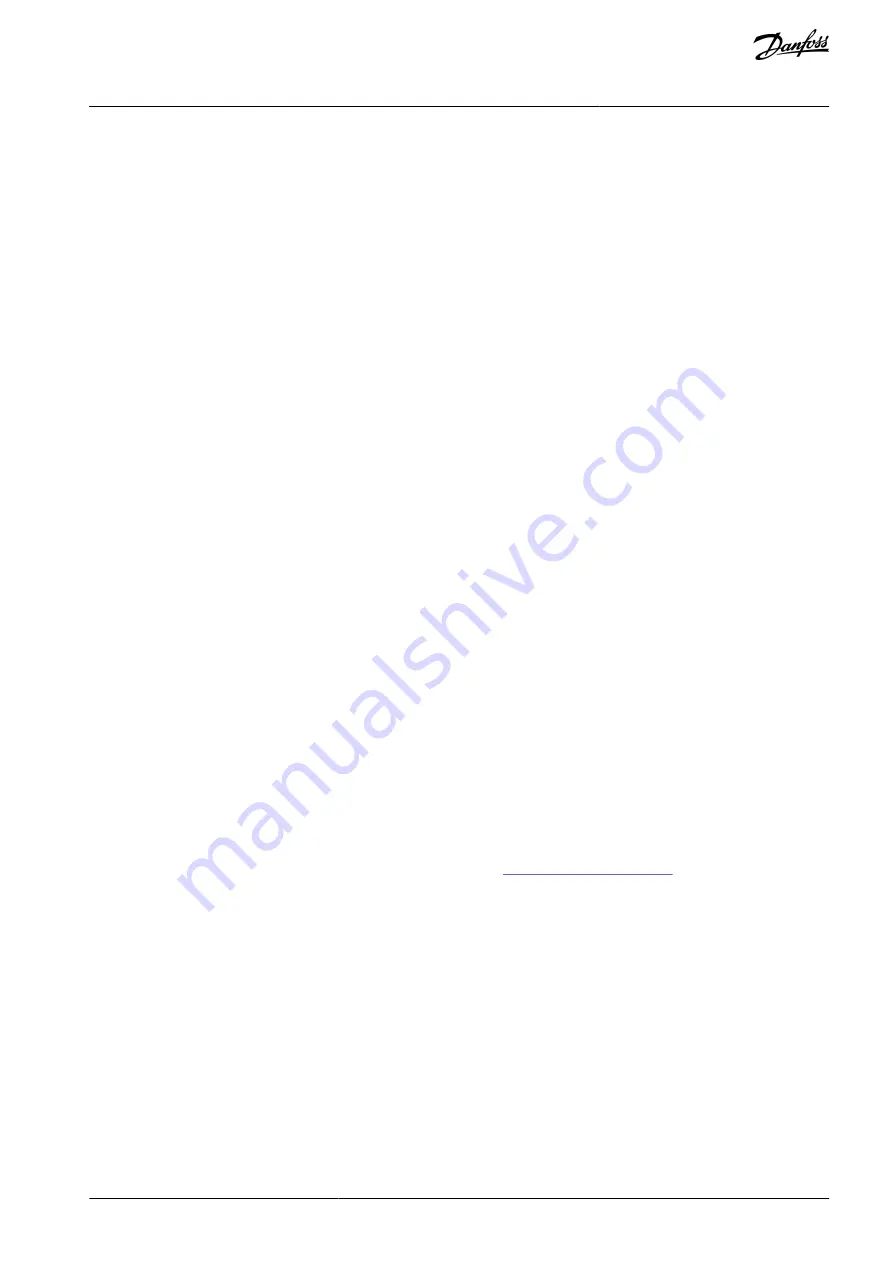
•
•
•
•
•
•
•
•
•
•
•
•
•
•
•
•
This option provides the SS1 (Safe Stop 1) function with the VLT
®
Safety Option MCB 151 along with STO function using an emer-
gency stop push-button on the control compartment door. The option is compatible with HTL encoders or PNP proximity switches.
The emergency stop-push button activates the motor deceleration and makes the motor stop in the set deceleration ramp time.
Basic wiring for the S37 terminal of the option card to terminal 37 of control card and the emergency push-button wiring are provi-
ded
MCB 151 is used when the standstill or the motor speed is measured using a TTL encoder. For detailed instructions, refer to the VLT
®
Safety Option MCB 150/151 Installation, Guide. MCB 151 can be programmed using VLT
®
Motion Control Tool MCT 10 software to
take advantage of the following functional safety features:
Safe Torque Off (STO).
No power is being fed to the motor which can generate a rotation. Stop category 0 to EN IEC 60204-1.
Safe Stop 1 (SS1).
The motor decelerates. Monitoring of deceleration ramp and STO following zero speed, or STO at the end of a deceleration
time. Stop category 1 to EN IEC 60204-1.
Safely limited speed (SLS).
This function prevents exceeding a defined speed value. See the OPT-B option board and safety relay user manuals for the regu-
lations and the certified safety.
5.8 Connecting Motor, Mains, and Ground Cables
5.8.1 Power Cabling and Grounding Considerations
Motor and mains connections
Size the wiring according to the input current of the drive. For maximum wire sizes, see the
Electrical Data
section.
Use cables rated for 75 °C (167 °F) of insulation for UL installations.
Comply with local and national electrical codes for cable sizes.
Follow motor manufacturer wiring requirements.
Motor wiring knockouts or access panels are provided on the pedestal of IP21/IP54 (NEMA 1/NEMA 12) units.
Do not wire a starting or pole-changing device (for example Dahlander motor or slip ring induction motor) between the drive
and the motor.
Ground connection
Ground the drive in accordance with applicable standards and directives.
Use a dedicated ground wire for input power, motor power, and control wiring.
Do not ground 1 drive to another in a daisy chain fashion.
Keep the ground wire connections as short as possible.
Follow motor manufacturer wiring requirements.
Minimum cable cross-section: 10 mm
2
(6 AWG) (or 2 rated ground wires terminated separately).
Tighten the terminals in accordance with the information provided in
EMC-compliant Installation
Refer to the
EMC-compliant Installation
section.
AQ262139143212en-000301 / 130R0879 | 99
Danfoss A/S © 2021.10
Electrical Installation
VLT® AutomationDrive FC 302
Operating Guide
Содержание D9h
Страница 2: ......
Страница 11: ...AQ262139143212en 000301 130R0879 11 Danfoss A S 2021 10 Introduction VLT AutomationDrive FC 302 Operating Guide...
Страница 12: ...AQ262139143212en 000301 130R0879 12 Danfoss A S 2021 10 Introduction VLT AutomationDrive FC 302 Operating Guide...
Страница 13: ...AQ262139143212en 000301 130R0879 13 Danfoss A S 2021 10 Introduction VLT AutomationDrive FC 302 Operating Guide...