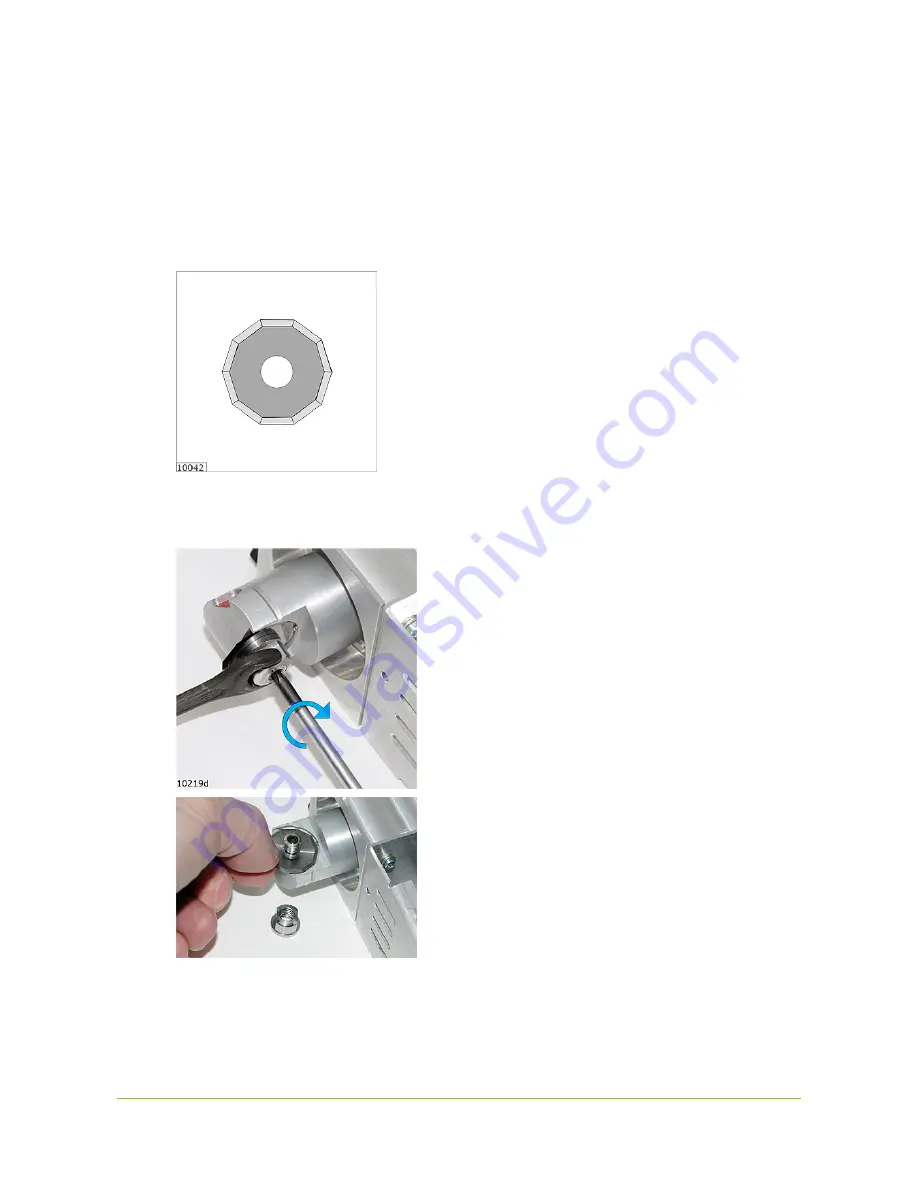
16
Kongsberg XE
The
RotaCut Knife Tool
is a special tool for cutting light materials, as thin fabric.
Maximum
Cutting Depth
is 2 mm / 0.07 inch.
Note: Due to the characteristics of this knife tool, some restrictions apply to the use of it:
• It is not suitable for curves with small diameter.
• It is not suitable for designs containing short lines in combination with sharp angles.
The
RotaCut Knife Tool
is prepared for
Decagonal Knife Blades
, ø25 mm / 1 inch.
How to replace the Knife Blade
1
Use the spanner and the hexagonal screw
driver to remove the
Knife Blade
fixing nut.
2
Carefully remove the old
Knife Blade
and
insert the new one.
Ensure the
Knife Blade
is properly seated.
Mount the nut and fix it properly.
115
Содержание Kongsberg XE10
Страница 1: ...Kongsberg XE User Manual 09 2017 Kongsberg XE ...
Страница 6: ...Kongsberg XE 20 4 i cut 133 vi ...
Страница 55: ...10 Kongsberg XE This work flow ensures exact positioning of the geometry relative to the Positioning pins 55 ...
Страница 74: ...11 Kongsberg XE The Counter function is enabled 74 ...