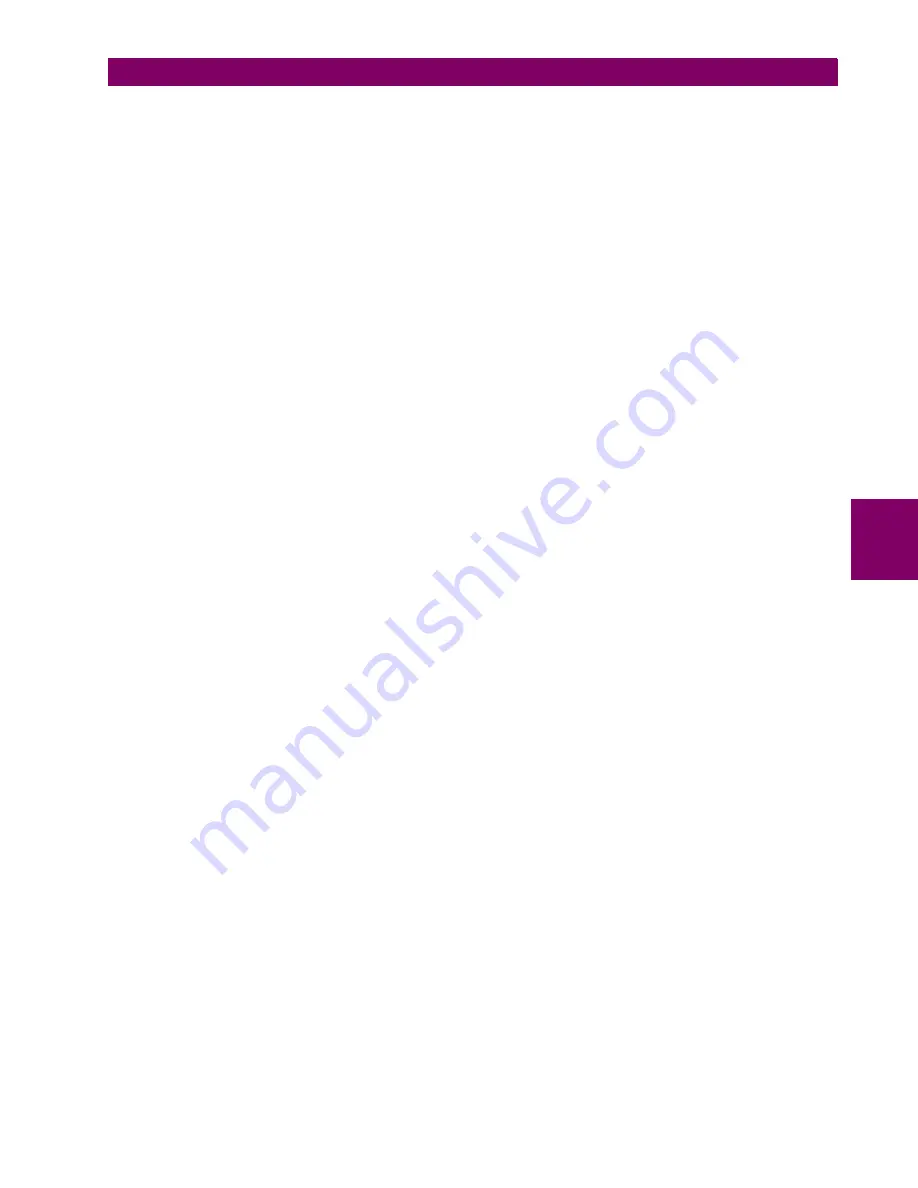
GE Multilin
M60 Motor Protection System
5-249
5 SETTINGS
5.7 CONTROL ELEMENTS
5
It is recommended that frequency tracking be enabled to avoid possible false broken rotor bar detection results when the
system frequency drifts from the nominal frequency.
The following settings are available for the broken rotor bar detection element.
•
START OF BRB OFFSET
: This setting specifies the beginning of the frequency range where the spectral component
due to a rotor bar failure will be searched. The beginning of the frequency range is defined as follows, where
f
1
is the
system frequency and
f
start_offset
is this setting.
(EQ 5.40)
If the upper sideband is to be measured, this setting should be programmed as follows, where
f
1
is the system fre-
quency and
s
is the motor slip at full load.
(EQ 5.41)
For example, if the full load slip is 0.01, program this setting as follows for a 60 Hz power system.
(EQ 5.42)
If the lower sideband is to be measured, this setting should be programmed as follows, where
f
1
is the system fre-
quency and
s
is the motor slip at full load.
(EQ 5.43)
Using the same values from previous example, this value should be programmed as follows.
(EQ 5.44)
•
END OF BRB OFFSET
: This setting specifies the end of the frequency range where the spectral component due to a
rotor bar failure will be searched. The end of the frequency range is defined as follows, where
f
1
is the system fre-
quency and
f
end_offset
is this setting
(EQ 5.45)
If the upper sideband is to be measured, this setting should be programmed as follows, where
f
1
is the system fre-
quency and
s
is the motor slip at full load.
(EQ 5.46)
For example, if the full load slip is 0.01, program this setting as follows for a 60 Hz power system.
(EQ 5.47)
If the lower sideband is to be measured, this setting should be programmed as follows, where
f
1
is the system fre-
quency and
s
is the motor slip at full load.
(EQ 5.48)
Using the same values from previous example, this value should be programmed as follows.
(EQ 5.49)
•
BRB START BLOCK DELAY
: This setting is used to block the broken rotor bar detection function while the motor is
starting for the specified time. This ensures that the broken rotor bar element is active only when the motor is running.
•
MINIMUM MOTOR LOAD
: When the motor load is less than the value specified by this setting, the data acquisition of
the broken rotor bar detection function is blocked. The broken rotor bar detection algorithm cannot accurately deter-
mine the broken rotor bar spectral component when a motor is lightly loaded.
•
MAX. LOAD DEVIATION
: When the standard deviation of the motor load is greater than the value specified by this
setting, the data acquisition of the broken rotor bar detection function is blocked. The broken rotor bar detection algo-
rithm cannot accurately determine the broken rotor bar spectral component when the motor load varies.
f
start
f
1
f
start_offset
+
=
f
start_offset
2
sf
1
max 0.3 min 2
sf
1
0.4
–
1.0
–
=
f
start_offset
2
sf
1
max 0.3 min 2
sf
1
0.4
–
1.0
–
=
2 0.01 60
Hz 0.8
–
=
0.40 Hz
=
f
start_offset
2
–
sf
1
max 0.3 min 2
sf
1
0.4
–
1.0
–
=
f
start_offset
2
–
sf
1
max 0.3 min 2
sf
1
0.4
–
1.0
–
=
2 0.01 60 Hz
–
0.8
–
=
2.00 Hz
–
=
f
end
f
1
f
end_offset
+
=
f
end_offset
2
sf
1
max 0.3 min 2
sf
1
0.4
–
1.0
+
=
f
end_offset
2
sf
1
max 0.3 min 2
sf
1
0.4
–
1.0
+
=
2 0.01 60
Hz 0.8
+
=
2.00 Hz
=
f
end_offset
2
–
sf
1
max 0.3 min 2
sf
1
0.4
–
1.0
+
=
f
end_offset
2
–
sf
1
max 0.3 min 2
sf
1
0.4
–
1.0
+
=
2 0.01 60 Hz
–
0.8
+
=
0.40 Hz
–
=
Содержание M60 UR Series
Страница 10: ...x M60 Motor Protection System GE Multilin TABLE OF CONTENTS ...
Страница 98: ...3 40 M60 Motor Protection System GE Multilin 3 3 DIRECT INPUT OUTPUT COMMUNICATIONS 3 HARDWARE 3 ...
Страница 128: ...4 30 M60 Motor Protection System GE Multilin 4 3 FACEPLATE INTERFACE 4 HUMAN INTERFACES 4 ...
Страница 238: ...5 110 M60 Motor Protection System GE Multilin 5 4 SYSTEM SETUP 5 SETTINGS 5 Figure 5 29 DISCONNECT SWITCH SCHEME LOGIC ...
Страница 410: ...5 282 M60 Motor Protection System GE Multilin 5 10 TESTING 5 SETTINGS 5 ...
Страница 413: ...GE Multilin M60 Motor Protection System 6 3 6 ACTUAL VALUES 6 1 OVERVIEW 6 FIRMWARE REVISIONS See page 6 29 ...
Страница 440: ...6 30 M60 Motor Protection System GE Multilin 6 5 PRODUCT INFORMATION 6 ACTUAL VALUES 6 ...
Страница 452: ...7 12 M60 Motor Protection System GE Multilin 7 2 TARGETS 7 COMMANDS AND TARGETS 7 ...
Страница 462: ...9 8 M60 Motor Protection System GE Multilin 9 2 BATTERIES 9 MAINTENANCE 9 ...
Страница 474: ...A 12 M60 Motor Protection System GE Multilin A 1 PARAMETER LISTS APPENDIX A A ...
Страница 584: ...B 110 M60 Motor Protection System GE Multilin B 4 MEMORY MAPPING APPENDIX B B ...
Страница 614: ...C 30 M60 Motor Protection System GE Multilin C 7 LOGICAL NODES APPENDIX C C ...
Страница 630: ...E 10 M60 Motor Protection System GE Multilin E 1 IEC 60870 5 104 PROTOCOL APPENDIX E E ...
Страница 642: ...F 12 M60 Motor Protection System GE Multilin F 2 DNP POINT LISTS APPENDIX F F ...
Страница 644: ...G 2 M60 Motor Protection System GE Multilin G 1 RADIUS SERVER CONFIGURATION APPENDIX G G ...
Страница 652: ...H 8 M60 Motor Protection System GE Multilin H 3 WARRANTY APPENDIX H H ...
Страница 662: ...x M60 Motor Protection System GE Multilin INDEX ...