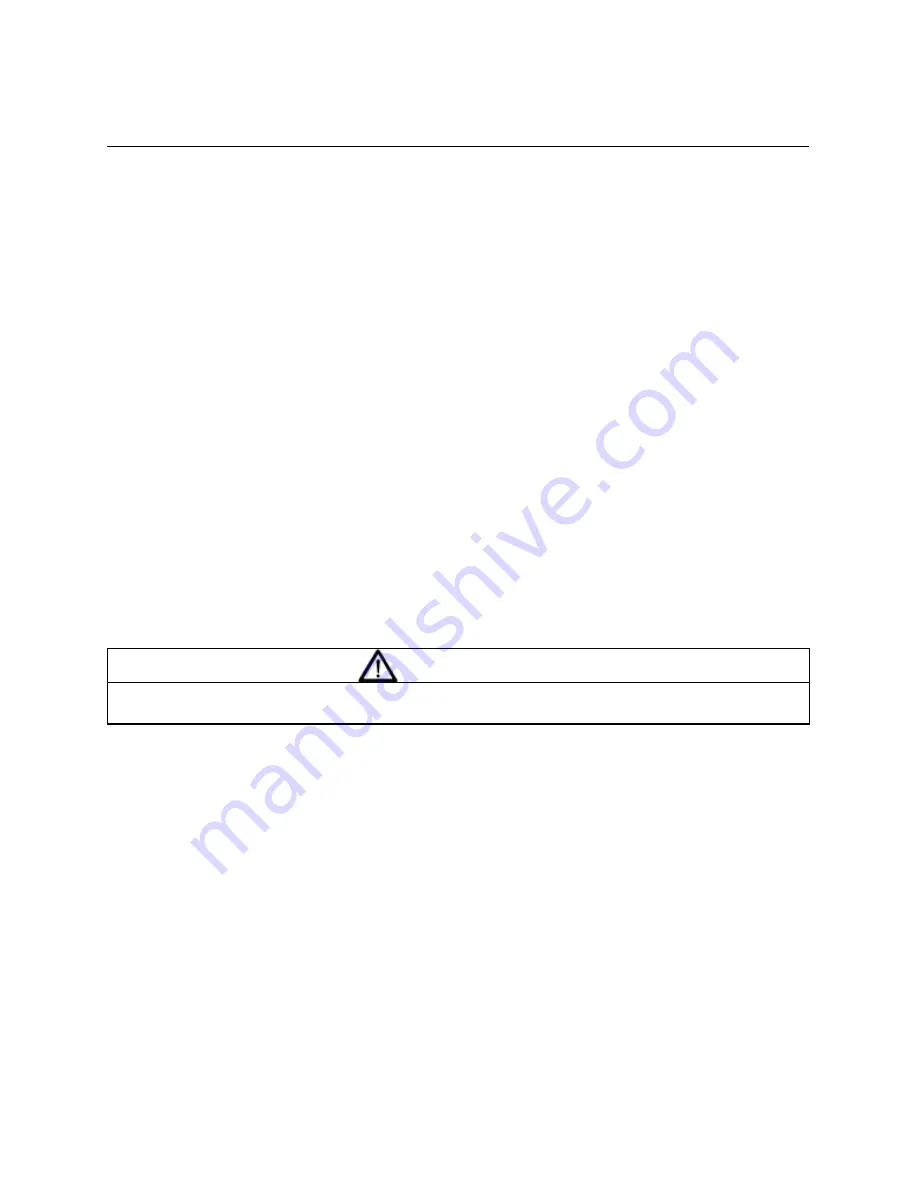
13-11-614 Page 24
SECTION 4
CONTROLS & INSTRUMENTATION
GENERAL DESCRIPTION
- The Champion RotorChamp water-flooded rotary screw compressor is
prewired with all controls, motor, and starter for the voltage and horsepower at the time of ordering. It is
necessary only to connect the compressor unit to the correct power supply, to the shop air line, and to the
appropriate water supply. A standard compressor unit consists of the compressor, water reservoir, water
cooling system and filters, lubrication reservoir, motor type as specified, NEMA 12 starter/control box, and
control components as described below.
This compressor unit features the AUTO SENTRY W controller, which integrates all the control functions
under microprocessor control. Its functions include safety and shutdown, compressor regulation, operator
control, and advisory/maintenance indicators. The keypad and display provide the operator with a logical
and easily operated control of the compressor and indication of its condition.
AUTO SENTRY W OPERATION
Normal operation is controlled by the keys in the OPERATE island of the AUTO SENTRY W controller.
Prior to starting, press the [STOP/RESET] key to place the controller into its READY state (as indicated
on the display). Press the [RUN] key to start the compressor. The green LED will light near the
automatic operation symbol whenever operation is enabled.
The [STOP/RESET] key may be pressed at any time to stop the compressor under normal conditions. If
the compressor has been running, the reservoir pressure is relieved before stopping the motor. The
display will count down to zero during the normal stop.
An optional control may be wired into the AUTO SENTRY W controller to interrupt and restart the unit
based on controls by others. When stopped by these controls, the display indicates remote stop.
WARNING
Automatic restarting or electrical shock can cause injury or death. Open, tag
and lockout main disconnect and any other circuits before servicing the unit.
In any mode, the compressor will start only if reservoir pressure is below 5 psig (0.3 bars). The display
will indicate if the control is waiting for a reservoir blowdown, along with the remaining pressure. The
controls also delay initial loading of the compressor until a startup delay has been completed.
All modes of operating provided by the AUTO SENTRY W controller produce load/unload flow control.
An independent pneumatic pilot valve is also supplied to provide flow modulation and thus match
package air supply to the system demand. If simple load/unload operation is desired, the pneumatic pilot
valve can be deactivated by setting its opening pressure beyond the unload pressure setting programmed
in the controller. See “Subtractive Valve”, page 39, under “Other Control Devices” for details.
Constant Run Mode Operation
- This mode is best used in applications where there are no long
periods of unloaded operation. The compressor unit will start and run continuously, using its controls to
load and unload the compressor. This matches average delivery to demand. When the air demand is
less than the compressor capacity, the air pressure rises to the unload point of the controller, which will
then unload, blow down, and stop delivery of air to the system. Air demands are supplied by air stored in
receivers and plant piping. When the pressure falls halfway between the unload and load pressures, the
W controller again fully loads the compressor.
When first starting, the controller will keep the compressor fully unloaded and blown down until the
system pressure drops below the load pressure.
Содержание ROTORCHAMP EWF99C-100
Страница 7: ...13 11 614 Page 7 Figure 1 2 PACKAGE ILLUSTRATION AIR COOLED 309EWF797 A Ref Drawing ...
Страница 8: ...13 11 614 Page 8 Figure 1 3 PACKAGE ILLUSTRATION WATER COOLED 310EWF797 A Ref Drawing ...
Страница 9: ...13 11 614 Page 9 Figure 1 4 AIR COOLED SCHEMATIC 307EWF797 A Ref Drawing ...
Страница 10: ...13 11 614 Page 10 Figure 1 5 WATER COOLED SCHEMATIC 308EWF797 A Ref Drawing ...
Страница 29: ...13 11 614 Page 29 Figure 4 2 FLOW CHART FOR SETUP PROGRAMMING 300EWC1255 Ref Drawing ...
Страница 43: ...13 11 614 Page 43 303EWF546 A Ref Drawing Page 2 of 2 ...
Страница 44: ...13 11 614 Page 44 Figure 4 5 WIRING DIAGRAM WYE DELTA WITH EXPANSION BOARD 304EWF546 A Ref Drawing Page 1 of 2 ...
Страница 45: ...13 11 614 Page 45 304EWF546 A Ref Drawing Page 2 of 2 ...
Страница 46: ...13 11 614 Page 46 Figure 4 6 WIRING DIAGRAM FULL VOLTAGE LESS STARTER 305EWF546 A Ref Drawing Page 1 of 2 ...
Страница 47: ...13 11 614 Page 47 305EWF546 A Ref Drawing Page 2 of 2 ...