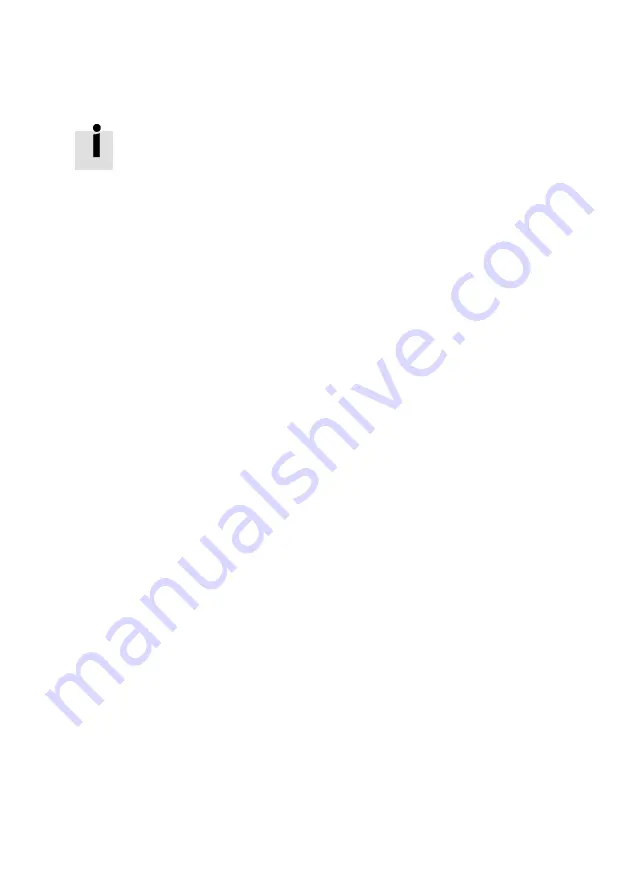
5
Commissioning
Festo – P.BE-CPX-CMAX-SYS-EN – en 2017-09b – English
55
5.4
Commissioning with the FCT (overview)
Detailed information on commissioning with the FCT
è
Help for the FCT plug-in CMAX.
Information on commissioning via the CPX node
è
Communication profile description,
P.BE-CPX-CMAX-CONTROL-....
5.4.1
Overview of commissioning steps
Preparations for commissioning
1. Check the construction of the positioning system with the components used on the axis string
(
è
2. Check power supply of the CPX terminal.
3. Install FCT and CMAX plug-in on the PC.
4. Create or open a project in the FCT. Add a new “component” with the CMAX plug-in.
The following steps are typically performed during commissioning:
Caution:
Leave the compressed air supply switched off at first.
1. Switch on power supply (
è
2. Configure FCT interface (dependent on the connection
è
3. Create device connection (online connection) between PC and CMAX via FCT.
When the CMAX is in the delivery status (display C00), the configuration wizard is automatically
started when the equipment linkage is created.
4. Parameterise application data and load into the CMAX by download:
–
Load
–
Supply pressure
–
Mounting position
These application data are the foundation for setting the controller.
5. Set additional parameters and download them into the CMAX (e.g. software end positions, record
table).
6. Switch on the compressed air supply.
7. Carry out the movement test.
8. Only for incremental displacement encoder: Perform homing.
9. Carry out identification travel.
10.Carry out test run.
After commissioning of the positioning system (
è
Communication profile description, P.BE-CPX-CMAX-
CONTROL-...) perform the following steps:
1. Configure the CPX bus node or control block (CPX-FEC, CPX-CEC).
2. Check controller of the positioning system with the CMAX.
Preliminary configuration and parameterisation (e.g. in office)
The CMAX can be preliminarily configured and parameterised even without connected components. All
necessary data must be entered for that purpose. After the valve and the displacement encoder or
sensor interface have been connected, the CMAX performs automatic hardware recognition after it is
switched on. The data recognised thereby are then accepted as setpoint configuration by the FCT if the
component data agree with those in the FCT project.