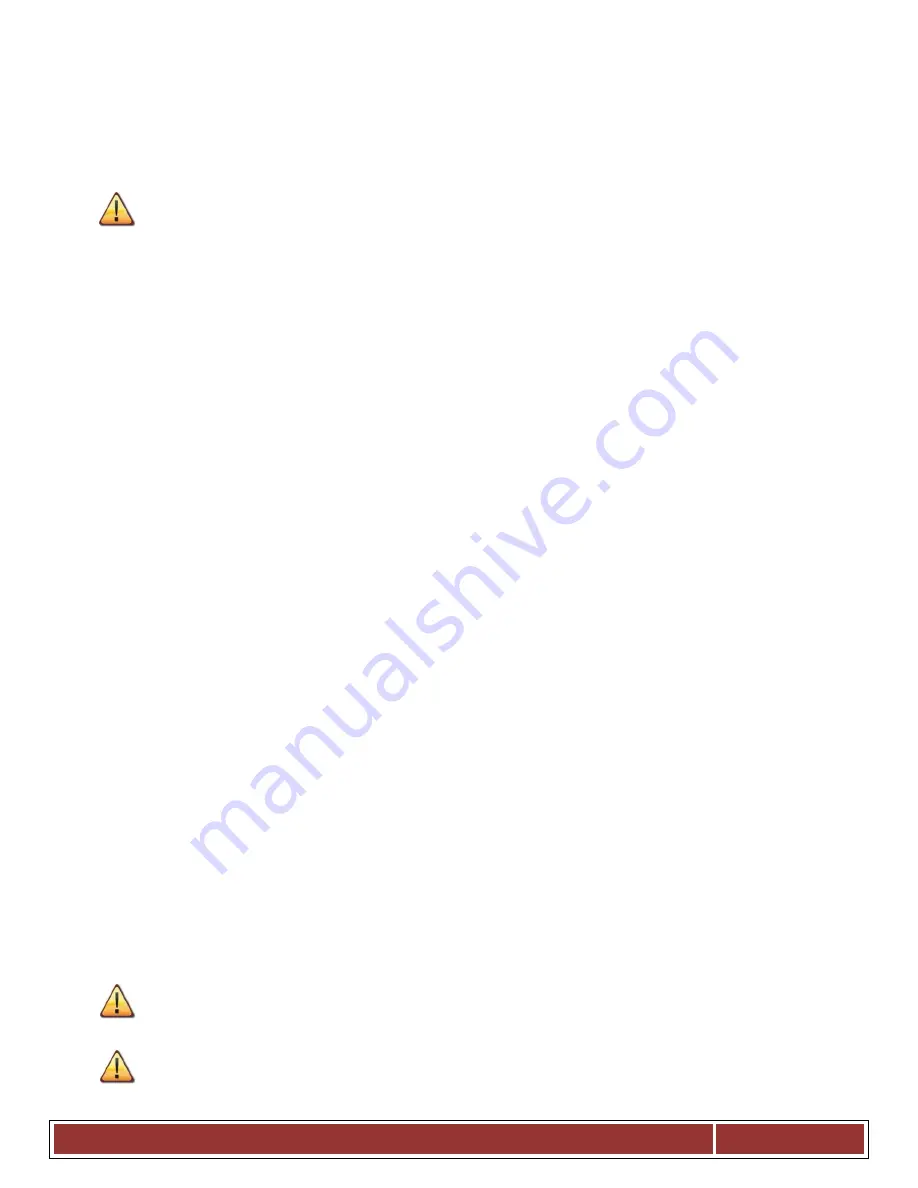
LIMIT and HOMING switches
On both – slave and master axes side – there should be
separate LIMIT and HOME switches
. The
signals should be properly set in Mach3 program („Config
Ports and Pins”).
Before next steps it is necessary to verify if the signals are correctly configured (DIAGNOSTICS tab)
Pay special attention whether HOMING switches are not replaced. Pressing by hand the HOME
switch on „X” motor side the M1HOME should light up, presing HOME switch on „B” motor side - the
M5HOME should light up.
Axis direction settings
One of the most important issues is correct setting of movement directions for master and slave ax-
es. In our example, drive is transmitted by toothed bars. In this case, usually there is need to change
slave axis direction. We can do it in „Config
Homing/Limits” by setting „Reversed” at „B” axis. The
direction can be also changed in servo drive.
Manual feed test
When all the steps described above are already done, you can attempt to test the axis working in the
manual feed. A small note: At the beginning, the best is to set very low speed - even 0.5%. You
should first verify whether the motors are working on both sides and whether the feed goes in good
directions.
Automatic reading of HOME switches position difference
Before we activate the mode slave axis with geometry correction, you should know what is position
difference of HOME switches on master (“X”) and slave (“B”) side. Homing with geometry correction
is about that master axis always finishes homing at the moment it goes back off its HOME switch, and
slave axis goes to: [HOME switch back off position - correction]. If we gave zero correction initially
and HOME switches position on both sides differs by e.g. 10 mm - then there would be issues with
gantry during homing.
To avoid this situation there is additional mode created - for HOME switches position difference
measurement.
In plugin configuration window for “X” axis in “Slave Axis Configuration” group enable the „Read
Difference” mode and start homing. After homing is finished, open the plugin configuration window
again and in „Geometry correction” area there should be the value from the measurement.
Geometry correction mode activation
After correct measurement
of
HOME switches position difference, in the configuration window you
can activate „Sl. correction” mode for „X” axis. Since now on, we can adjust the perpendicularity by
modifying "Geometry correction" value. For perpendicularity measurement, we recommend
Renishaw® Ballbar system.
You should not use stepper motors for slave axis. Lack of position feedback causes a risk of mechan-
ics of machine damage. With servo-drives, you should always have alarm signals configured correctly.
CS-Lab Company made every effort to ensure reliability of CSMIO/IP-S controller. However, our
company does not take any responsibility for any mechanics damage because of wrong configuration
and any eventual failure or software errors of CSMIO/IP-S controller.
C S - L a b s . c . – C S M I O / I P - S - C N C C o n t r o l l e r
Page 93