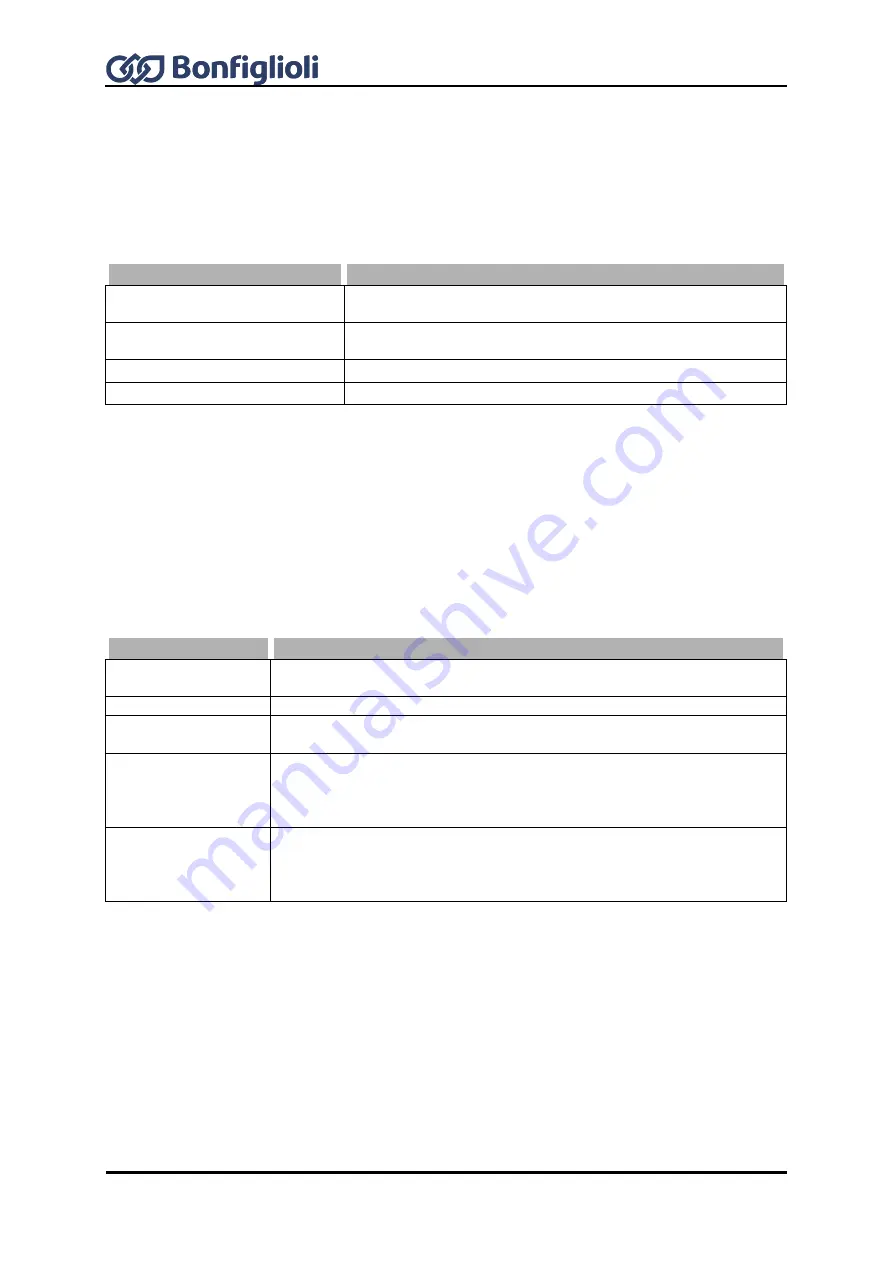
226
Operating Instructions ACU
12/16
18.5.3.3
Limit value sources
The limitation of the frequency can be done by setting fixed values and by linking to an analog input
parameter. The analog value is limited via parameters
Minimum Reference Percentage
518
and
Maximum Reference Percentage
519
, but does not consider the
Gradient Percentage Ramp
477
of
the reference percentage value channel.
The assignment is done for the torque controller via parameters
Frequency Upper Limit Source
769
and
Frequency Lower Limit Source
770
.
Operation mode 769, 770
Function
101 - Analog Input MFI1A
Multifunction input 1 in analog Operation Mode
452
is the
source.
110 - Fixed Limit
The selected parameter values are taken into account to limit
the speed controller.
201 - Inv. Analog Input MFI1A
Operation mode 101, inverted.
210 - Inv. Fixed Limit
Operation mode 110, inverted.
18.5.3.4
Switching over between speed control and torque control
With the signal assigned to parameter
n-/M-Control Change-Over
164
, you can switch between
speed control and torque control. See Chapter 16.4.6 "16.4.6".
18.5.4
Speed controller
The actual speed source is selected via parameter
Actual Speed Source
766
. In the default setting,
Speed Sensor 1 is used as the source of actual speed. If Speed Sensor 2 of an extension module is
to deliver the actual value signal for the speed controller, Speed Sensor 2 must be selected as the
source. Alternatively, the speed controller can derive the actual speed value from the machine model
in in Configurations 410, 411 and 430 (
Parameter Configuration
30
).
Operation Mode 766
Function
1 - Speed Sensor 1
The actual speed source is speed sensor 1 of the basic device (factory
setting).
2 - Speed Sensor 2
The actual speed source is speed sensor 2 of an extension module.
1)
3 - Machine Model
The speed controller receives the calculated actual speed value from the
machine model. Can be set in configurations 4xx and 6xx.
4 - Speedtracking EC
1
Speedtracking by comparison between the calculated machine model and
speed sensor 1 to increase speed accuracy. Can be set in configurations 4xx
and 6xx. The setting for parameter
Integral Time Speedtracking
515
is
considered.
5 - Speedtracking EC
2
Speed compensation by comparison between the calculated machine model
and speed sensor 2 of an extension module
1)
to increase speed accuracy.
Can be set in configurations 4xx and 6xx. The setting for parameter
Integral Time Speedtracking
515
is considered.
1)
Only available if extension module is installed
The control of the torque-forming current components is done in the outer control loop by the speed
controller. Via parameter
Operation Mode
720
, you can select the operation mode for the speed
controller. The operation mode defines the use of the parameterizable limits. These are referred to
the direction of rotation and the direction of the torque and depend on the selected configuration.
Содержание active cube 201
Страница 1: ...ACTIVE CUBE Operating Instructions Frequency inverter 230 V 400 V 0 25 kW 132 kW...
Страница 2: ......
Страница 45: ...12 16 Operating Instructions ACU 45...
Страница 181: ...12 16 Operating Instructions ACU 181...
Страница 284: ......