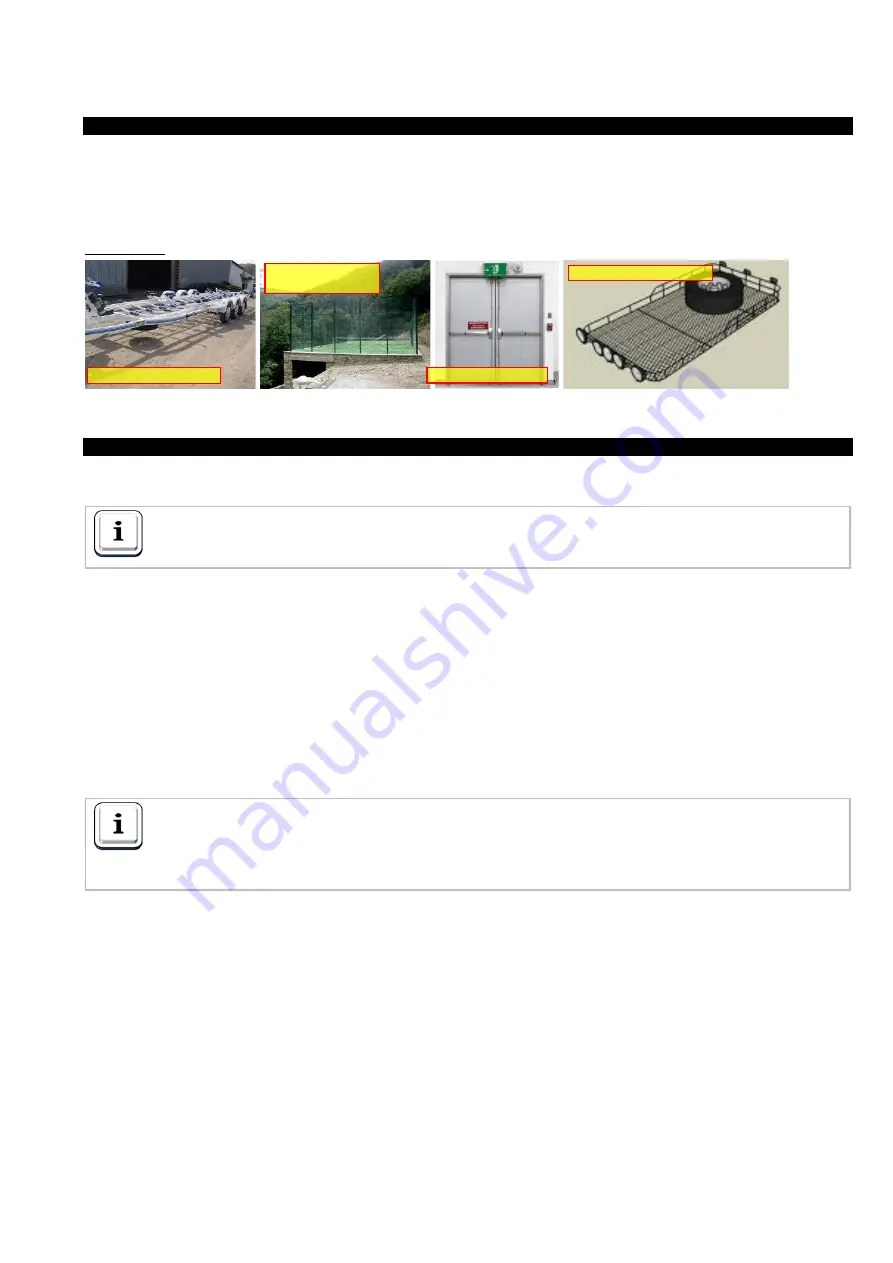
GALA PULSE SYNERGIC DR ADVANCED. Instructions Manual
72
8.4.14. WELDING WITH CuAL8 FILLER METAL.
It improves applications welded with CuSi and its joints are characterised by being mechanically resistant and
suitable for cold deformation, also having good corrosion resistance.
The resistance to atmospheric corrosion of these alloys is good; they resist corrosion in saline atmospheres well, too.
Copper aluminium joints are less sensitive than brass to corrosion under stress in ammonia atmosphere; however ,
they are more sensitive to inter-granular corrosion in the presence of overheated vapour.
Applications:
8.4.15. ALUMINIUM WELDING.
Before starting to weld, we must bear in mind the basic aspects of the material, its high heat conductivity and its low
melting point may easily produce perforations in the material due to an excess of input heat.
The amount of filler metal will permit controlling the increase in temperature and thus reduce the risk of
the material cracking.
The greater the diameter of the filler metal, the easier it is to control the melting pool.
Before starting to weld aluminium, the operators must meticulously clean the base material and eliminate aluminium
oxide and contamination by hydrocarbons coming from lubricants or cutting solvents.
It is good to remember that temperature developed by the electric arc of the MIG process is higher than the 660°C
necessary to melt the aluminium; therefore, it is important to maintain an even arc length, thermally controlling the
bead trajectory.
The technical requirement necessary to carry out this type of joint is greater than for other materials, as we must
master the process considering the fast heating speed and slow cooling speed of the material.
We must also assess the influence of the oxide film (alumina) which is formed and covers the aluminium surface in
contact with the oxygen of the air. The aluminium oxide melting temperature is 2038°C while aluminium, the base
material underneath, melts at 649°C. Therefore, any oxide that remains on the surface of the base metal will inhibit
the penetration of the metal into the piece.
To reduce the resistance of the oxides and facilitate the execution of aluminium welded joints, it is
recommended to apply previous descaling work. We can use mechanical treatments, using bristle
brushes, or specific polishing discs, or attacks with chemical products, such as solvents or descaling
agents, to destroy the high melting point oxide layer and to prevent the formation of new oxide during
the welding process.
Welding aluminium requires specific travel speeds. Unlike steel, the high heat conductivity of aluminium determines
the use of higher travel speed and intensity adjustments. If the travel speed is too low, the welder runs the risk of
perforating the plate, especially if the plate is thin.
During its hardening process and as a result of its high coefficient of thermal expansion, the increase in temperature
causes changes in the shape of the aluminium parts that may give rise to the appearance of cracks, deformation or
residual stress.
AUXILIARY TRANSPORT
SPORT EQUIPMENT
SPORT EQUIPMENT
ANTI-PANIC DOORS
AUTOMOTIVE INDUSTRY