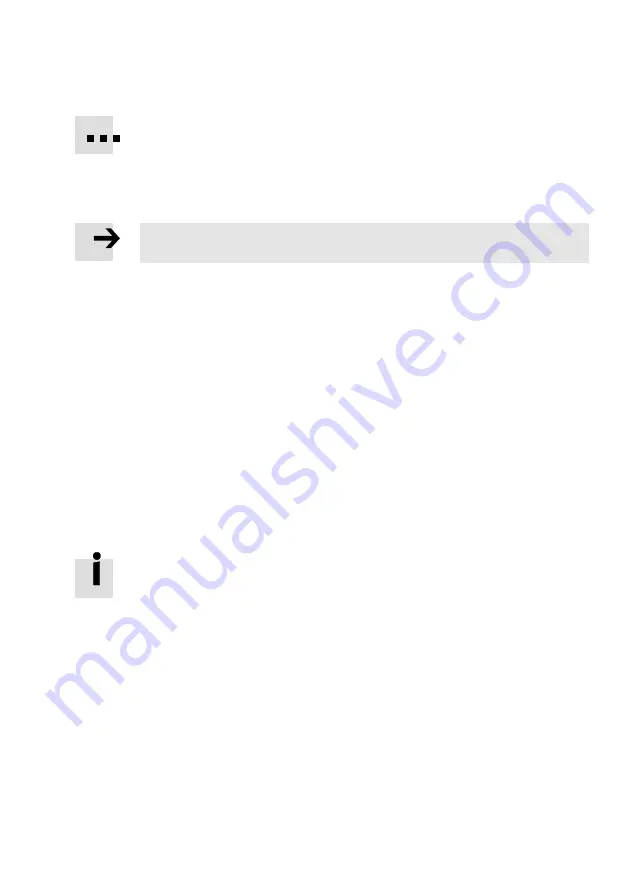
3
Mounting and pneumatic installation
Festo – P.BE-CPX-CMAX-SYS-EN – en 2017-09b – English
37
Tubing connection help for DGCI and DSMI-...-B
When ordering the DGCI with fittings – standard (not a modular system feature) or modu
lar system features QD or QR as well as for DSMI-...-B:
The fittings on the valve and drive have colour-coded release rings.
Connect the ports with blue release rings and the ports with black release rings to each other with
tubing.
Note
Check tubing connection with the movement test.
Silencers
The VPWP is available with an integrated flat plate silencer.
When using the VPWP without an integrated flat plate silencer:
Install silencers with a large nominal flow rate, e.g. UC-M5, U-1/8, U-1/4 or U-3/8 (dependent on
the valve type).
When using the VPWP with ducted exhaust air:
Guide the exhaust into a small air pressure reservoir. Exhaust the air pressure reservoir and with a
large silencer. Make sure that the fittings and tubing provide sufficient flow (shortest possible tube
length).
With correct design, this can markedly reduce the exhaust noise.
Notes on the conversion of systems
When systems are converted, the existing drives should normally continue to be used. Only drives with
one-sided air connection are often available here and the cushioning path (PPV) is also used as the
drive stroke.
In some cases, the expected positioning times cannot be fully achieved.
The specified positioning times and optimum system behaviour can only be achieved if
the installation instructions described in the previous section are observed.
Drives with compressed air supply on one side
Observe the following when using drives with air supply connection on one side:
–
Use a single-sided air supply connection only with drives with a stroke length ≤ 600 mm.
–
When air is supplied through port 4 of the proportional directional control valve, the drive must
move in a negative direction, that is, toward the zero point of the displacement encoder.
If compressed air is applied to port 2, the drive must move in a positive direction. In some cases,
arrows on the drive indicate the direction of movement. After installation, the movement test
must always be performed.
–
The resulting positioning times may vary according to the direction of the stroke.