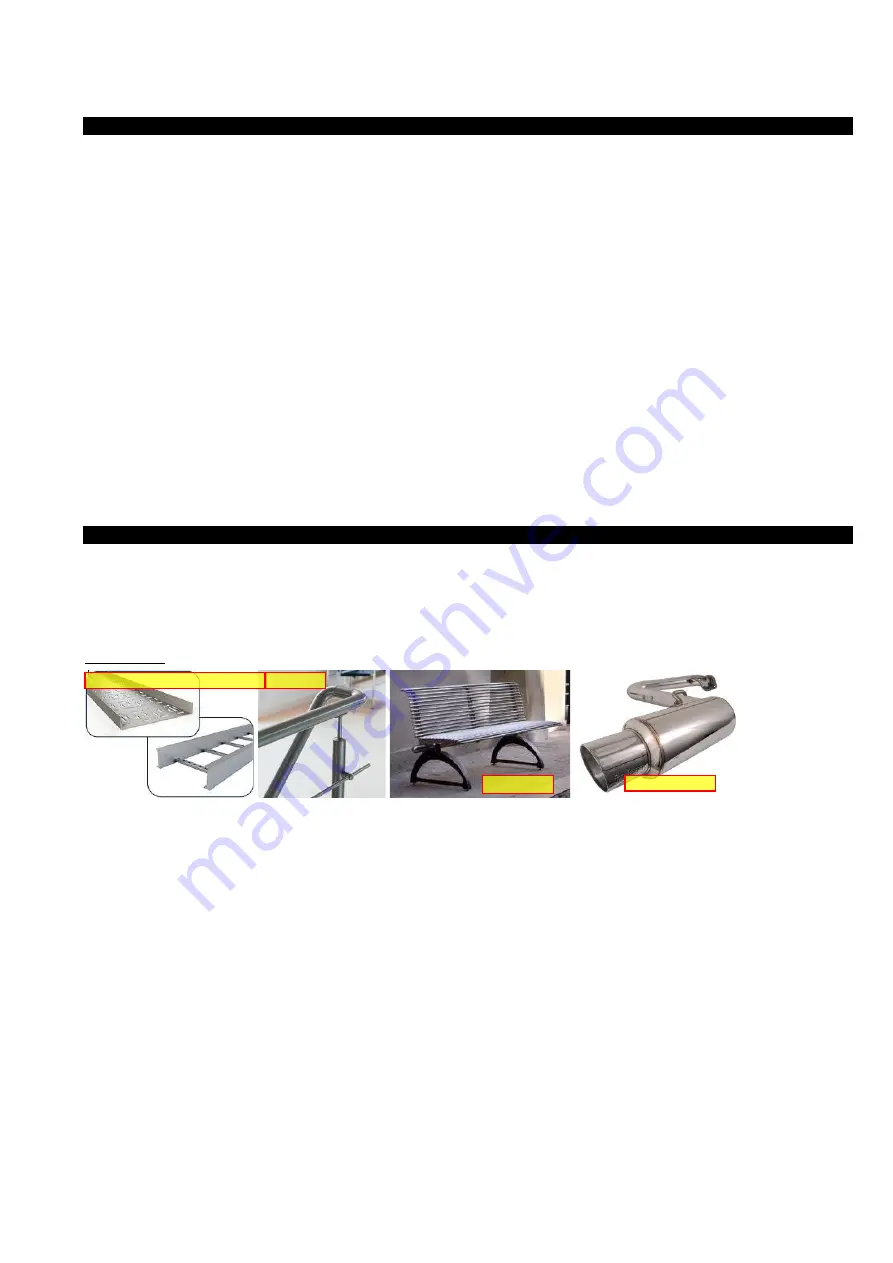
GALA PULSE SYNERGIC DR ADVANCED. Instructions Manual
69
8.4.7. STAINLESS STEELS WELDING.
In general lines, the execution of welded joints in applications with stainless steel does not differ too much from
welding carbon steels. It is true that the intensity adjustment values are similar, however, the great difference lies in
the basic need for gaseous protection or backing elements in the welding penetration.
The increasing demand by industry and especially by the chemical industry for this steel with high mechanical and
physical properties under conditions of corrosion and high temperatures, increases the demand in stainless steel
applications.
In exposure conditions at high temperatures (between 650 and 700°C) the film of oxide becomes thicker, forming an
impenetrable barrier with the high heat resistance properties that are required. However, stainless steel is stainless at
ambient temperature, but in melting conditions, it becomes a highly oxidisable material. In such a way that the effect
of the oxygen situated on the back of the joint, will accelerate its oxidising effect and chrome carbides will appear
very easily.
The welding process results in the heating and cooling of the melting area and the thermally affected area. The
duration of this heating cycle varies depending on the thickness and type of material to be welded, as well as on the
adjustment parameters used to make the bead. This heat cycle has a direct influence on the precipitation of chrome
carbides, increasing their size and speed of appearance, the longer they remain at high temperatures.
During the welding process and as a result of the increases in temperature we submit the part to, metallurgy
problems may arise that affect the weldability of these materials. The tendency to cracking, material weakening or
inter-granular corrosion are risks that we must contemplate and reduce to a minimum when welding stainless steels,
reducing the heat input as much as possible to avoid critical transformations.
8.4.8. WELDING WITH 308L Si FILLER METAL.
Its high silicon content, which improves the application of the welded deposit, achieving cleaner beads and higher
application speed, permits obtaining highly atmospheric corrosion resistant joints. Once welded, it provides surface
temperatures that vary between -196°C and 400°C.
Recommended for welding austenitic stainless steel type 304 and 304L, stabilised of type 321 and for 301, 302 and
308 joints, it is used especially when there is a risk of inter-granular corrosion.
Applications:
AIR CONDITIONING SUPPORTS RAILINGS
FURNITURE
EXHAUST PIPES