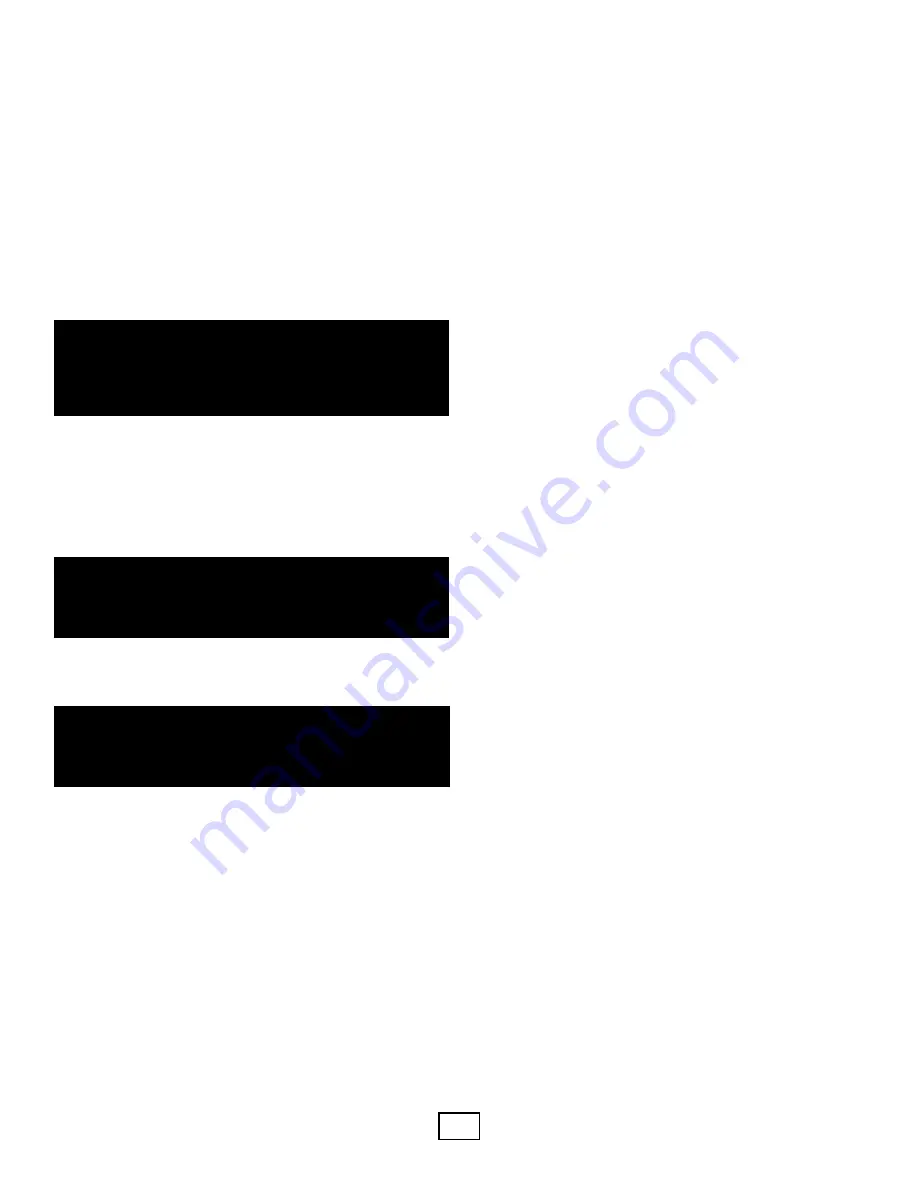
Enertech Global
54
EAV - EME/EMD Rev. A Models
Installation and Operations Manual
Load Side Antifreeze
If the unit will be used for cooling, antifreeze must be added
on the load side of the system to protect the braze plate heat
exchanger from rupturing. Chilled solution set points are in the
40’s °F. The load solution so within the heat exchanger, could be
near freezing. To protect against freezing. Enertech recommends
the use of Propylene Glycol (20-25%) for the load side antifreeze.
Additional inhibitor may be required if the concentration is less
than 25% to 30% (depending upon brand) to provide corrosion
protection and prevent bacterial growth.
Important:
Propylene glycol concentrations below 30% typically
require additional inhibitors to be added to the solution.
Enertech recommends Fernox F1. Reference
Figure 14 and
Tables 4 to 6
for additional antifreeze information.
Note:
The minimum recommended air handler size is 2 tons.
Flushing and Filling (see next page for drawings)
The system needs to be flushed of air and debris, and filled
before it is turned on and put into service. All systems have dirt
and debris from the piping, soldering, etc. Enertech
recommends using a flush cart to the purge the system. The
flush cart should utilize a ½ HP pump, which is sufficient for
almost all residential hydronic systems, as long as each circuit is
isolated and flushed one at a time.
First, isolate each circuit, including the heat pump and domestic
hot water tank. Then, flush each zone of air, and fill each zone
with water (radiant tubing, air handler, etc.).
Third, open the isolation valves and flush/ fill the heat pump,
making sure that the water flow direction is as it would be in
normal operation.
Note:
Water flow direction is crucial during this step. If the
water flow is backwards, the Wye Strainer is not protecting the
braze plate heat exchangers from the miscellaneous debris that
hasn’t been flushed out into the flush cart.
Once the entire system has been flushed and filled, the
antifreeze and water treatment can be added, using the flush
cart to add and mix the treatment. All zones should be open
during this process, so that proper mixing can take place.
Take multiple readings, and check the antifreeze percentage, as
the system is being mixed. The final step is to go through the set
up wizard on the controller (HMI) to energize the diverting valve
(if equipped) and verify that the last bit of air is removed from
the system.
See Section 9 for additional details
. Once
completed, the flush cart can be removed from the system.
Note:
If any small amount of air is still in the system, the air
elimination device will remove it and the make-up water, as well
as the expansion tank, will keep pressure on the system.
Recommended pressure setting is 12-17 PSI cold = 15-19 PSI hot.
The entire system is now flushed, filled, treated, and ready to be
put into operation.
Water Quality
Enertech recommends that all hydronic systems water be tested
prior to being used in any installation.
Water quality is important for the Load side of the system. Due
to use of dissimilar metals throughout the system (i.e. stainless
braze plates, cast iron pump volutes, etc.) certain minerals or
chemicals may build up and become detrimental to system
operation and longevity. Filling the system with good quality
water that meets the specifications outlined in
Table 3.
The quality of the water used in hydronic systems is very
important. In closed loop systems the dilution water (water
mixed with antifreeze) must be of high quality to ensure
adequate corrosion protection. Water of poor quality contains
ions that make the fluid “hard” and corrosive. Calcium and
magnesium hardness ions build up as scale on the walls of the
system and reduce heat transfer. These ions may also react
with the corrosion inhibitors in glycol based heat transfer fluids,
causing them to precipitate out of the solution and rendering
the inhibitors ineffective in protecting against corrosion. In
addition, high concentrations of corrosive ions, such as chloride
and sulfate, will eat through any protective layer that the
corrosion inhibitors form on the walls of the system.
Ideally, de-ionized water should be used for dilution with
antifreeze solutions since de-ionizing removes both corrosive
and hardness ions. Distilled water and zeolite softened water are
also acceptable. Softened water, although free of hardness ions,
may actually have increased concentrations of corrosive ions
and, therefore, its quality must be monitored. The Department
of Natural Resources or your local municipality can direct you to
the proper testing agency. Please see
Table 3
for guidelines.
Also, once the system has been flushed and filled, Enertech
recommends the use of Fernox F1 (Enertech P/N: F-57880)
water treatment products in order to keep the system clean and
running smooth for years to come.
Second, open the isolation valves and flush/ fill the hot water
tank (if equipped), making sure to keep the system pressure
below 30 PSI. If the pressure gets above 30 PSI, the relief valve
on the tank will purge water. Once this step is complete, close
the isolation valves.
Note:
This step can be skipped if the unit is not equipped with
hot water capability.
⚠
WARNING
⚠
IF MORE THAN 30% ANTIFREEZE IS ADDED, HEAT
TRANSFER AND VISCOSITY ISSUES MAY ARISE. BE
SURE TO KNOW WHAT TYPE OF ANTIFREEZE IS BEING
USED, AND IF IT IS PURE OR PRE-MIXED.
⚠
WARNING
⚠
USING JUST THE ON-SITE CITY OR WELL WATER
PRESSURE, WILL NOT FLUSH THE AIR AND DEBRIS OUT
PROPERLY FROM THE SYSTEM.
⚠
WARNING
⚠
MAKE SURE TO ISOLATE THE DOMESTIC WATER TANK
BECAUSE THE RELIEF VALVE INSTALLED IN THE TANK
WILL PURGE WATER AS THE SYSTEM IS FLUSHED.
Section 7: Water Quality & Antifreeze