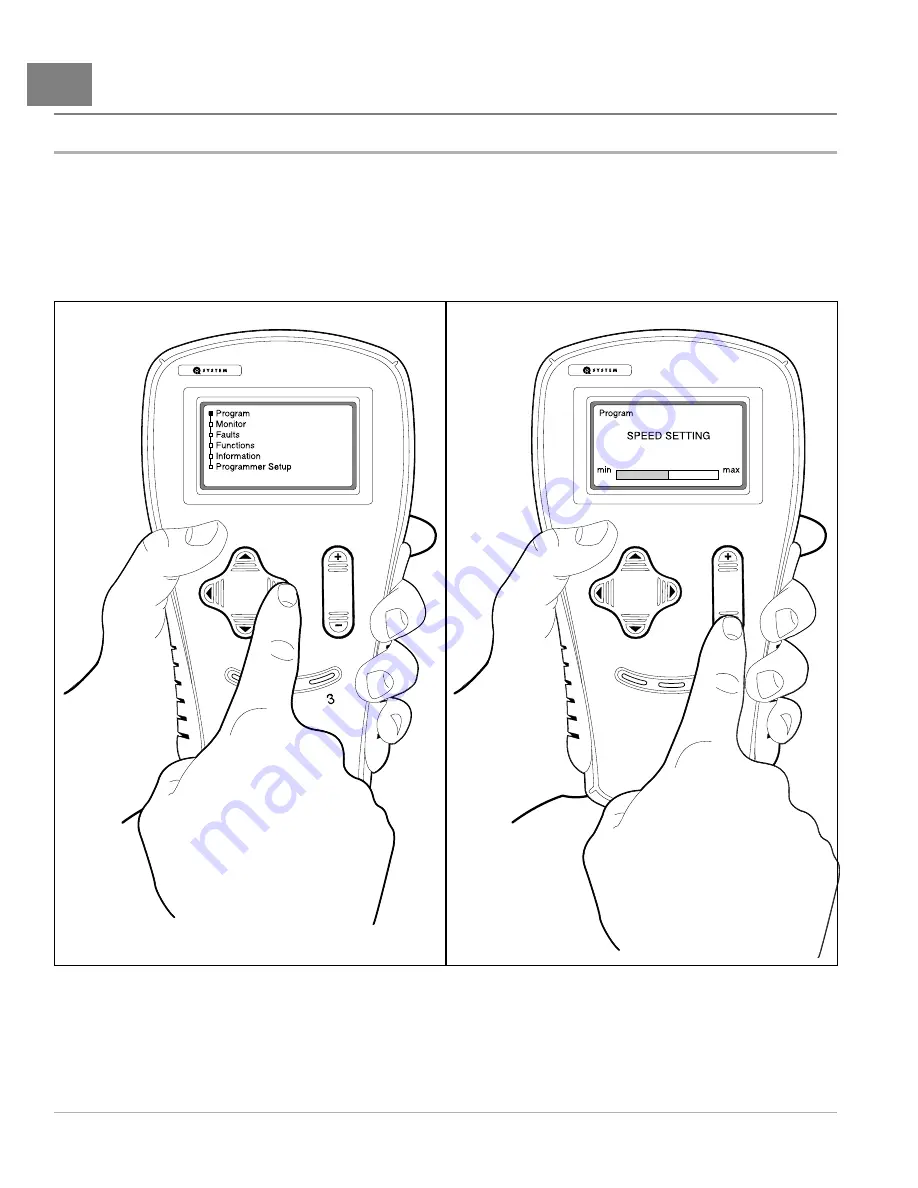
21
Program Menu
IQ DISPLAY MODULE PROGRAMMER
(IQDM-P): EXCEL SYSTEM
PROGRAM MENU
The
program
menu can be accessed by pressing the right arrow on the navigation button when the square beside
program
is blinking
(Figure 21-3, Page 21-2)
. When the
program
menu is active, use the up or down arrows on the
navigation button to go to the desired item in the
program
menu. Again, press the right arrow to select the menu item.
Use the change value button to change the values of the selected item as necessary.
The following parameters can be programmed with the handset from the
program
menu:
1
2
3
2
1
3
775
Figure 21-3
Access Program Menu
776
Figure 21-4
Change Speed Setting
Page 21-2
2009 Electric Precedent Maintenance and Service Manual
Содержание 2009 Precedent
Страница 2: ......
Страница 4: ......
Страница 16: ......
Страница 22: ......
Страница 48: ......
Страница 64: ......
Страница 136: ......
Страница 174: ......
Страница 196: ......
Страница 218: ......
Страница 262: ......
Страница 264: ......
Страница 306: ......
Страница 307: ......
Страница 308: ......
Страница 310: ......
Страница 311: ......
Страница 312: ......