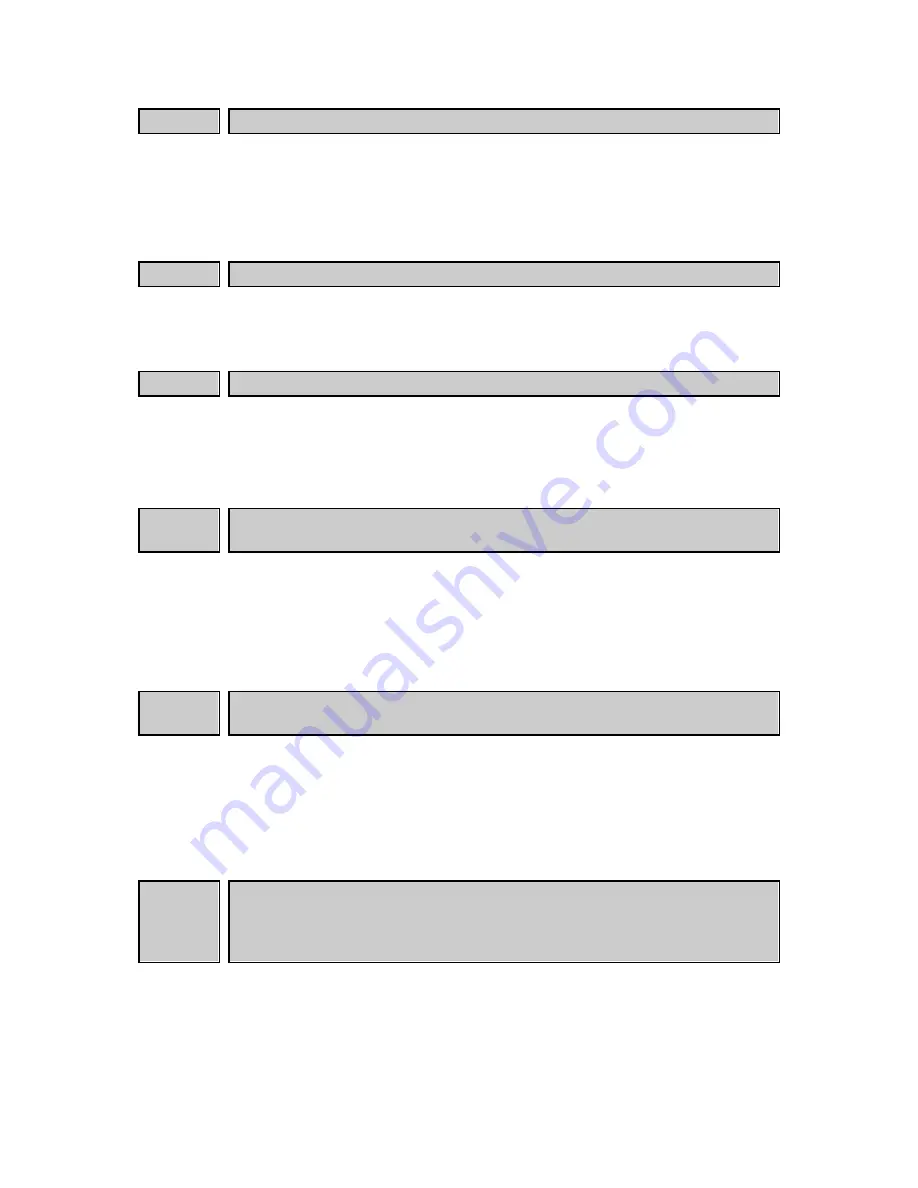
5-23
J01
PID Control (Mode selection)
J01 is used to activate the PID control of the inverter. In case of Solar Pumping application please set this function
code to 2 (inverse operation). The reason is that in this application when the PID feedback value is higher than the
PID set point value the output of the PID controller has to increase the manipulated value (inverter frequency set
point) in order to increase the power consumption of the motor, causing a reduction of the PV panel voltage (PID
feedback).
J02
PID Control (Remote command)
This parameter is used to set the source of the set point value (SV) under PID control. For Solar Pumping
application please set to 1, so that the set point value can be given from the Customized Logic program.
J06
PID Control (Feedback filter)
J06 specifies the time constant of the filter for feedback signals under PID control. In case of Solar Pumping
application the recommended value is 0.0 (s). The reason is that the PID feedback value (DC link voltage/PV panel
voltage) should not be filtered to be able to respond rapidly to changes on the PV panel conditions (especially
irradiance when changing from cloudy to sunny and opposite).
J59
J60
PID Control (P (Gain) 2)
PID Control (I (Integral time) 2)
The inverter is able to select between two PID gain sets depending on the relative values of the PID feedback and
PID set point.
J59 (P Gain 2) and J60 (Integral time 2) are used to set respectively the proportional gain and integral time of the
PID controller when the PID feedback value is higher than the PID set point value. These constants should be set
to achieve a slow response of the PID controller in order to avoid that the power drawn from the PV panel is too
high when the manipulated value (inverter set point frequency) increases.
U132
U133
PID Control (P (Gain) 1)
PID Control (I (Integral time) 1)
The inverter is able to select between two PID gain sets depending on the relative values of the PID feedback and
PID set point.
U132 (P Gain 1) and U133 (Integral time 1) are used to set respectively the proportional gain and integral time of
the PID controller when the PID feedback value is lower than the PID set point value. These constants should be
set to achieve a fast response of the PID controller in order to reduce as fast as possible the power drawn from the
PV panel.
U128
UA14
UA18
UA23
Tank level detection function (High level)
Tank level detection function (High level hysteresis width)
Tank level detection function (Signal ON Delay Time)
Tank level detection function (Signal OFF Delay Time)
The inverter can monitor the tank level by an analog signal from an analog sensor connected to terminal 12. The
inverter can also detect the tank high level by connecting the signal from a sensor to digital input [X1]. It is possible
to use either analog or digital sensor, but not both at the same time. In case of using the analog sensor, if the
detected level is higher than the value set in U128 (High level) for a time longer than the time set in UA19 (Signal
ON delay time) then the inverter will stop operation, in order to prevent the tank overflow. Also the inverter will
activate a digital output programmed to function CL01 (
TANK FULL
; E20, E21 data = 111). If the detected level is
lower than the value U128
– UA15 (High level hysteresis width) for a time longer than the time set in UA24 (Signal
OFF delay time) then the inverter will resume operation, and will deactivate the above mentioned digital function. In
case of connecting the tank high level sensor to digital input [X1], the parameters UA19 (Signal ON delay time) and
UA24 (Signal OFF delay time) also apply.
Содержание Frenic-Sce
Страница 10: ......