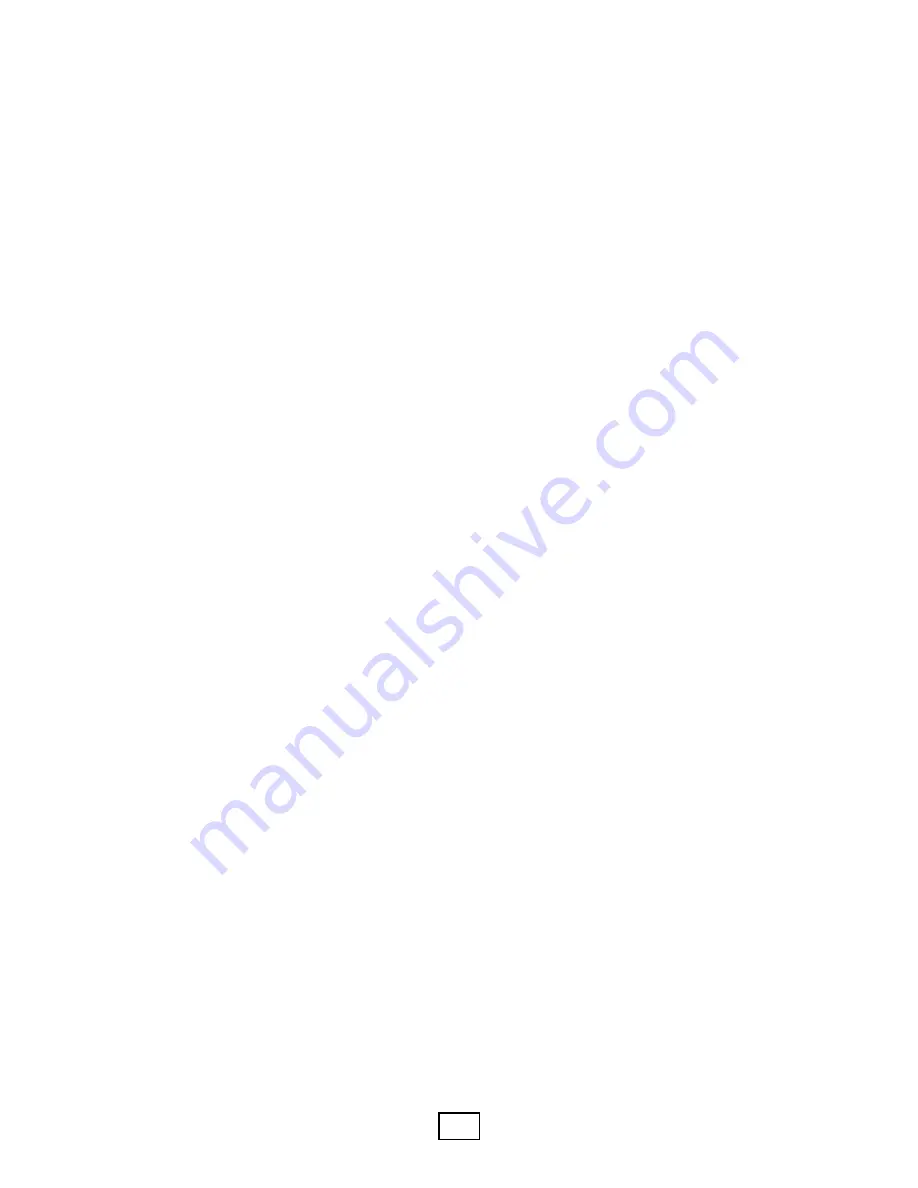
Enertech Global
87
EAV - EME/EMD Rev. A Models
Installation and Operations Manual
Sequence of Operation
Idle
The system is off and waiting for a call.
Pump Start
The load pump runs at maximum speed and the EEV (Electronic
Expansion Valve) opens completely to equalize the system and
prepare for the compressor to start. The diverting valve and
reversing valve move into position accordingly.
The reversing valve is energized only in cooling.
The diverting valve is energized only in hot water heating. This
state runs for one minute to allow temperatures and pressures
to equalize and provide relevant sensor information.
Equalization
This step is primarily a verification of conditions.
If the pressures have not equalized, the system will not continue
to the running phase. Also, the system will verify that the load
temperature does not exceed the required target temperature
(see the next section “Variable Speed Control”).
Compressor Start
The EEV moves to the starting position and the compressor
starts at the minimum speed (1650 RPM).
Run
The compressor modulates speed according to the required
load. The EEV modulates as needed to maintain 8°F superheat.
The pump modulates to maintain ΔT across the heat exchangers.
See the next section, “Variable Speed Control”, for more
information.
Compressor Stop
After all calls have been satisfied, the compressor ramps down
gradually to zero RPM.
Pump Stop
The pump maintains its current speed for one minute as it slowly
ramps down to turn off.
Note:
Zone controls must allow post purge after a call to allow
the internal load pump to stop.
ASC
The anti-short cycle timer prevents the compressor from running
for three minutes after the unit has been shut down. All calls will
be held until the ASC timer has expired. The three minute ASC is
in addition to the pump start and stop durations to provide an
industry standard five minute anti-shortcycle of the compressor.
Heat/Cool/HW Transitions
•
The compressor ramps down to minimum speed (1650
RPM) for 45 seconds. The pump will slow down as
compressor capacity ramps down.
•
The reversing valve is energized or de-energized if switching
from heating to cooling or cooling to heating. If the system
is switching from heating to hot water or hot water to
heating, the reversing valve does not change.
•
The zone valves in the Indoor Module switch from the
hydronic load to the domestic hot water tank or the zone
valves switch from DHW to hydronic heating/cooling.
•
After the valves have transitioned, the system resumes to
its normal running mode where the pump, compressor,
and EEV modulate accordingly. Note that when switching
from DHW to cooling or cooling to DHW,
the valves will not
switch to hydronic load or DHW tank if the leaving load
temperature is not within 20°F of the target temperature.
This approach eliminates hot water going to a fan coil in
cooling mode or chilled water going to the DHW tank.
When the higher priority call is satisfied, and there is still a call
holding, the system will transition back to the original call in the
same manner. The compressor is able to continue running and
thus no ASC delay is experienced.
Variable Speed Control
The use of the variable speed compressor and pump includes
advanced control algorithms to match the load demand of the
space. The control described here takes place during the “Run”
portion in the system sequence of operation described in the
previous section.
Compressor
Control of the compressor is based on the target outlet
temperature of the system. The system monitors the current
load out temperature and compares to the target temperature.
Using the control algorithm, the system seeks to maintain the
exact target outlet temperature. Outlet temperature above or
below the target temperature causes the compressor to throttle
faster or slower as needed. In radiant floor heating, with an
outdoor thermistor, the outdoor reset dictates the targeted load
temperature. In cooling and hot water, the static menu settings
control the target temperature.
This control allows the system to react to changing conditions.
As zone valves open and close, the compressor speed is adjusted
to meet the current demand.
In some small load situations, such as very small radiant zones,
the system may not be able to run slow enough to avoid thermal
runaway. To accommodate this situation, the compressor can
shut down when the load outlet temperature over/under shoots
its target by 4°F. During this time, the pump will continue to
circulate and the ASC timer is started.
The compressor will be cycled on again when the ASC timer
expires AND the outlet temperature has dropped below the
target temperature. All priorities are still obeyed during this
time. If the call becomes satisfied the system will shut down
normally.
Note:
It is recommended to size zones in order to avoid this
cycling condition. It is preferred to avoid compressor cycling and
improve efficiency.
Pump
When the pump is in “auto” mode, it controls to maintain ΔT
(Default 5°F) across the heat exchangers. To do so, load entering
and leaving temperatures are continually monitored. A sensed
ΔT above the 5°F setpoint will cause the pump to run faster.
Below the setpoint causes the pump to run slower – down to the
set minimum speed.
Note
: If, after setup, the EME/EMD detects the minimum flow
rate allows less than 5.0 GPM, it will attempt to increase the
minimum flow percentage until 5.0 GPM is achieved. This will
overwrite the previous minimum setting.
Section 9: On-Board Controls