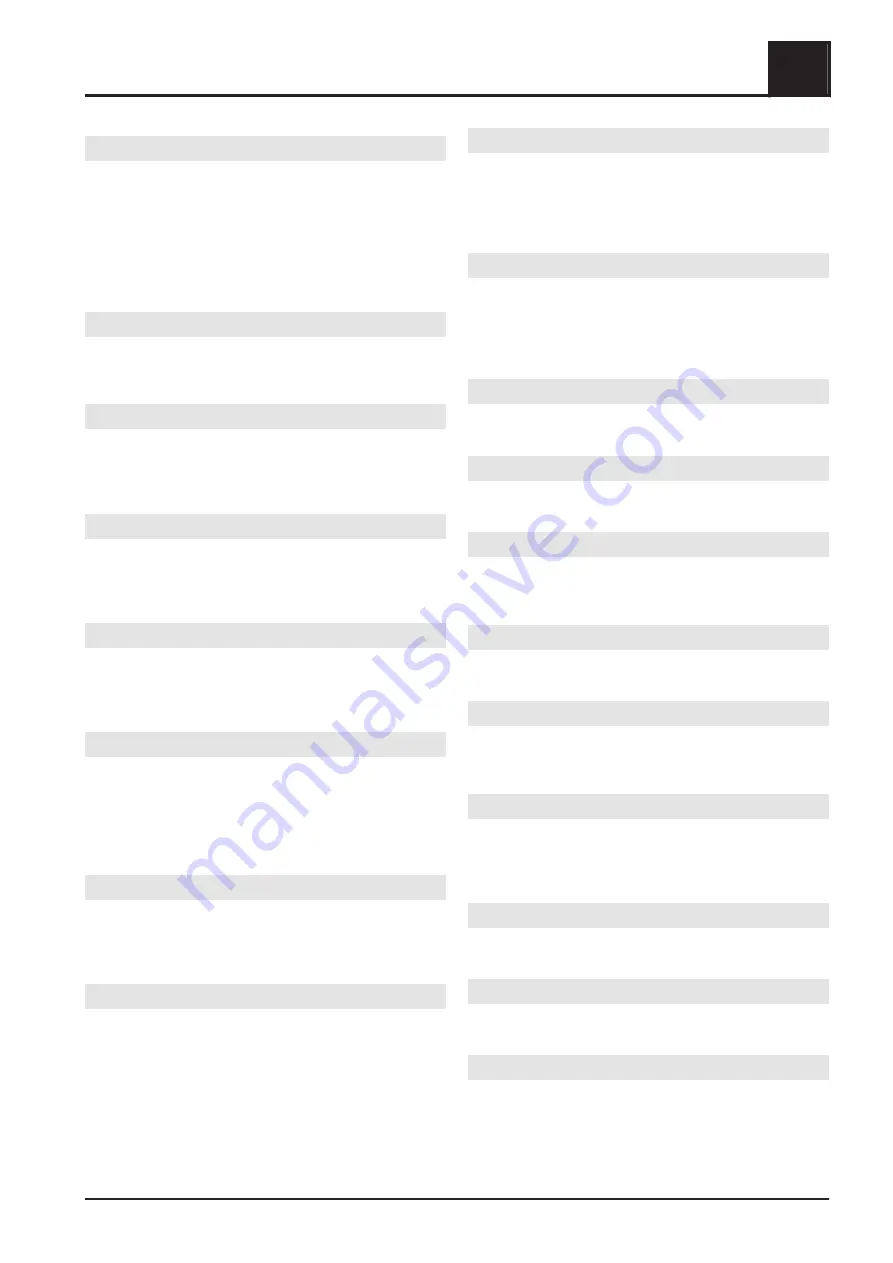
CCT signal for primary FGR stop
Specifies the stop point for the FGR primary air as a
percentage of the combustion chamber control band. The
control band is defined by the parameters "0% CCT signal
at CCT" and "100% CCT signal at CCT". Because the
FGR primary air is also dependent on the instantaneous
feed level, it is important that the FGR primary air flap is
not yet at its maximum position when this point is reached
or exceeded.
Prim. FGR decrease curve
Specifies which curve will be used to control the FGR
primary air from the stop point until the maximum
combustion chamber temperature is reached.
CCT signal for primary FGR start
Specifies the start point for the FGR primary air as a
percentage of the combustion chamber control band. The
control band is defined by the parameters "0% CCT signal
at CCT" and "100% CCT signal at CCT".
Prim. FGR increase curve
Specifies which curve will be used to control the FGR
primary air from the start point (“CCT signal for primary
FGR start” parameter) to the stop point (“CCT signal for
primary FGR stop” parameter).
CCT signal for secondary FGR start
Specifies the start point for the FGR secondary air as a
percentage of the combustion chamber control band. The
control band is defined by the parameters "0% CCT signal
at CCT" and "100% CCT signal at CCT".
CCT signal for secondary FGR stop
Specifies the stop point for the FGR secondary air as a
percentage of the combustion chamber control band. The
control band is defined by the parameters "0% CCT signal
at CCT" and "100% CCT signal at CCT". At and above this
point, the maximum possible FGR secondary air has been
reached.
Max. reduction of secondary air in FGR mode
Specifies the maximum reduction to the secondary air
when the stop point is reached (“CCT signal for secondary
FGR stop” parameter). This ensures that the secondary air
(= fresh air) is not closed off too much by the FGR.
Start of FGR control at FGR
The FGR is only activated from this set demand. If the flue
gas temperature drops by a defined value (FGR
hysteresis) after the FGR is activated, the FGR is
deactivated again.
Influence of FGR primary air on FGR control
This factor increases/decreases the effect of the FGR
primary air flap position on the pressure setpoint in the
FGR duct. It is important to note that the higher value
applies (influence of FGR primary air or influence of FGR
secondary air).
Influence of FGR secondary air on FGR control
This factor increases/decreases the effect of the FGR
secondary air flap position on the pressure setpoint in the
FGR duct. It is important to note that the higher value
applies (influence of FGR primary air or influence of FGR
secondary air).
FGR primary air opening at 0% control
Defines the minimum opening of the FGR primary air flap
and guarantees a minimum proportion of primary air.
FGR primary air opening at 100% control
Defines the maximum opening of the FGR primary air flap
and serves to limit the proportion of primary air.
FGR secondary air opening at 0% control
Defines the minimum opening of the FGR secondary air
flap and guarantees a minimum proportion of secondary
air.
FGR secondary air opening at 100% control
Defines the maximum opening of the FGR secondary air
flap and serves to limit the proportion of secondary air.
FGR secondary air opening at 0% control
Defines the position of the FGR flap at minimum control
(0% corresponds to a complete opening in the flue gas
direction to the chimney)
FGR flap opening at 100% control
Defines the position of the FGR flap at maximum control.
Please note that the way through the FGR duct flap is
limited (rotation angle approx. 51°, corresponds to the
default value of 57%).
Pressure setpoint in FGR duct at 0% FGR control
Defines the minimum pressure in the FGR duct which
must be reached at minimum control.
Pressure setpoint in FGR duct at 100% FGR control
Defines the maximum pressure in the FGR duct which
may not be exceeded at maximum control.
FGR flap control delay time
During pressure changes in the FGR duct, the control of
the FGR flap is delayed by the specified time, in order to
counter act constant vibrations.
Parameters overview
4
System
Service manual Lambdatronic H 3200 for wood chip boiler | B1480721_en
95