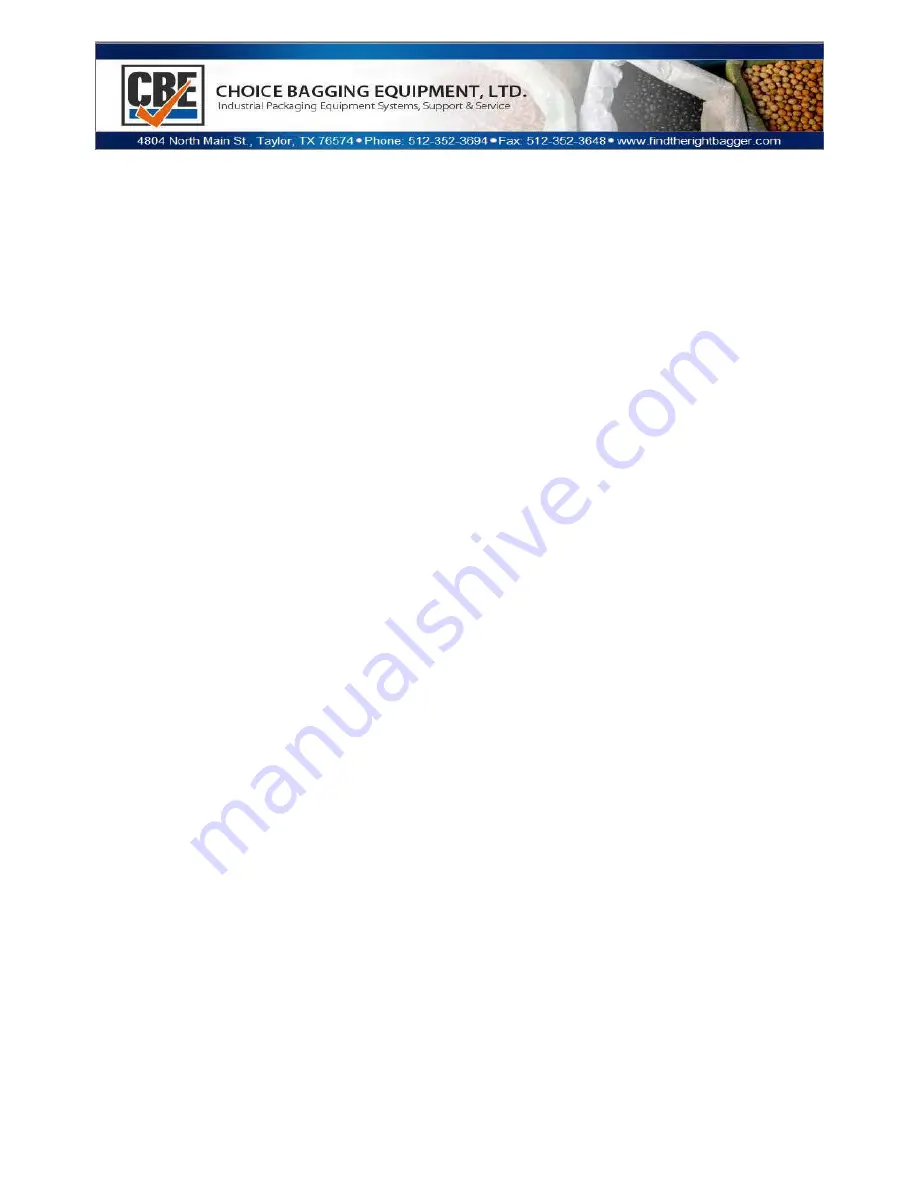
2
Table of Contents Page
Quick Reference Installation Information
4
Warnings and Notices
5
Grounding Recommendations and Noise
6
Recommended Spare Parts
9
Chapter 1
– General Information
10
Receipt and Inspection
11
Caution and Warnings
11
Specific Requirements
12
Dust Collection
13
Chapter 2
– Installation Guide
14
Introduction
15
Preparation
15
Site Selection
15
Uncrating
15
Re-Adjusting the Load Cell Feet
15
Load Cell Feet Checks
16
Connecting to the Supply Bin
16
Setting Conveyors
17
Installation Summary
17
Chapter 3
– Load Cell Wiring
18
Load Cell Wiring to Junction Box
19
Calibration Instructions
20
Load Cell Replacement
20
Chapter 4
– Component Description
23
CBE 520 Bulk Bag Filler Assemblies
24
Densifying Deck
26
Chapter 5
– Operational Sequence
27
Operational Sequence
28
Auto Strap Release (Optional)
29
Bag Seal Cuff (Optional)
30
Pre-Bag Inflate (Optional)
31
Powered Roller Discharge (Optional)
32
Chapter 6
– Conveyor Setup
33
Chapter 7
– PLC Timers and Adjustments
38
CBE Data Touch
40
Avery 405
40
Chapter 8
– Weigh Controller and Adjustments
43
Controllers
44
Avery 405 - Setting Target Weight
45
Содержание 520
Страница 1: ...1 CBE 520 BULK BAGGER Safety Installation Operation Maintenance ...
Страница 10: ...10 CHAPTER 1 General Information ...
Страница 14: ...14 CHAPTER 2 INSTALLATION GUIDE ...
Страница 18: ...18 CHAPTER 3 LOAD CELL WIRING ...
Страница 22: ...22 Figure 3 500 Series Bottom View ...
Страница 23: ...23 CHAPTER 4 COMPONENT DESCRIPTION ...
Страница 26: ...26 CBE DENSIFYING DECK ...
Страница 27: ...27 CHAPTER 5 OPERATIONAL SEQUENCE ...
Страница 33: ...33 CHAPTER 6 Conveyors Setup ...
Страница 38: ...38 CHAPTER 7 PLC and Timers and Adjustments ...
Страница 43: ...43 CHAPTER 8 WEIGH CONTROLLER And ADJUSTMENTS ...
Страница 45: ...45 ...
Страница 48: ...48 See attached Documentation For the Controller specifically Used on your machine ...
Страница 49: ...49 Chapter 9 MAINTENANCE ...
Страница 51: ...51 CHAPTER 10 TROUBLESHOOTING ...
Страница 55: ...55 ...
Страница 56: ...56 CHAPTER 11 STANDARD ILUSTRATED PARTS See attached documentation for Other parts Specific to Your Bagger ...
Страница 57: ...57 CHAPTER 12 PLC and TIMER ADJUSTMENTS ...
Страница 61: ...61 DRAWINGS AND SCHEMATICS See attached Schematics And Drawings specific for your machine ...