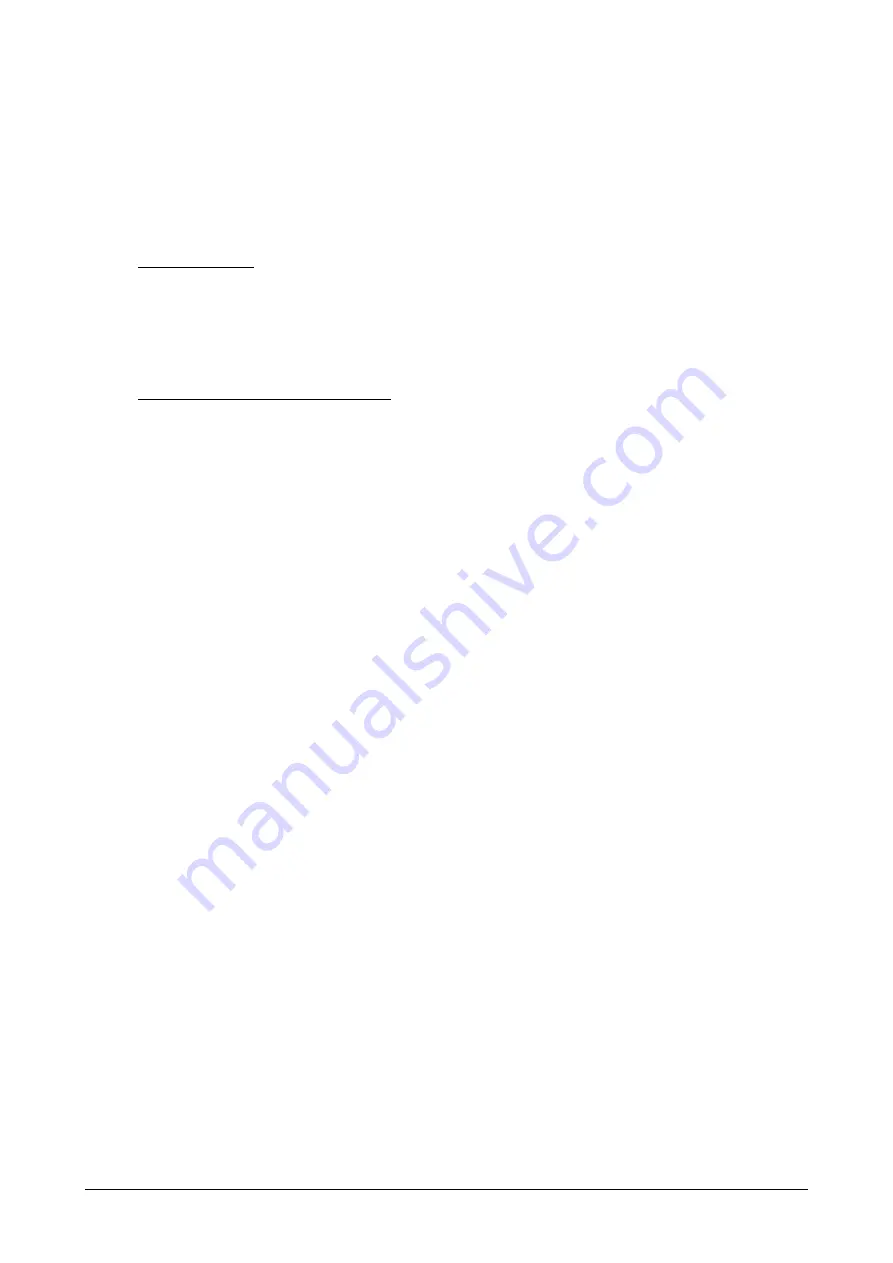
____________________ _
ADL300-EPCv2- User Guide
Page 8 of 64
2. APPLICATION OVERVIEW
This section contains a general description of the EPC (Elevator Positioning Control) application.
The
EPC
(Elevator Positioning Control) function is a separate application for independent management of
direct arrival at the floor with internal position regulator and saving of floor distances (system autotuning).
There are two possible configurations for this application:
- Digital I/O control: in the installations where the number of available I/Os is sufficient, the control can
be done via I/Os.
N
Digital Inputs are necessary to manage a system with 2
N
floors. If the number of
I/Os available in the BASIC version (ADL300
B
) is not sufficient, it is possible to use the ADVANCED
(ADL300
A
) version with an adequate number of I/Os (e.g. by using the
EXP-IO-D16R4-ADL
expansion card).
-
Remote control via CANopen fieldbus: it is possible to control the application via CANopen fieldbus,
saving in this way I/Os. To use this mode the ADL300 must be equipped with the CANopen
interface. (Order the ADL300 version with CAN interface).
-
In case of systems where the number of floors is 16+, the use of CANopen control is suggested
.
The main requirements for the EPC function are:
-
Maximum operating speed (4m/s)
-
Maximum number of floors 32
-
Stop at floor without approaching at reduced speed (positioning for direct arrival at floor)
-
Automatic management of speed and ramp times according to the floor of call and arrival
-
Management of brake and contactor command sequences
-
Availability of configurator for complete configuration and monitoring of operating variables.
-
Possibility of calling floors directly (floor booked) or of requesting stops at floors during travel.
-
Possibility of entering corrections and compensations on floor levels
Advanced controls:
-
Inertia Compensation
-
Battery run mode with choice of preferred direction
-
Over Permissible Speed protection
The following functions are managed externally, by an external PLC or electromechanical unit:
-
Floor call logic
-
Safety logic
The control system recognises the position of the floors via a series of cams installed along the path of the
lift car. It uses a Self Study initialisation sequence to detect the position of these cams, on the basis of which
it determines the level of each floor and the number of floors.
The distance between floors may vary from floor to floor, subject to certain restrictions.