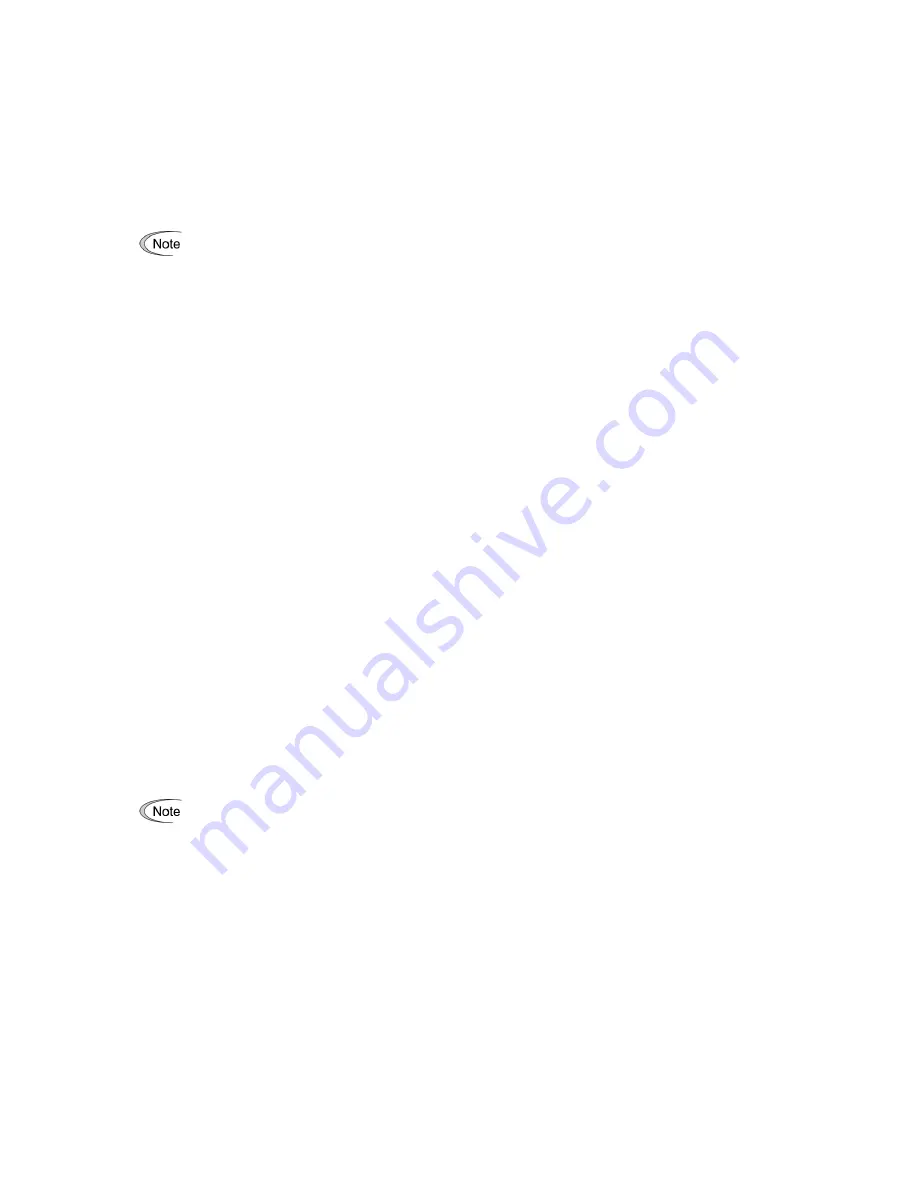
5-14
Vector control without speed sensor (dynamic torque vector)
To get the maximal torque out of a motor, this control calculates the motor torque matched to the load applied and
uses it to optimize the voltage and current vector output.
When the vector control without speed sensor (dynamic torque vector) is selected, automatically auto torque boost
and slip compensation become enabled. This control is effective for improving the system response to external
disturbances such as load fluctuations, and the motor speed control accuracy.
Note that the inverter may not respond to a rapid load fluctuation.
For slip compensation in case of vector control without speed sensor, constants of motor are used.
Therefore, satisfy the following conditions below. If these conditions cannot be satisfied, sufficient control
performance may not be obtained.
• A single motor is controlled per inverter.
• The prerequisite is that motor parameter P02, P03, P06 to P13 are accurately set or auto-tuning is
performed.
• Under vector control without speed sensor, the capacity of the motor to be controlled must be not less
than two ranks lower of the inverter capacity. Otherwise, the inverter may not control the motor due to
decrease of the current detection resolution.
V/f control with speed sensor
Applying any load to an induction motor causes a rotational slip due to the motor characteristics, decreasing the
motor rotation. Under V/f control with speed sensor, the inverter detects the motor rotation using the encoder
mounted on the motor shaft and compensates for the decrease in slip frequency by the PI control to match the
motor rotation with the reference speed. This improves the motor speed control accuracy.
V/f control with speed sensor and auto torque boost
The difference from "V/f control with speed sensor" stated above is to calculate the motor torque that matches to
the load applied, and use it to optimize the voltage and current vector output for getting the maximal torque from
the motor.
This control is effective for improving the system response to external disturbances such as load fluctuations, and
the motor speed control accuracy.
Vector control for synchronous motor without speed sensor nor pole position sensor
This control estimates the motor speed based on the inverter's output voltage and current, and uses the estimated
speed for speed control. It also decomposes the motor drive current into the exciting and torque current
components, and controls each of those components as vectors. No PG (pulse generator) interface card is
required. It is possible to obtain the desired response by adjusting the control constants (PI constants) using the
speed regulator (PI controller).
When changing function code F42 to data 15 " Vector control for synchronous motor without speed
sensor nor pole position sensor " by the keypad, then the inverter automatically updates data of F03,
F04, F05 and others.
Содержание Frenic-Sce
Страница 10: ......