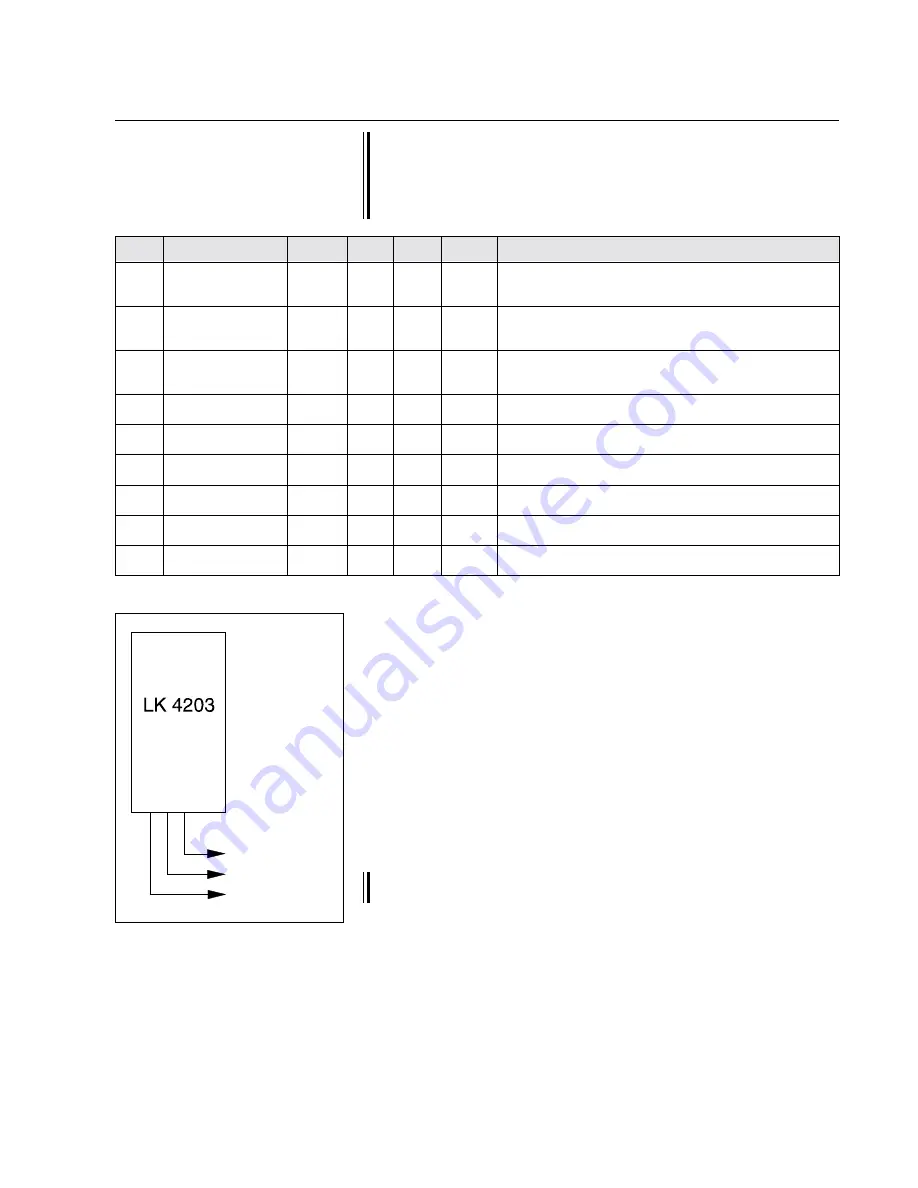
U Page 57
Digital controller RK 4004
5.3 "Three position controller"
upgrade
No.
Name
Default
Min.
Max.
Unit
Description
.1.3.
puls range ±
2.0
0.0
2000.0
mm
Switching threshold for transition
Stop at pulse output
.1.4.
slow range ±
4.0
0.0
2000.0
mm
Switching threshold for transition
Pulse output to permanent signal
.1.5.
fast range ±
6.0
0.0
2000.0
mm
Switching threshold for transition
Permanent signal to fast signal
.1.6.
hysteresis
1.0
0.0
2000.0
mm
Hysteresis of the individual switching thresholds
.1.7.
pulse ON-time
1.0
0.0
10.0
sec
Switch-on time of pulse signal
.1.8.
pulse OFF-time
1.0
0.0
10.0
sec
Switch-off time of pulse signal
.1.9.
jog with fast
0
0
1
Jog mode with fast signal
.2.0.
dig. I/O adress
0
0
7.F
hex
Address of digit. output card for the positioning signals
.2.1. •
act. control out
Display of the current positioning signal
Output:
"Right"
"Left"
"Fast"
For control card applications as a three position controller the va-
lue 32 must be entered in parameter "..3. start service" during
control card commissioning. This loads the three position control-
ler parameter record. The three position controller parameters that
differ from the norm are described below.
.1.3. puls range ±
(switching threshold 1)
.1.4. slow range ±
(switching threshold 2)
.1.5. fast range ±
(switching threshold 3)
The three position controller software features 3 switching thresholds.
Switching threshold 1pulsed "Right" or "Left" output
Switching threshold 2 "Right" or "Left" output duration
Switching threshold 3 "Fast" output duration
The "Fast" output is switched to threshold 2.
The switching thresholds should be entered in the appropriate para-
meters. The entered value corresponds to the unit mm .
If a switching point is not required, the value "0" must be set in the
appropriate parameter.