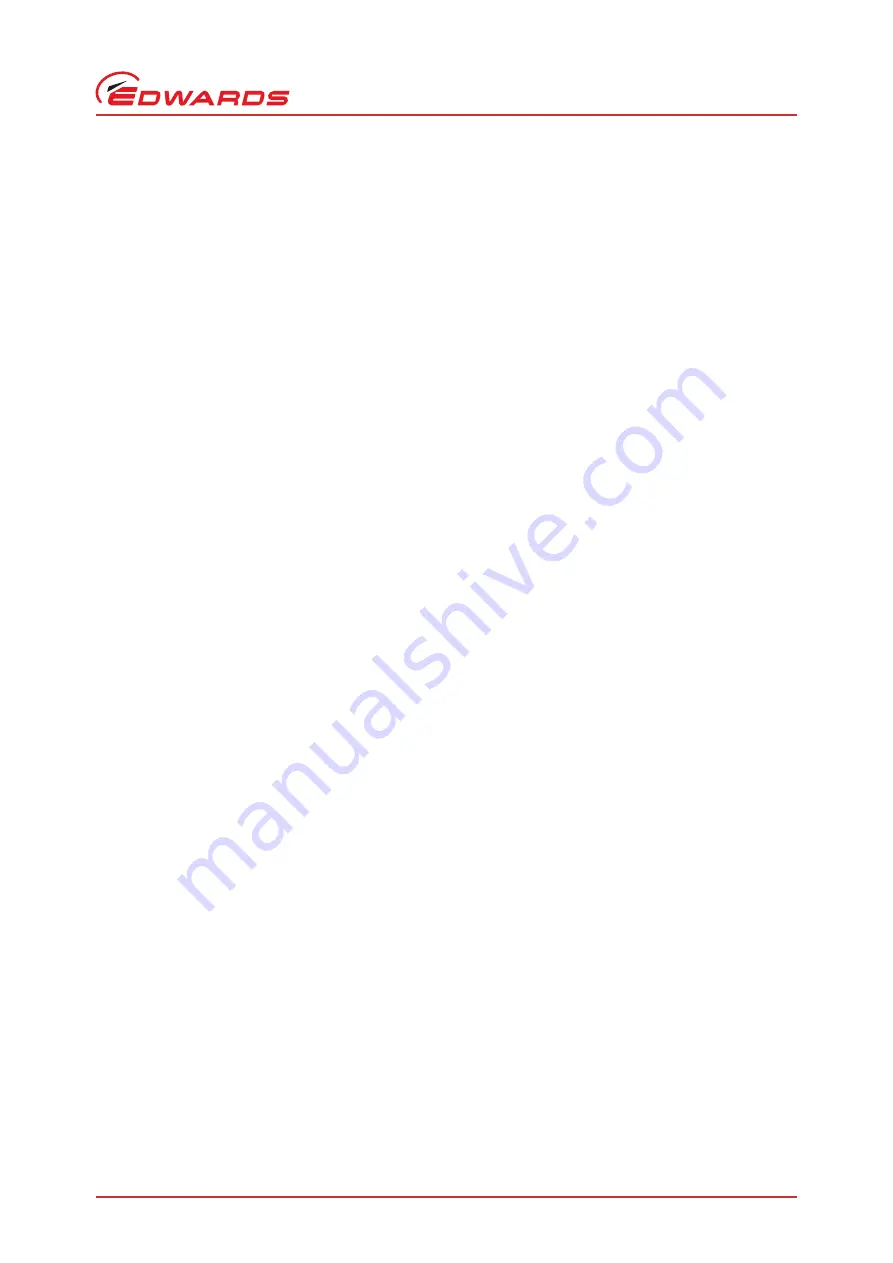
© Edwards Limited 2009. All rights reserved.
Page 5
Edwards and the Edwards logo are trademarks of Edwards Limited.
INTRODUCTION
A533-23-880 Issue C
1.6
The HMB mechanical booster pump
The HMB pump is a positive displacement roots vacuum pump. The pump mechanism is driven by a three-phase
electric motor. The HMB pump in the iF1800 system is driven through an electrical inverter, which increases the
speed of the motor to 6000 r min
-1
.
The FDP pump backs the HMB pump:
The HMB pump in an iF1800 system operates between atmospheric pressure and ultimate vacuum; when you
start the FDP pump, the HMB pump starts after 30 seconds.
1.7
Temperature control system
1.7.1
FDP pump temperature control system
The FDP200 employs a direct cooling method, having the water circulating through the pump body such as casing,
gear case and bearing case.
The pump-motor is cooled by water, which flows through a cooling jacket which surrounds the motor. The cooling-
water supply and return pipelines are connected to the iF system by connectors at one end (Figure 4, items 2 and 3).
The cooling-water is distributed via the pump cooling circuit to the pump-motor cooling jacket before joining the
outlet of the HMB cooling circuit.
A surface temperature sensor is fitted to the pump-body to measure the temperature of the pump-body. The output
of the thermocouple is monitored by the iF system, refer to Section 1.9.3.
For safety reasons, a shutdown thermistor is fitted to the pump-motor cooling outlet. It is connected to the relay
interlock circuit, and will cause the iF system to shut down if the temperature exceeds 60
o
C.
A motor protection thermistor and a snap switch are fitted to the pump motor. The thermistor operates at 130
o
C and
the snap switch at 155
o
C. Both are connected to the relay interlock circuit and will shut down the iF system if the
pump motor gets too hot.
1.7.2
HMB pump temperature control system
The headplate and front bearing housing of the HMB pump are directly cooled by water, which flows around these
parts of the pump. The solenoid valve in the water system provides cooling to the HMB outlet when required. The
pump-motor is cooled by water, which flows through a cooling jacket that surrounds the pump-motor. The pump-
motor cooling-water supply and return pipelines are connected to the cooling-water manifold on the FDP pump.
A motor-protection thermistor is fitted to the HMB1800 pump-motor. This thermistor is similar to that fitted to the
FDP pump (refer to Section 1.7.1). The thermistor is connected to the relay interlock circuit and will cause the system
to be shut down if the pump-motor is too hot.
A temperature sensor probe (Figure 5, item 15) is fitted in the stator of the pump. The output of the sensor is
monitored by the iF control system. The output is used to operate the water solenoid valve. It is also used to slow
the HMB down if the pump temperatures become too high.
1.8
Exhaust system
The outlet of the FDP pump is connected to an exhaust silencer, which is below the pump. The outlet of the silencer
has a check-valve which prevents the suck-back of exhaust vapours after the iF system is shut down. The check-valve
also provides additional attenuation of the pulses in the exhaust pressure. If required, you can remove the check-
valve for your specific process (refer to Section 3.9).