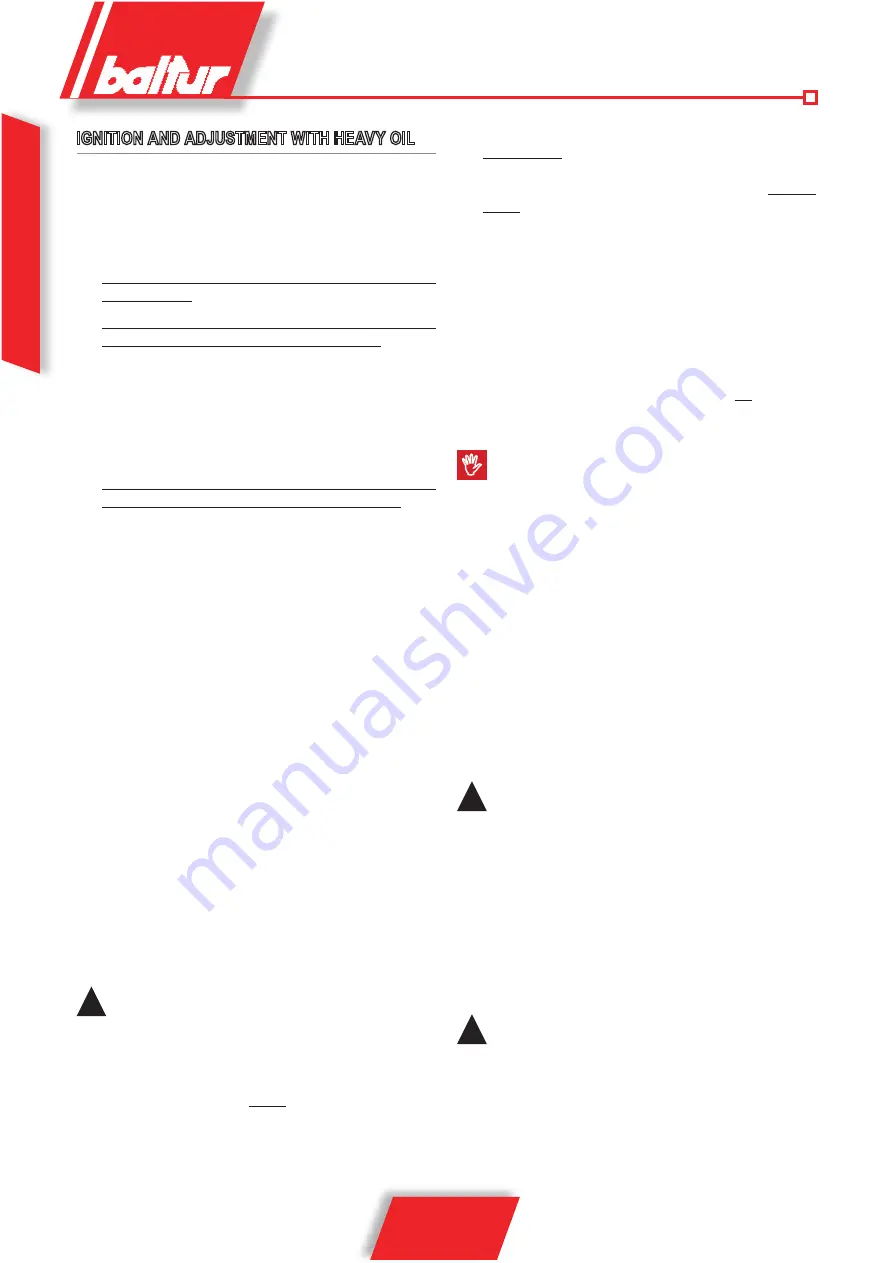
14 / 28
0006080844_201003
E
N
G
L
I
S
H
IGNITION AND ADJUSTMENT WITH HEAVY OIL
1) Check that nozzle characteristics (flow and spray angle) are
suitable for the combustion chamber (see BT 9353); if they are
not replace the nozzle with one that is suitable.
2) Check that there is fuel in the tank and that it is, at least on a
visual check, suitable for the burner.
3)
Check that there is water in the boiler and that system gate
valves are open.
4)
Check with absolute certainty, that combustion products are
able to escape freely (boiler damper and flue open).
5) Check that the voltage on the power line to which you intend
to connect corresponds with that required by the burner and
that all motor and heating element connections are properly
arranged for the available voltage. Check that all electrical
connections made at the installation site are carried out properly
as per our wiring diagram.
6)
Make sure that the combustion head penetrates into the combustion
chamber to the extent requested by the boiler makers.
Check that the air adjuster device on the combustion head is in
a position assumed to be suitable for supply of the relevant fuel
(the air passage between disk and head must be significantly
closed where fuel flow is relatively reduced; on the other hand,
where nozzle flow is rather high, the air passage between disk
and head must be relatively open). See the chapter “Adjusting
the combustion head”.
7) Remove the cover from the rotating disk (on the modulation
motor) where the adjuster screws that control fuel and relative
combustion air are housed.
8) Turn the two modulation switches in the “MIN” (minimum)
position to “MAN” (manual).
9) Adjust the element control thermostat incorporated in the line
filter to around 50° C. Adjust the minimum thermostat “Tmin” in
the preheater thermostats unit to a temperature thought to be
adequate. The temperature to which the minimum ther
-
mostat must be adjusted depends on the type of fuel
used. Consult the viscosity-temperature chart, bea
-
ring in mind that the fuel must reach the nozzle with
viscosity no greater than 2° E. Heavy oil heating tem
-
perature can be modified via the adjuster thermostat
or (where installed) via the “MS 30” electronic regulator; such
temperature must be around 20° C higher than the setting on
the minimum thermostat.
!
The specific instructions for the electronic regulator are given
on the following pages.
10) Start up the auxiliary fuel feed circuit, check that it is working
efficiently and adjust pressure to approximately 1 bar.
11) Remove the plug (on the vacuum meter coupling seat) from
the burner pump and then
slightly
open the gate valve on the
fuel infeed pipe. Wait for the fuel to exit the hole (there should
be no air bubbles) and then re-close the gate valve.
12) Fit a pressure gauge (end of scale approx. 3 bar) to the on-pump
vacuum meter
coupling seat in order to check the pressure
at which fuel arrives at the burner pump. Apply a pressure
gauge (end of scale approx. 30 bar) to the on-pump
pressure
gauge
coupling seat in order to check the working pressure of
the pump itself. Apply a pressure gauge (end of scale approx.
30 bar) to the return pressure regulator coupling to check the
value that determines flow (see drawing. n° 0002900311).
13) Turn the main switch “Q1” to on and the start/stop switch “S1”
to “0” (off) to prevent the elements being switched on with the
tank empty. Make sure that the fan motor and pump motor turn
the right way. For the pump motor turn the switch “S1” to on
and press the tank loading switch; for the fan motor manually
close contactors “KL” (line) and “KY” (star) simultaneously by
pushing the mobile part of the contactor; do
not
close “KD”
(triangle). To invert the direction of rotation exchange two power
line wires relative to the motor which turns the wrong way.
I
WARNING. Pressing the tank loading button cuts power to
the control box and the heating elements on the preheaters
are therefore off. Nevertheless, do not turn on the preheater
elements with the preheater tank empty.
14) Run the burner pump by pressing the tank filling button until the
gauge that reads the working pressure of the pump shows slight
pressure. Slight pressure in the circuit confirms that preheater
tank filling has been completed.
15) Close burner switch “S1” and the main switch. The elements
contained in the fuel preheaters are thus turned on. Switching
on of the elements is signalled by the relative control panel
indicator lights. The contactor coils on elements “KR1” and
“KR2” are powered via contacts “Y1” and “Y2” of the “MS 30”
electronic temperature regulator (where applicable) or the
regulator thermostat. The burner still does not start because
minimum thermostat consensus is absent (i.e. the fuel in the
preheater is not hot enough).
!
Do not turn on the elements with the tank empty as doing so
could damage them.
16) The minimum thermostat closes its contact (i.e. comes on)
when the temperature in the preheater reaches its setting
value. Tripping of the minimum thermostat immediately cau
-
ses switching on of the burner control box (as long as boiler
safety thermostats/pressure switches are closed).
With the burner control box now on the burner ignition sequence
begins. The programme includes simultaneous pre-ventilation
and pre-circulation, with low pressure hot oil, throughout the
burner fuel circuit. Burner ignition is as described in the previous
chapter, “Description of Operation”; the burner is ignited at its
minimum.
!
To adjust the gas pilot flame proceed as follows:
- disconnect the wire from terminal n° 18 of the LFL...
control box to prevent the electromagnet being
switched on.
- disconnect the wire from terminal n° 17 of the LFL...
Содержание GI 1000 DSPN-D
Страница 2: ......
Страница 4: ......
Страница 32: ......
Страница 59: ...59 68 0006080844_201003 ...
Страница 60: ...60 68 0006080844_201003 ...
Страница 61: ...61 68 0006080844_201003 ...
Страница 62: ...62 68 0006080844_201003 ...
Страница 63: ...63 68 0006080844_201003 ...
Страница 64: ...64 68 0006080844_201003 ...
Страница 66: ...66 68 0006080844_201003 CONNETTORE RAMPA PILOTA PILOT GAS TRAIN CONNECTOR CONECTOR RAMPA PILOTO ...