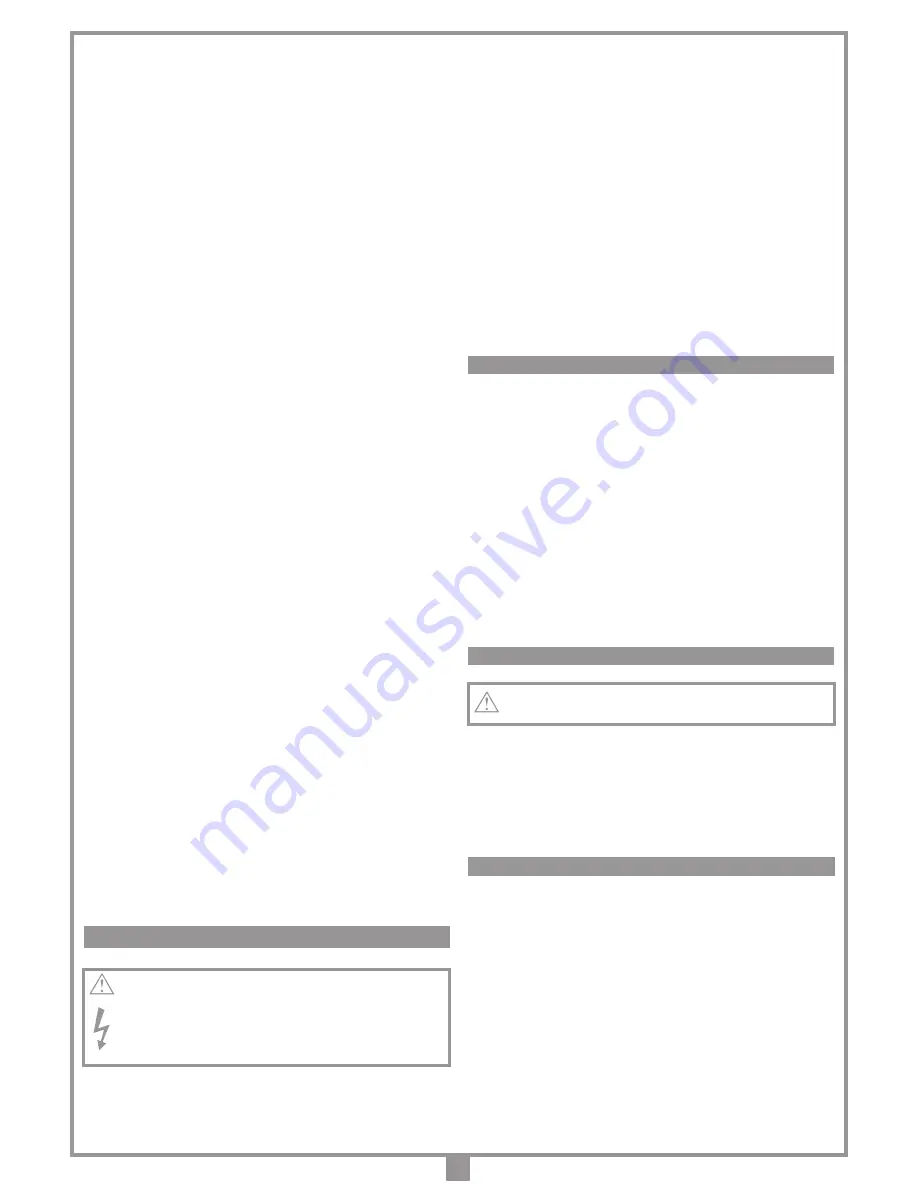
12
• The cables must be fastened down near the terminal board so
that both the power wires and the sheath are well blocked by the
supplied cable clamp.
• The electrical wires may be run to the appliance in two ways:
- through the wall entrance "
O" (fig.9)
- externally, using a cable pipe, after having remove the plastic
disk blocking the entrance hole.
Connect the motors following the wiring diagram on page 8.
Left-hand installed motor:
- binding post "
1" opening direction;
- binding post "
2" closing direction;
- binding post "
N" common.
Right-hand installed motor:
- binding post "
1" closing direction;
- binding post "
2" opening direction;
- binding post "
N" common
Releasing the gate should only be carried out when the motor has
stopped because of blackouts.
Releasing the gate
Open the access door and rotate the lever anticlockwise as shown in
detail "
A" (fig.12) until it reaches the release position "B" where it will
remain thanks to an anti return mechanism. This will release the geared
motor and free the gate, which can then be opened by pushing lightly
on the gate.
Locking the gate
Lightly press the lever from the released position pos."
B" to overcome
the anti-return mechanism. The presence of the spring will make the
mechanism automatically return to the blocked position "
A". The reduc-
tion motor gears may not lock immediately but they can be locked
manually by pressing on the gate or by reactivating the motor.
Before carrying out any cleaning or maintenance operations
make sure the power is disconnected at the mains.
Replacing travel limits (fig. 10, pag. 6)
- The opening/closing travel limits are connected in series to one
of the motor live wires: when the contact is open the power to the
motor is cut off.
- Positioning the lower and upper cams must be carried out exactly
as shown in the drawing in details "
A1" and "B1".
During the opening/closing manoeuvre check for correct operation
and activate the emergency stop button in case of danger.
During blackouts the gate can be released and manually manoeuvred
using the supplied release key (see manual release).
Periodically check the moving parts for wear and tear and grease if
required, using lubricants which maintain their friction levels unal-
tered throughout time and are suitable for temperatures of
-20 to
+70°C.
In case of failure or operational anomalies switch off the power at
the mains do not attempt to repair the appliance yourself.
Periodically check the correct operation of all safety devices (pho-
toelectric cells etc.). Eventual repair work must be carried out by
specialised personnel using original spare parts.
FITTING THE UNIT
The unit may be positioned either to the right or to the left of the
passageway.
• Move the gate/s to the closed position.
• Choose the value "
A" (fig. 4) according to the required opening
angle and work out (depending on the structural characteristics of
the gate) at what height the front bracket will be fitted to the gate.
Once the position has been established, fasten down the motor
support plate using four M8 screws and steel Ø14 rawlplugs. Make
sure that the support bracket "
D" (fig. 7) is perfectly level.
• Insert the operator arm "
E" onto the motor drive shaft as indicated
in fig.8 and tighten down using the supplied grub screw "
F".
• According to the assembly drawings (motor installed to the right
fig.9) and (motor installed to the left fig.10) fix the geared motor
to the base plate using the two screws and self-locking nuts "
G".
The geared motor is factory set to be installed to the right of the
gate as seen from the inside. To install the motor to the left first
remove the plastic disk "
H" (fig.10) which blocks the hole required
for the motor drive shaft, using a pair of pliers and then cover the
other hole using the supplied mobile disk "
L".
• Fit the articulated operator arm and bracket to the gate (fig.2)
- insert the plastic guides "
11" into the holes on the curved arm
"
7", connect the curved arm "7" to the straight arm "6" and to the
bracket "
8" using the screws "9" and self-locking nuts "12" after
having inserted the zinc-plated washer "
10" inside the plastic guide
"
11".
• Release the motor (fig. 12).
• Fasten the front bracket to the gate using two
M8 screws 39 mm
below the base (det. 1 fig.6). The position of the front bracket is
determined by opening the arm to its maximum extension (with
the gate fully closed) and aligning the points 1,2 and 3 (fig.4). Next,
move point 2 backwards by
100 mm from the point of alignment.
The arm must be in square "
M" (fig.6).
Check the following:
- with the front bracket leaning against the gate check that it
does not suffer forcing along the "
L" axis (fig.6) either upwards or
downwards while the gate is moving. Should this occur either the
gate or the geared motor has been incorrectly installed and this
could damage the appliance.
Once you have checked all the alignments fasten down the front
bracket to the gate.
• Adjust the opening direction travel end micro switch (upper cam
"
A" fig. 1-2) and the closing end micro switch (lower cam "B" fig.
1-2): move the gate to the desired open/closed position, rotate
the cam manually until the switch trips and then fasten down.
• After finishing the installation of the appliance and carrying out the
electrical connection fit the carter (fig.11) using the self-tapping
screws "
N" and making sure that the two lower teeth on the plastic
base lock the cover.
• You are advised to fit an electric locking device on the installation
(see standard installation fig.1).
Before connecting the appliance make sure that the voltage
and frequency rated on the data plate conform to those of
the mains supply.
An all pole trip switch with a least
3 mm between the contacts
must be installed between the unit and the mains supply.
• The appliance works off a
230Vac power supply.
• Do not use cables with aluminium conductors; do not solder the
ends of cables which are to be inserted into the binding posts.
ELECTRICAL CONNECTION (fig. 14)
MANUAL RELEASE MECHANISM (fig.12)
MAINTENANCE
USER INSTRUCTIONS