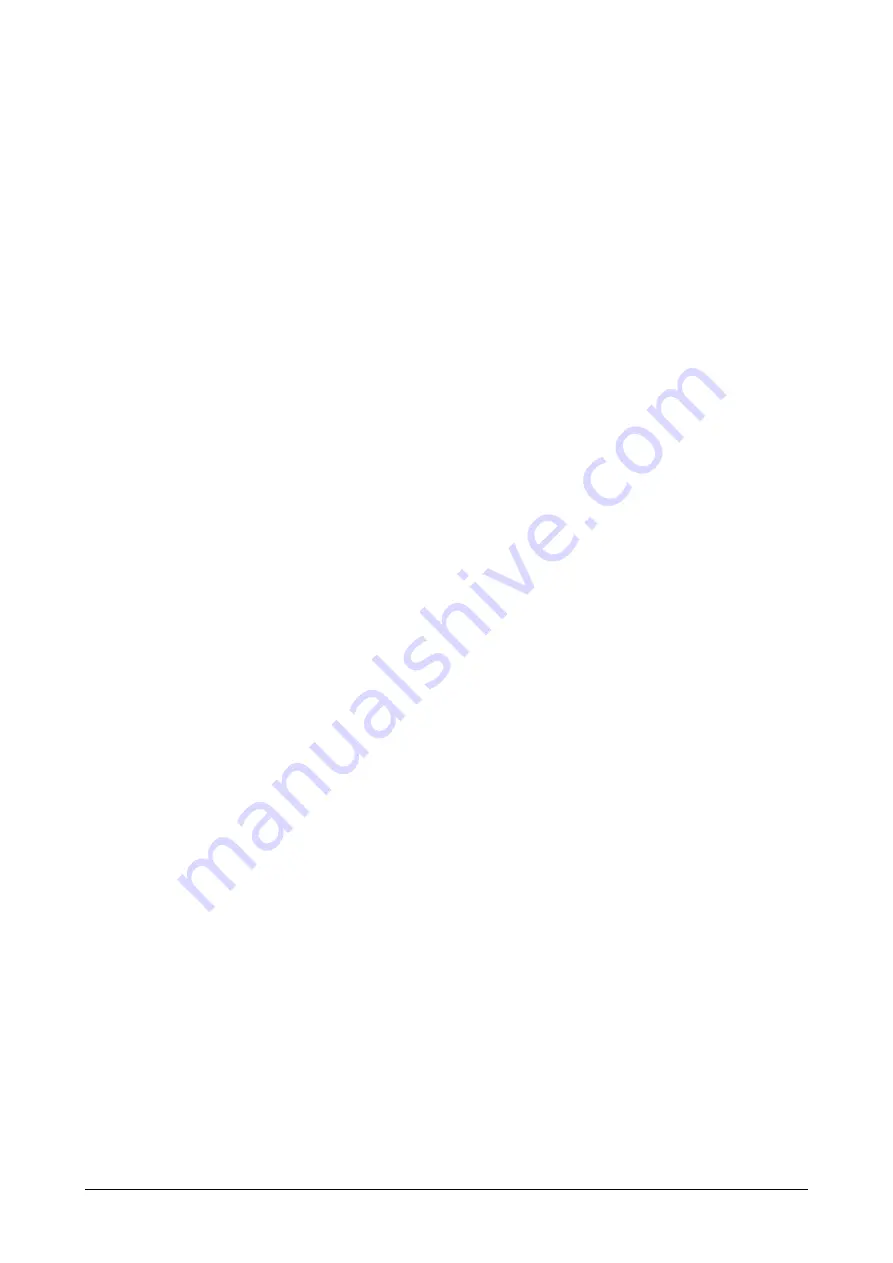
____________________ _
ADL300-EPCv2- User Guide
Page 14 of 64
3.2 Description of Functions (EPC)
The internal positioning device (EPC) offers standard functions, positioning mode functions and special
functions.
3.2.1 Standard functions:
Some of the functions are already available in the standard version of the drive (EFC application). These
mainly include:
-
Signals and sequences for brake and door contactor commands
-
Pre-torque function
-
Ramping down of current at the end of the sequence
-
Weights and estimated inertia.
3.2.2 Floor counter
The application must be able to read the floor counter cams (cam A and cam B), and recognise the current
position in the shaft and the direction of travel. The floor counter cams are arranged so as to simulate a
hypothetical incremental encoder "spread" over the lift shaft. The position is thus controlled twice, once
based on the reading of the motor position sensor and once based on the reading of the cams to check the
real position of the lift car in the shaft.
3.2.3 Mechanical constants
Specific parameters used to perform exact calculations of mechanical constants (separation of the ratio into
two parameters).
3.2.4 Elevator Shaft Limit
Control functions to prevent shaft limits from being exceeded. The controls regard both position and speed.
An alarm must be generated if the control systems intervene.
3.2.5 Self Study function
The Self Study command is used to set a special control system mode in order to detect the height of the
cams indicating the position of the floors in the lift shaft. These heights are detected automatically by
performing a series of movements. The following positions are stored for each floor:
A Low, B High
This
command should only be executed when installing the control system or moving the floor identification cams
.
No direct floor call or movement commands are possible (except jog and zero cycle) unless a Self Study
command has been correctly executed.
3.2.6 Zero cycle function
The zero cycle command is used to move the lift car to a known zero position. A zero cycle must be
executed each time the drive is switched on to reset the floor counter and rephase to a known position.
The
encoder alarm generates a loss of zero
3.2.7 Jog mode
This command is used to perform manual jog operations in both directions. This is necessary during
maintenance operations and commissioning.