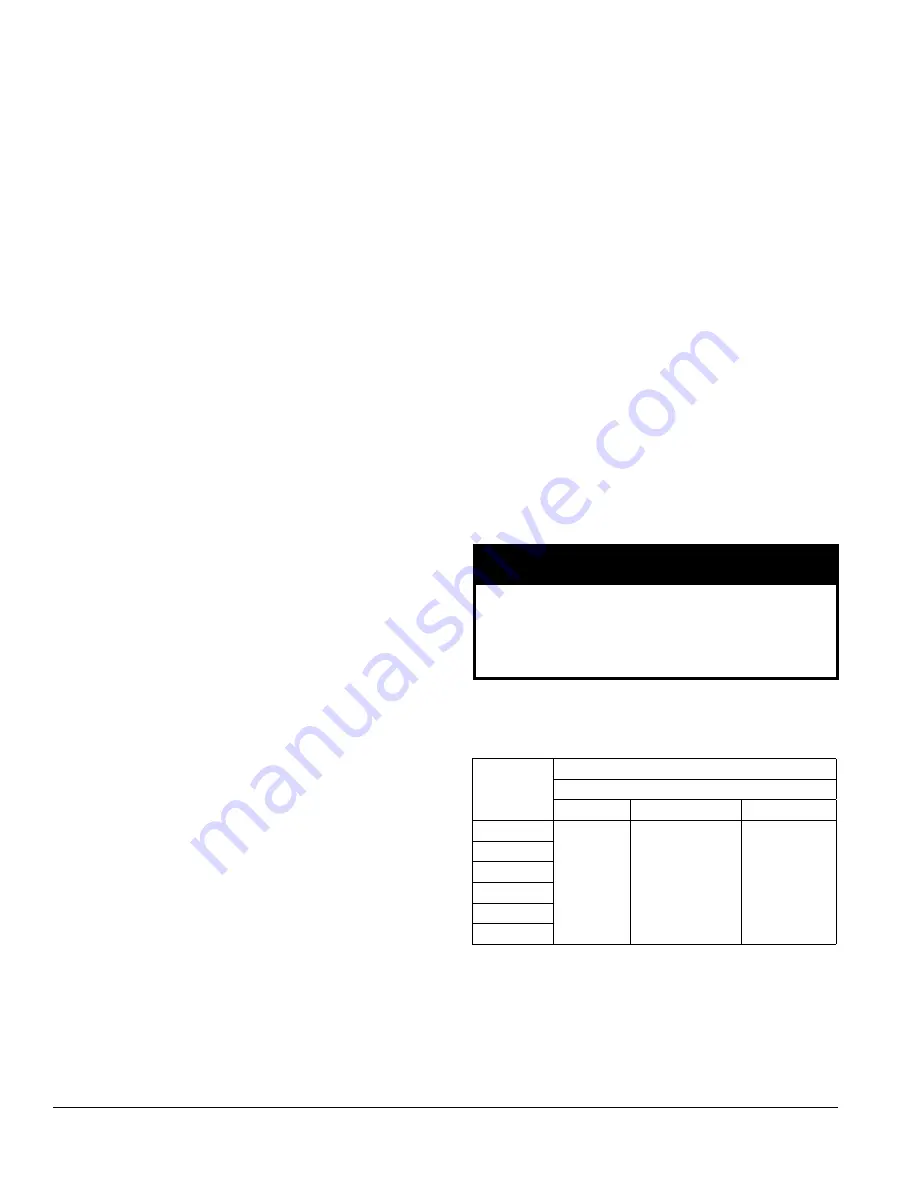
86
103448-02 - 6/13
5. Obtain gas-heating value (Btu per cubic foot) from
gas supplier.
6. Multiply hourly gas flow rate by gas heating value
to determine the boiler input rate, BTU/hr
Example:
Natural gas heating value provided by local gas
utility is 1050 Btu per cubic foot.
Measured and calculated hourly gas flow rate is 100
cu ft/hr.
Measured boiler input rate is:
100 cu ft/hr x 1050 BTU/ cu ft = 105, 000 BTU/hr
7. Compare measured input rate to input rate value
stated on rating label. Strive to adjust the boiler
input rate within 88% to 100% of the value listed on
the boiler rating label.
8. If measured input is too high, reduce input rate by
rotating gas valve throttle screw clockwise (see
Figure 53) in ¼ turn increments and checking the
rate after every adjustment until the measured input
rate value falls within 88% to 100% of the value
listed on the boiler rating label.
9. If measured input is too low, increase input rate by
rotating gas valve throttle screw counterclockwise
(see Figure 53) in ¼ turn increments and checking
the rate after every adjustment until the measured
input rate value falls within 88% to 100% of the
value listed on the boiler rating label.
10. Once the boiler input rate adjusted/confirmed,
recheck main burner flame and perform combustion
test as described below (see Paragraph M “ Perform
Combustion Test”).
11. Upon completion, return other gas-fired appliances
to previous condition of use.
M.
Perform Combustion Test
Boilers are equipped with Flue Temperature Sensor
installed into:
• Flue sensor port of boiler CPVC/PVC two-pipe
vent system connector (floor standing build) -
See Figures 6 and 17.
• Flue sensor port of vent elbow, located inside air
box behind access panel (wall hung build) - see
Figure 7B.
• Flue sensor port of boiler concentric vent collar
(floor standing build) - see Figure 18.
Remove Flue Temperature Sensor and insert the
analyzer probe through Flue Temperature Sensor
silicon cap opening, or if required, remove also the Flue
Temperature Sensor silicon cap and insert the analyzer
probe directly into flue sensor port. Reinstall the sensor
and the cap upon combustion testing completion.
Check CO
2
(or O
2
) and CO at both high and low fire.
The boiler may be locked into high or low fire as
follows:
1. To lock the boiler in high fire, enter the Manual
Control screen by first entering the Adjust screen.
To access the Adjust screen, touch the Adjust button,
then Login using the
contractor password “076”
.
Press Save and then select the adjust button. Enter
the Manual Control button and select “High”.
Allow the boiler to operate for approximately 5
minutes before taking combustion readings.
2. To lock the boiler in low fire select “Low” from
the Manual Control screen. Allow the boiler to
operate for approximately 5 minutes before taking
combustion readings.
3. Normal modulation of the boiler will only occur
after the “Auto” button is selected in the Manual
Control screen.
Typical CO
2
values for natural gas are shown in Table
26.
Typical CO
2
values for LP gas are shown in Table 27.
If actual combustion readings are outside of typical
values shown, contact factory for assistance.
Warning
Each alpine Series boiler is tested at the factory
and adjustments to the air fuel mixture are
normally not necessary. improper gas valve or
mixture adjustments could result in property
damage, personal injury, or loss of life.
Boiler
Model
altitude range
0 - 7000 Ft.
% CO
2
% O
2
range
CO, PPM
ALP080B
9.9 - 8.2
(High Fire)
9.9 - 7.9
(Low Fire)
3.5 - 6.5
(High Fire)
3.5 - 7.0
(Low Fire)
Less than
100 PPM
ALP105B
ALP150B
ALP210B
ALP285B
ALP399
Table 26: Typical Combustion Values, natural gas
iX. System Start-up
(continued)
Содержание ALP080B
Страница 72: ...72 103448 02 6 13 VIII Electrical continued ...
Страница 73: ...103448 02 6 13 73 VIII Electrical continued Figure 43 Wiring Connections Diagram ...
Страница 75: ...103448 02 6 13 75 VIII Electrical continued Figure 44 Ladder Diagram ...
Страница 136: ...136 103448 02 6 13 U S Boiler Company Inc P O Box 3020 Lancaster PA 17604 1 888 432 8887 www usboiler net ...