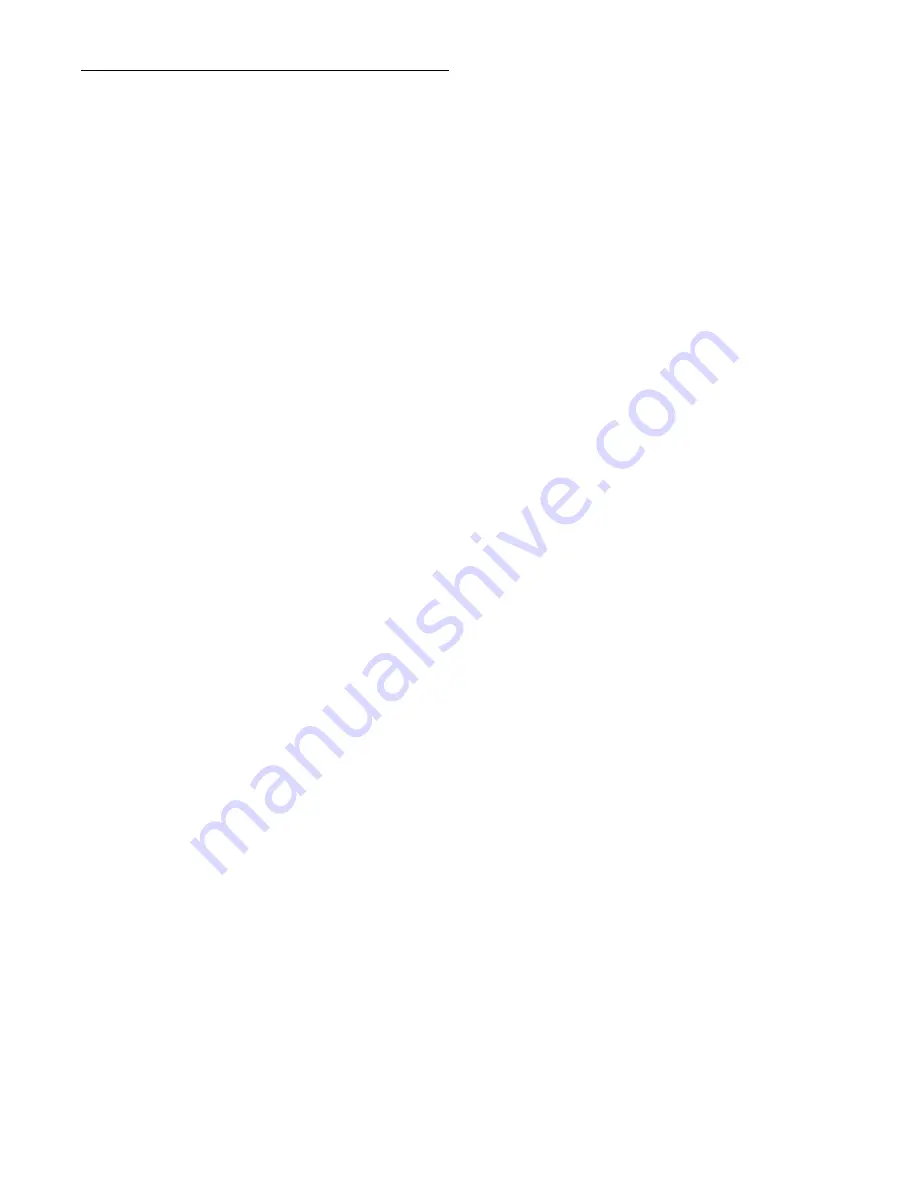
11
Application and precautions of Peripherals
Connection of single phase drives:
You may connect a single phase input drive to 3 phase
power by connecting terminal L1/L to phase A, L2/N to phase B and insulate phase C.
From the Power Source:
Apply the power source at the correct rated voltage to prevent from
damaging the inverter. Branch circuit protection (reference NEC article 610) must be installed
between the AC power supply and the inverter.
Molded-case circuit breaker and / or time delay fuses:
Utilize an appropriate circuit
breaker that's suitable for the rated voltage and current ratings of the inverter to switch ON/
OFF the power supply to the inverter and as additional protection for the inverter.
Leakage circuit breaker:
An earth leakage circuit breaker should be added to prevent false
operation caused by leakage current and to ensure personnel safety.
Magnetic contactor:
A magnetic contactor on line side of inverter can normally be omitted in
lieu of a crane mainline contactor. To utilize external DB braking resistors the magnetic
contactor or mainline must be installed on the primary side of the inverter with DB overload
wired in series. The magnetic contactor is only a fault isolation means. Do not use the mag-
netic contactor to switch power ON or OFF the inverter in a repititious fashion. Constant
power cycling to inverter may damage the inverter. If the inverter is installed in a retrofit where
existing reversing contactors are still maintained, insure the inverter is connected to a con-
stant source of power.
Load side contactors or conductors:
Any type of load side switch or load side sliding
conductors are strictly forbidden. The intermittent connection of the load will damage the
inverter.
Power feed conductors:
Always use a high quality conductor bar system with tandem shoe
collectors. Avoid brass wheel pickups or open span wire systems. Poor input power conduc-
tion will be sure to cause intermittent operation and possible damage to the inverter.
Brake contactor:
Select the proper contactor wired to primary of inverter to control motor
brake. Drivecon recommends the addition of a 3 phase AC suppressor across all brake
contactors.
Power improvement AC Reactor:
If large capacity source is applied (over 500KVA) addi-
tional AC reactor may be added to improve power factor and reduce likelihood of damage to
inverter.
Inverter:
Power supply input terminals L1, L2 and (L3) are not differentiated on phase se-
quence. They can be arbitrarily connected. Their connection may be interchanged.
Output terminal T1, T2, and T3 should be connected to T1, T2, and T3 terminals of motor
respectively. If motor turns in opposite direction of the inverter command, simply exchanging
two of the three wire connections will correct this problem.
Conductor length between drive and motor:
Excessive wire length between drive and
motor can cause premature insulation failure of motor. Substantial voltage spikes can be
measured at the motor terminals with as little as 30 feet of distance between the motor and
VFD. Drivecon recommends the use of our OLF filter or inverter duty motors with 1600V
magnet wire.
CAUTION:
•
Output terminal T1, T2, and T3 must not be connected to power source to prevent from
damaging the inverter.
Grounding terminal.
Properly ground the grounding terminal in compliance with NEC or local
codes. Under most circumstances and extra 4th conductor rail is not required but highly recom-
mended for personal safety. External wiring should be carried out in accordance with the follow-
ing requirement. Check and reassure the wiring is correct after the wiring is complete.
Содержание Crane Commander CCES102
Страница 16: ......
Страница 17: ......
Страница 20: ...18 Dimensions and installation of class B filter Models CCES215 CCES222 CCES407 CCES415 CCES422...