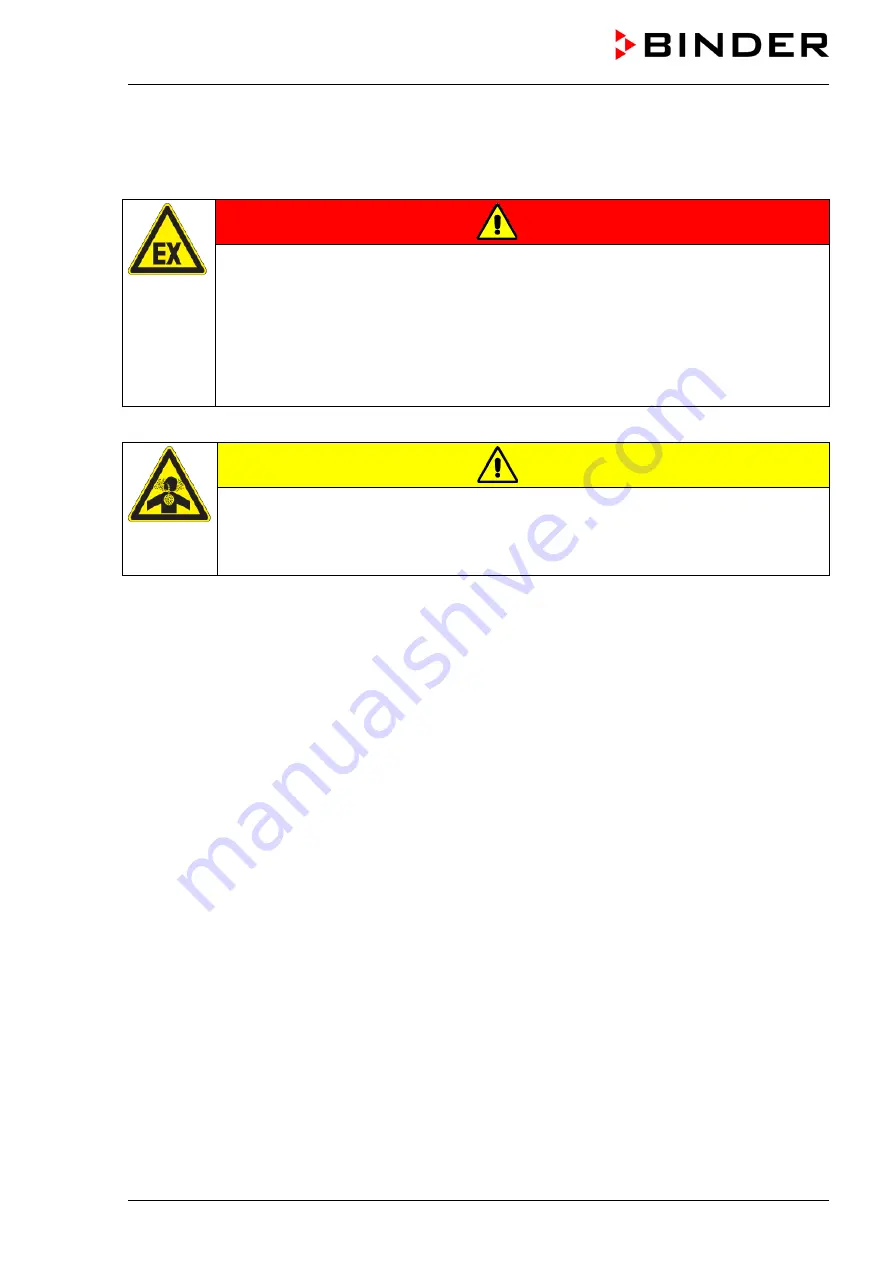
VDL (E3.1) 06/2020
Page 64/206
Observe the permissible gas inlet temperature of the vacuum pump in use.
Do NOT exceed this
temperature. If the gas inlet temperature is too high and then becomes even warmer by compression in
the pump, the resulting temperature (of the gas-solvent mixture inside the pump) could exceed the sol-
vent’s temperature class and auto-ignition temperature .
DANGER
Fire and explosion hazard by exceeding the auto-ignition
temperature of the solvent
with a too high gas inlet temperature.
Damage to the vacuum pump. Serious injury or death from burns and / or explosion
pressure.
Do NOT exceed the maximum gas inlet temperature of the pump. Adjust the tempera-
ture set-point accordingly.
With a higher set-point temperature, take appropriate measures to cool down the ex-
tracted vapor before it enters into the vacuum pump.
Extracted vapors can have a health damaging and/or corrosive effect on the chamber and pump.
CAUTION
Health hazard due to release of extracted vapors.
Corrosion
of oven and pump. Damage to health.
Conduct the extracted vapors e.g., into a fume extractor facility. Connect a suitable
hose to the vacuum pump outlet that may be located in the pump module.
To avoid condensation inside the chamber and in the suction system, select an appropriate vacuum
source to ensure its sufficient performance in relation to the released amount of steam. Coordinate drying
temperature, suction performance of the vacuum source and the amount of loading material.
Содержание vdl 115
Страница 192: ...VDL E3 1 06 2020 Page 192 206 28 6 Dimensions 28 6 1 VDL 23 Dimensions in mm ...
Страница 193: ...VDL E3 1 06 2020 Page 193 206 28 6 2 VDL 56 Dimensions in mm ...
Страница 194: ...VDL E3 1 06 2020 Page 194 206 28 6 3 VDL 115 Dimensions in mm ...
Страница 197: ...VDL E3 1 06 2020 Page 197 206 30 Certificates and declarations of conformity 30 1 EU Declaration of Conformity ...
Страница 198: ...VDL E3 1 06 2020 Page 198 206 ...
Страница 199: ...VDL E3 1 06 2020 Page 199 206 ...
Страница 200: ...VDL E3 1 06 2020 Page 200 206 31 Product registration ...
Страница 207: ......