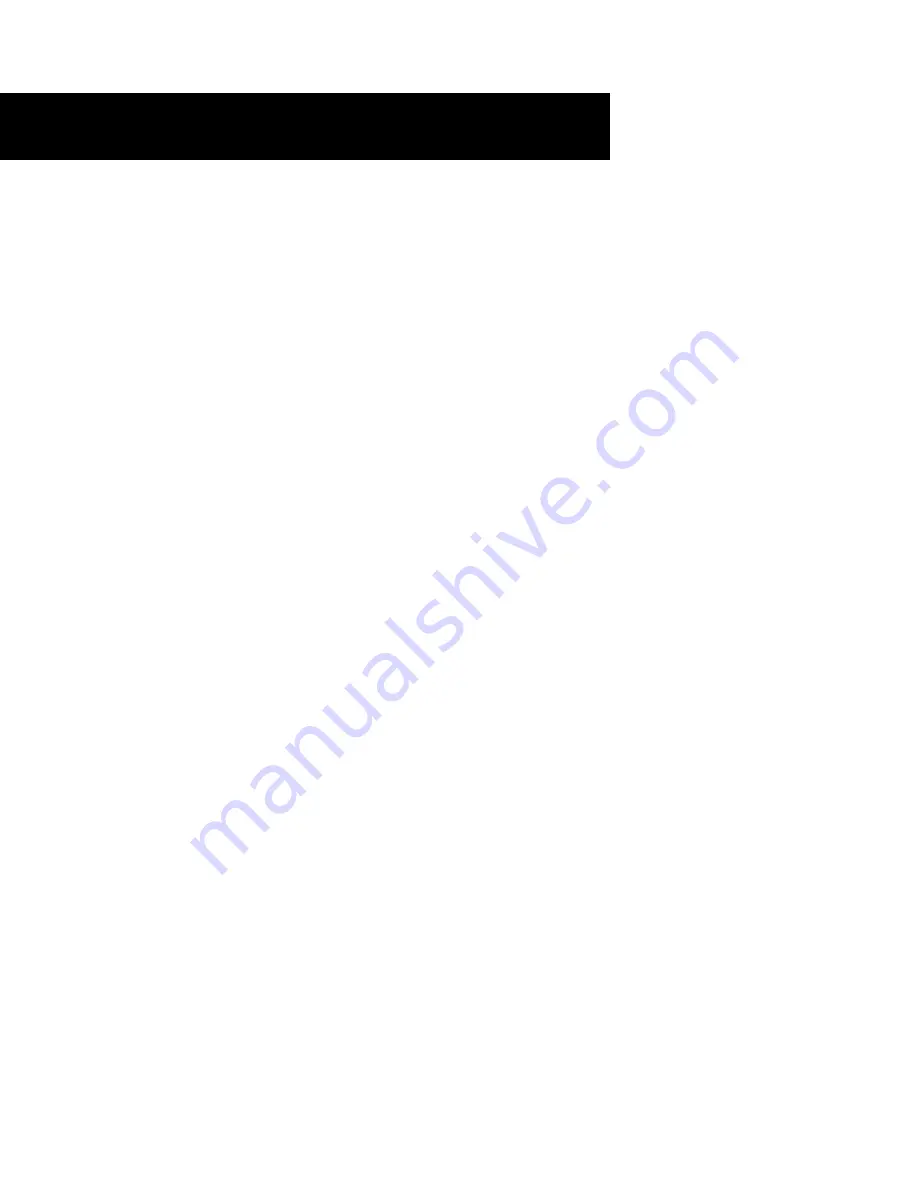
K. Synchronizers
1. Check high and low range synchronizers for
burrs, uneven and excessive wear at contact sur-
face, and metal particles.
2. Check blocker pins for excessive wear or loose-
ness.
3. Check synchronizer contact surfaces on the
high and low range gears for excessive wear.
L. Sliding Clutches
1. Check all yokes and yoke slots in sliding
clutches for wear or discoloration from heat.
2. Check engaging teeth of sliding clutches for
partial engagement pattern.
M.
O-Rings
1. Check all O-rings for cuts, cracks or distortion.
Replace if worn.
REASSEMBLY
Make sure that interiors of case and housings are
clean. It is important that dirt be kept out of trans-
mission during reassembly. Dirt is abrasive and
can damage polished surfaces of bearings and
washers. Use certain precautions, as listed below,
during reassembly.
1. GASKETS -
Use new gaskets throughout the
transmission as it is being rebuilt. Make sure all
gaskets are installed, as omission of gasket can
result in oil leakage or misalignment of bearing
covers. See "Location of Gaskets" heading.
2. CAPSCREWS - To prevent oil leakage, use
thread sealant on all capscrews. See torque rating
chart for recommended torque.
3. O-RINGS - Lubricate all O-Rings with silicone
lubricant.
4. ASSEMBLY - Refer to the disassembly illustra-
tions as a guide to reassembly.
5. INITIAL LUBRICATON - Coat all thrust washers
and splines of shafts with Lubriplate during instal-
lation to provide initial lubrication, preventing
scoring and galling.
6. AXIAL CLEARANCES - Maintain original axial
clearances of mainshaft forward speed gears of
.005" to .012". Mainshaft reverse gear clearance is
a minimum of .005".
7. BEARING - Use of flanged-end bearing drivers
is recommended for the installation of bearings.
These drivers apply equal force to both races of
bearing, preventing damage to balls and races and
maintaining correct bearing alignment with shaft
and bore. If tubular or sleeve type driver is used,
apply force only to inner race.
8. UNIVERSAL JOINT COMPANION FLANGE -
Pull the companion flange tightly into place with
the mainshaft nut, using 400-450 foot-pounds of
torque. Make sure the speedometer gear has been
installed on yoke. If a speedometer gear is not
used, a replacement spacer of the same width
must be used. Failure to pull the yoke or flange
tightly into place will permit the shaft to move
axially with resultant damage to rear bearing.
9. TORQUE - As you reassemble transmission,
refer to pages 12 and 13 for proper installation
torque of capscrews, nuts and plugs.
23
PRECAUTIONS
Содержание TRSM0515
Страница 1: ...Service Manual Fuller Heavy Duty Transmissions TRSM0515 October 2007...
Страница 4: ...DESCRIPTION...
Страница 10: ...PREVENTATIVE MAINTENANCE CHECK CHART...
Страница 11: ...TORQUE RECOMMENDATIONS...
Страница 12: ...Cut 7191D 7 84 TORQUE RECOMMENDATIONS...
Страница 13: ...AIR SYSTEM...
Страница 25: ...IX GEAR SHIFT LEVER HOUSING I SHIFTING CONTROLS...
Страница 87: ......