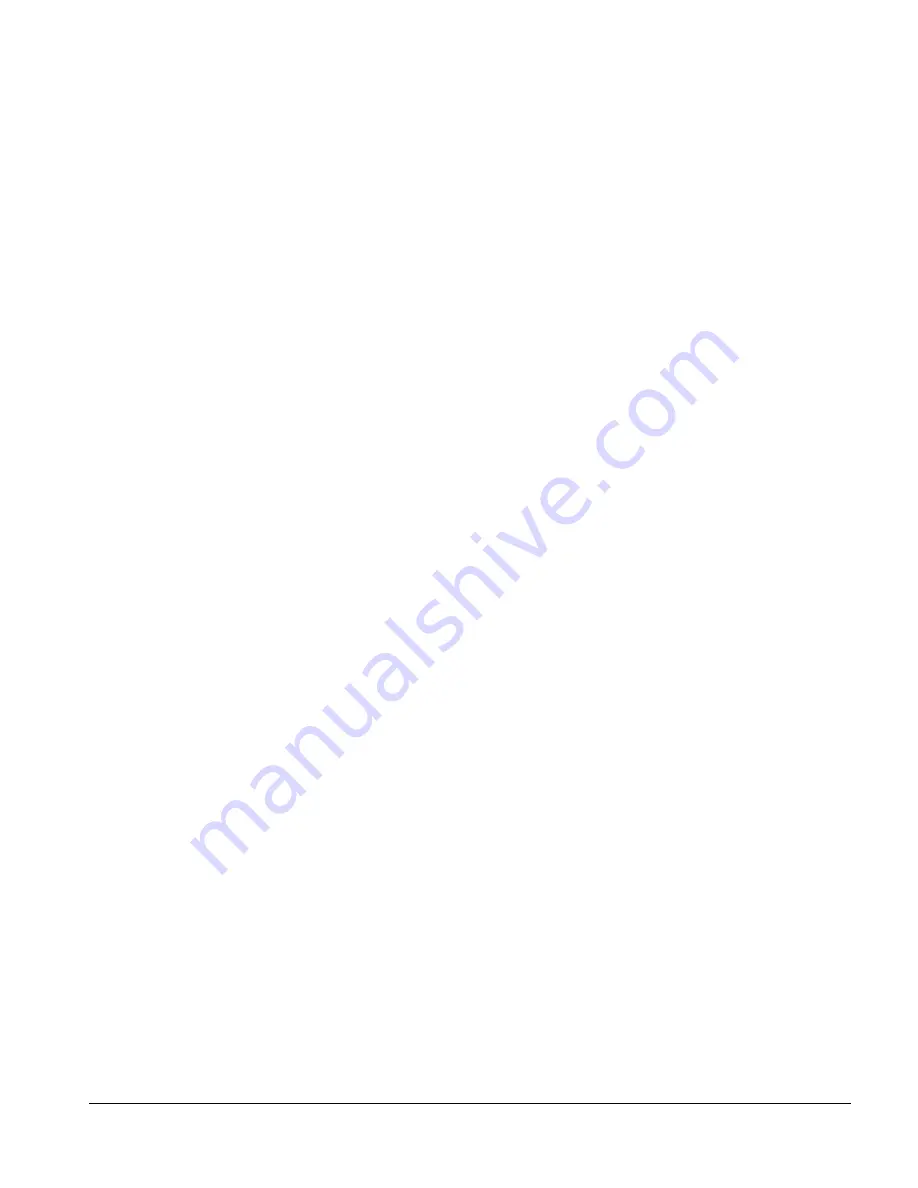
Series 1800 Washers
61301604086
1–3
Optional Features
•
Strip Chart Printer
•
RS232 Port for Data Download
•
Double Door Pass Through
•
Double Door Interlocks for Manual Doors
•
Powered Vertical Doors with Interlocks
•
Electric Stainless Steel Sump Heaters
•
Stainless Steel Treatment Components
•
Cold Water Pre-Wash Treatment
•
Non-Recirculated Final Tap Water Rinse
•
Non-Recirculated Final Pure Water Rinse
•
House Tap Water Temperature Booster
•
Pure Water Temperature Booster
•
Automatic Agent Injection Systems
•
Internal Chamber Illumination
•
Stainless Steel Automatic Damper
•
Power Exhaust Fan
•
Vented/Non-Vented Vapor Removal Condenser
•
Drain Discharge Cool-Down Systems
•
Treatment Solution pH Neutralization Systems
•
Removable Center Header
•
Recessed or Free Standing Cabinet Installations
•
Seismic Design
•
Knocked Down Shipment
•
Modem Troubleshooting
Accessories
•
Mouse Box Processing Rack
•
Rat Box Processing Rack
•
Pan Processing Rack
•
Transfer Cart
•
Feeder Bottle Baskets
•
Custom Accessories
Содержание Castle MTP 1800 Series
Страница 1: ...SERIES 1800 CAGE AND BOTTLE WASHER OPERATING MANUAL 61301604086 Rev A...
Страница 2: ......
Страница 68: ...Troubleshooting 5 6...
Страница 74: ...Installation Instructions 6 6...
Страница 92: ...Optional Equipment 7 18...
Страница 97: ......