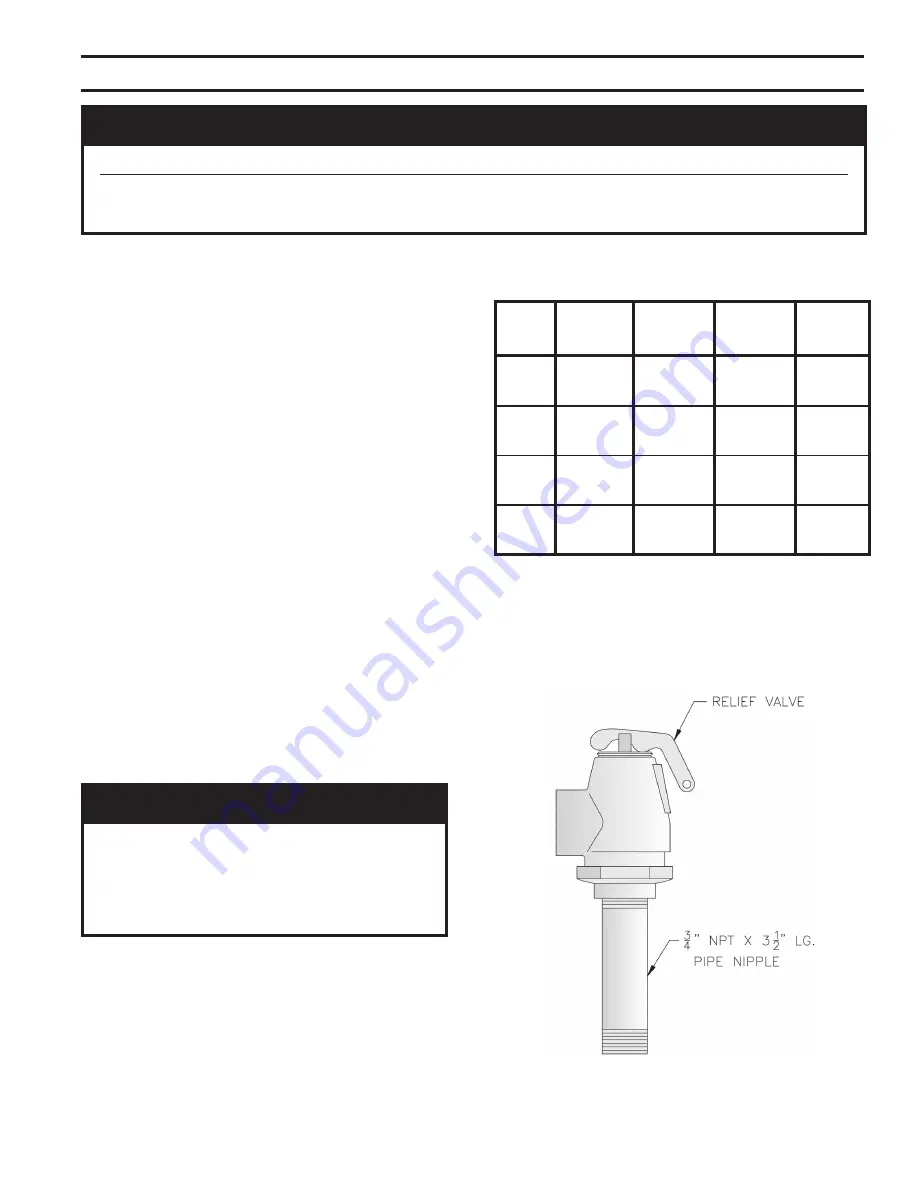
19
IV. Water Trim and Piping
A
.
Design and install boiler and system piping
to
prevent oxygen contamination of boiler water and
frequent water additions.
1. There are many possible causes of oxygen
contamination such as:
a. Addition of excessive make-up water as a result
of system leaks.
b. Absorption through open tanks and fittings.
c. Oxygen permeable materials in the distribution
system.
2. In order to insure long product life, oxygen sources
must be eliminated. This can be accomplished by
taking the following measures:
a. Repairing system leaks to eliminate the need for
addition of make-up water.
b. Eliminating open tanks from the system.
c. Eliminating and/or repairing fittings which allow
oxygen absorption.
d. Use of non-permeable materials in the
distribution system.
e. Isolating the boiler from the system water by
installing a heat exchanger.
f. Use properly designed and operating air
elimination devices in water piping.
B.
Design boiler piping and flow rate
to obtain proper
temperature rise though the boiler. (See Table 4)
WARNING
Pressure relief valve discharge piping must be
piped such that the potential of severe burns
is eliminated. DO NOT pipe in any area where
freezing could occur. DO NOT install any shut off
valves, plugs or caps. Consult Local Codes for
proper discharge piping arrangement.
C.
Install Safety Relief Valve.
See Figure 16.
Components are located in Water Trim Carton. Safety
Relief Valve must be installed with spindle in vertical
position.
1. Install ¾” NPT x 3½” lg. nipple in tapping “C”. See
Figure 3.
2. Install safety relief valve on ¾” NPT nipple.
WARNING
Failure to properly pipe boiler may result in improper operation and damage to boiler or structure.
Oxygen contamination of boiler water will cause corrosion of iron and steel boiler components, and can
lead to boiler failure. Crown’s Warranty does not cover problems caused by oxygen contamination of
boiler water or scale (lime) build-up caused by frequent addition of water.
Table 4: Flow Rate, Temperature Rise, and
Pressure Drop
Boiler
Model
Flow Rate
(GPM)
Temp. Rise
Thru Boiler
Min. Boiler
Piping NPT
Boiler
Pressure
Drop
16H-340
28
19
14
20° F
30° F
40° F
2”
1½”
1¼”
3’
2’
1’
16H-410
34
22
17
20° F
30° F
40° F
2”
1½”
1½”
3’
2’
1’
16H-460
38
25
19
20° F
30° F
40° F
2”
2”
1½”
3’
2’
1’
16H-505
42
28
21
20° F
30° F
40° F
2”
2”
1½”
3’
2’
1’
Figure 16: Safety Relief Valve Installation
Содержание 16H-340
Страница 11: ...11 Figure 6 Flame Roll out Switch Installation Figure 7 Burner Burner Access Panel Installation ...
Страница 13: ...13 Figure 8 Jacket Assembly ...
Страница 14: ...14 Figure 9 EP CSD 1 Control Installation ...
Страница 16: ...16 Figure 11 Main Gas Piping Intermittent Ignition EI ...
Страница 17: ...17 Figure 12 Schematic Pilot Piping Honeywell EI USA ...
Страница 18: ...18 Figure 15 Schematic Gas Piping EP CSD 1 Control System 16H 410 16H 505 ...
Страница 31: ...31 Figure 31 Wiring Diagram Honeywell EI USA Intermittent Circulation 16H 340 16H 510 MegaStor Relay MegaStor ...
Страница 37: ...37 Figure 41 Operating Instructions EI ...
Страница 47: ...47 Honeywell EI Trouble Shooting Guide ...
Страница 48: ...48 THIS PAGE LEFT BLANK INTENTIONALLY ...
Страница 58: ...58 ...
Страница 60: ...60 ...