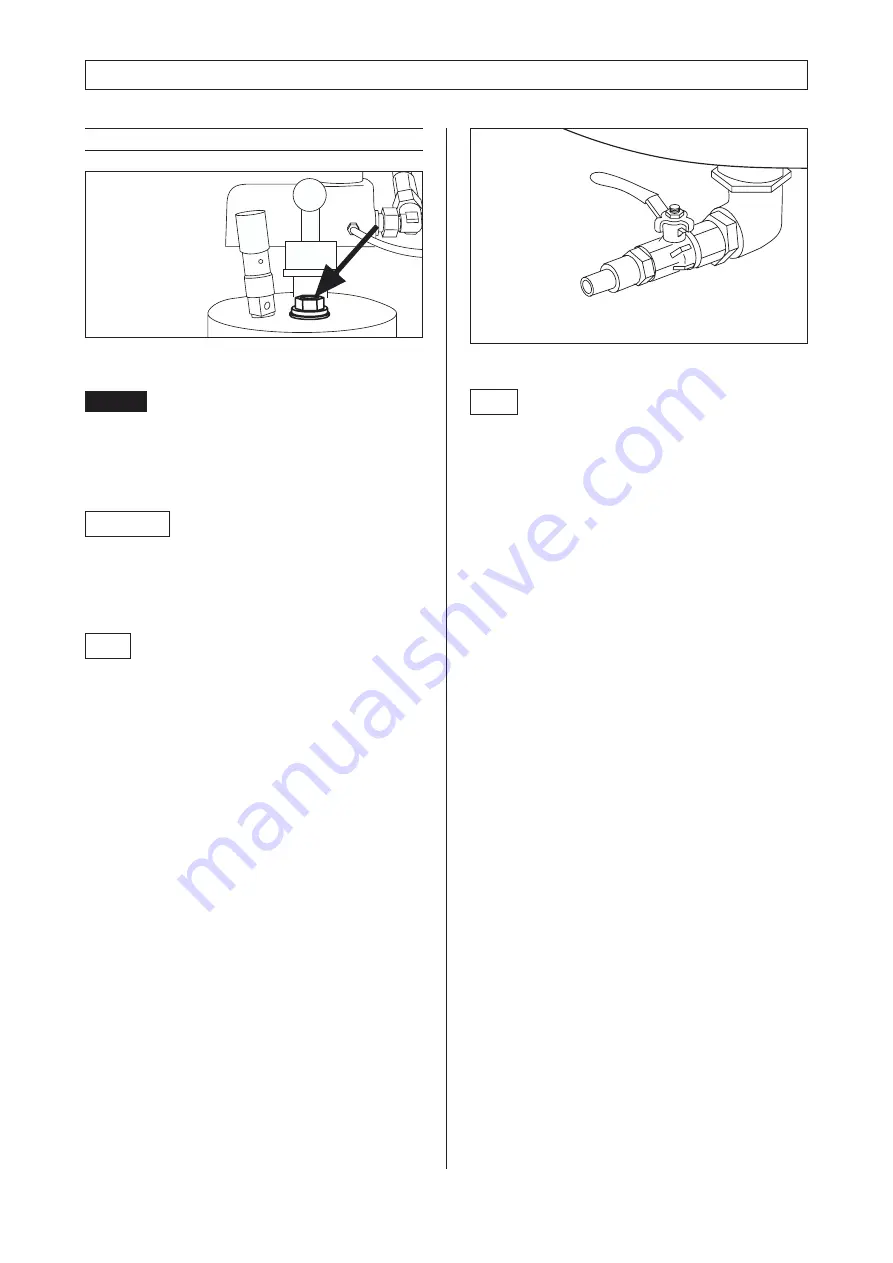
33
8. Servicing and maintenance
8.4
Oil change
Changing intervals for lubricants
The operating conditions (e.g. coolant temperatures),
the operating modes and the quality of the intake air
(e.g. content of dust, content of gaseous foreign matter
such as SO
2
, solvent vapours, etc.) have a strong in-
fluence on the oil change intervals. We therefore re-
commend to have your mineral oil supplier work out oil
analyses in the starting time. For critical applications,
the permissible time of use of the oil must be verified
with the help of an oil analysis.
For the oil change intervals, see the maintenance
schedule.
When changing the oil, proceed as follows :
• Carefully open the oil drain (fig. 19) of the pressure
reservoir and the oil cooler, utilize the residual pres-
sure in the unit for draining.
• Open the oil drain (fig. 20) of the pressure reservoir
and the oil cooler
• Drain the oil at operating temperature
• Close the oil drain (fig. 20) of the pressure reservoir
and the oil cooler
• Fill in oil (approx. 40 L)
• Close the oil filling hole with the plug screw
• Let the screw compressor unit run for approx. 2 mi-
nutes
• Check for leakages
• Switch the screw compressor unit off
• Check oil level :
For this, the oil should have settled, i.e. the entrap-
ped air should have been dispersed
• The oil level must be in the center of the oil sight-
glass
• If required, top up oil.
Note
When changing the oil, the waste oil is to be drained
completely, if possible, since used oil reduces the ser-
vice life of the new oil fill considerably.
Lubricants of different types should not be mixed.
When changing over to a new oil type, the oil in the oil
circuit must be drained completely.
Fig. 21
Danger
.
The oil must only be changed, when the screw
compressor is out of operation and depressurized !
Be careful when draining hot oil : Danger of scal-
ding !
Note
Collect the waste oil, let not seep away into the soil !
Disposal in accordance with the regulations ! Do not
spill oil ! Check for leakage !
With these compressors, the oil change intervals
strongly depend on the degree of contamination of the
circulating oil. It must therefore be taken care that no
oil-deteriorating matter (dusts, vapours, gases) are
transported through the air intake filter into the oil circuit
of the compressor unit. Also a high content of humidity
in the intake air and the formation of condensate within
the machine affect the service life of the lubricant oil so
that a reduction in the oil change intervals may become
necessary. The specified oil change intervals refer to
an intake air from a normal environment without a high
content of foreign matter (dusts, vapours, gases). If, un-
der favourable conditions, it is intended that the oil ser-
vice life be extended, oil samples have to be examined,
and the extension of the operating time is to be deter-
mined on the basis of these analysis results.
Important
Remove oil residues and other deposits from unit
parts and from the coolers of compressors, which
are exposed to hot compressed air, according to
the operating instructions.
Fig. 20