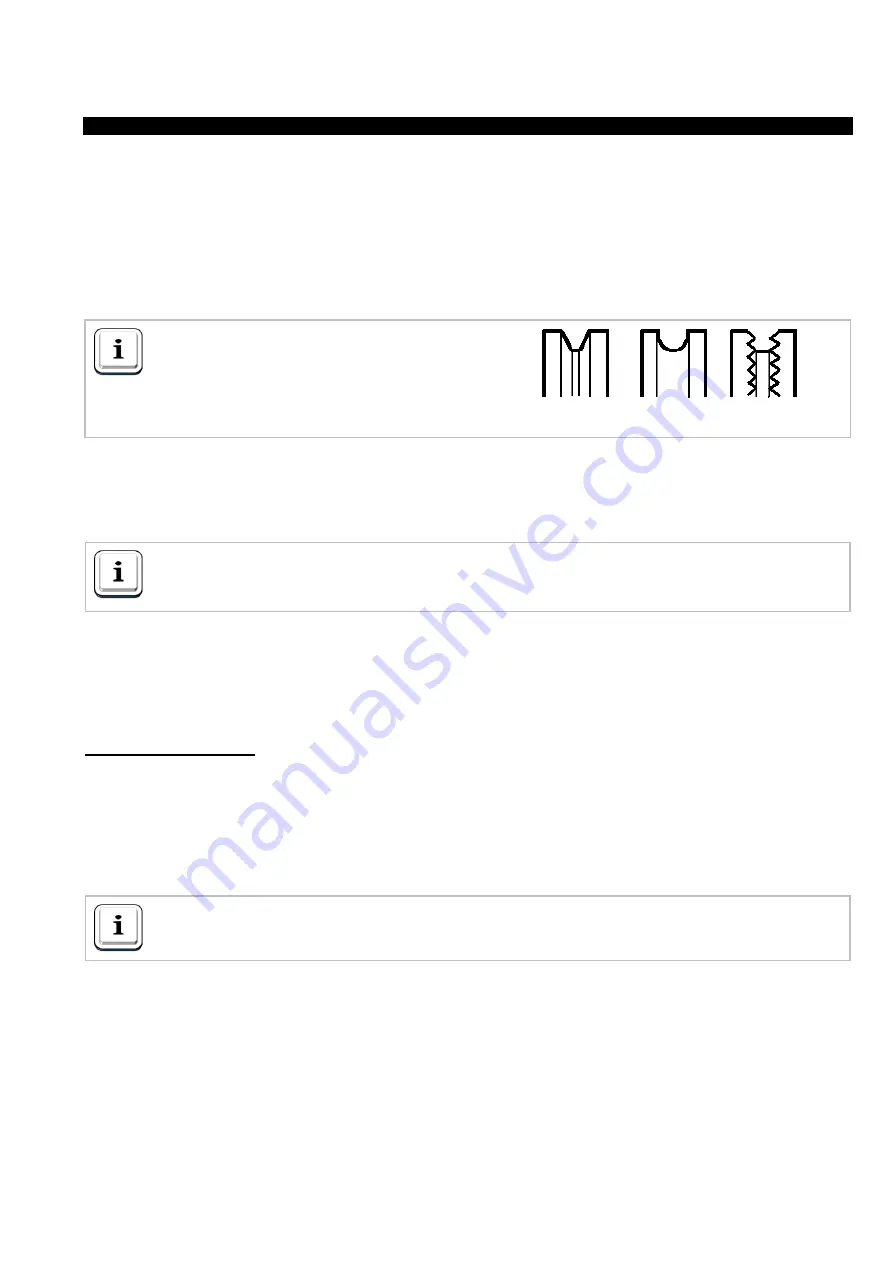
GALA PULSE SYNERGIC DR ADVANCED. Instructions Manual
64
8.3. MIG-MAG PROCESS. RECOMMENDATIONS.
Before analysing in depth the different welding options that GPS develops, we must contemplate a series of data that
have a general influence on all the work programmes.
The wires must be free from dust, grease, impurities and humidity. The metal dust adheres easily to the wire on the
reels, and may even saturate the liner of the torch giving rise to the appearance of problems. To prevent this, the
feed system must be cleaned regularly maintaining the wire in the conditions recommended by the manufacturer.
Another recommendation is to use greater diameter fillers, whenever possible, to reduce the wire feeding problems
derived.
We must use the wire feeding rollers recommended for each type of wire, verifying the state of the pressure rollers,
which with use may suffer wear and generate problems in the wire feeding process (the wire slips).
V: Carbon steel, stainless steel* and CuSi.
U: Aluminium.
Z: Flux-cored.
* If feeding problems are detected with stainless steel, replace the nearest roller to the wire reel with a grooved one (Z).
Excessive pressure of the clamping knob will be harmful for the system as we run the risk of squashing the wire,
increasing its diameter in one of these axes and increasing the resistance on the liner and varying the feed continuity.
We must continuously control the arc length (distance from the base metal to the non-melted end of the filler
material). Since the greater the electrode extension for a given intensity the greater is the deposition rate and lesser
the penetration.
Approximately 90% of the energy is concentrated in the arc and 10% in the wire, therefore, the longer
the arc the greater the tension.
The greater the end of the wire, the less the penetration will be, increasing the appearance of spatters.
Depending on the material that we wish to weld (stainless, aluminium, ...) and due to its very nature, the use of start
and end currents will be recommended (See cycle parameters).
This method is recommended to minimise the problems caused during arc-striking due to low energy input at that
time. The materials mentioned above require an increase in intensity to establish the arc in a more gentle way, thus
reducing initial spatters, excess stress and the reduction of the risk of micro cracks-cracks appearing.
PULSED ARC WELDING
Due to the basic principles of the process, the first information that we must take into consideration is the proportion
of CO
2
in the gas mix. The greater the percentage of carbon dioxide in the mix, the worse it will be to obtain the
pulse arc, and it will be difficult to obtain with percentages over 20% the total gas content.
The nature of the shielding gas itself has a direct influence on the transfer of the metal. On its own, CO
2
generates
greater penetration, it improves the physical properties of the joint and increases its resistance to impact and
corrosion. However, the active nature of the gas produces more bulky welding beads, with worse aspect and
increases the spatters.
The lower the CO2 content in the gas mix, the greater the electric arc height developed by the process.
Therefore, to compensate the modification in the arc height (ha) we must correct the arc towards
negative.