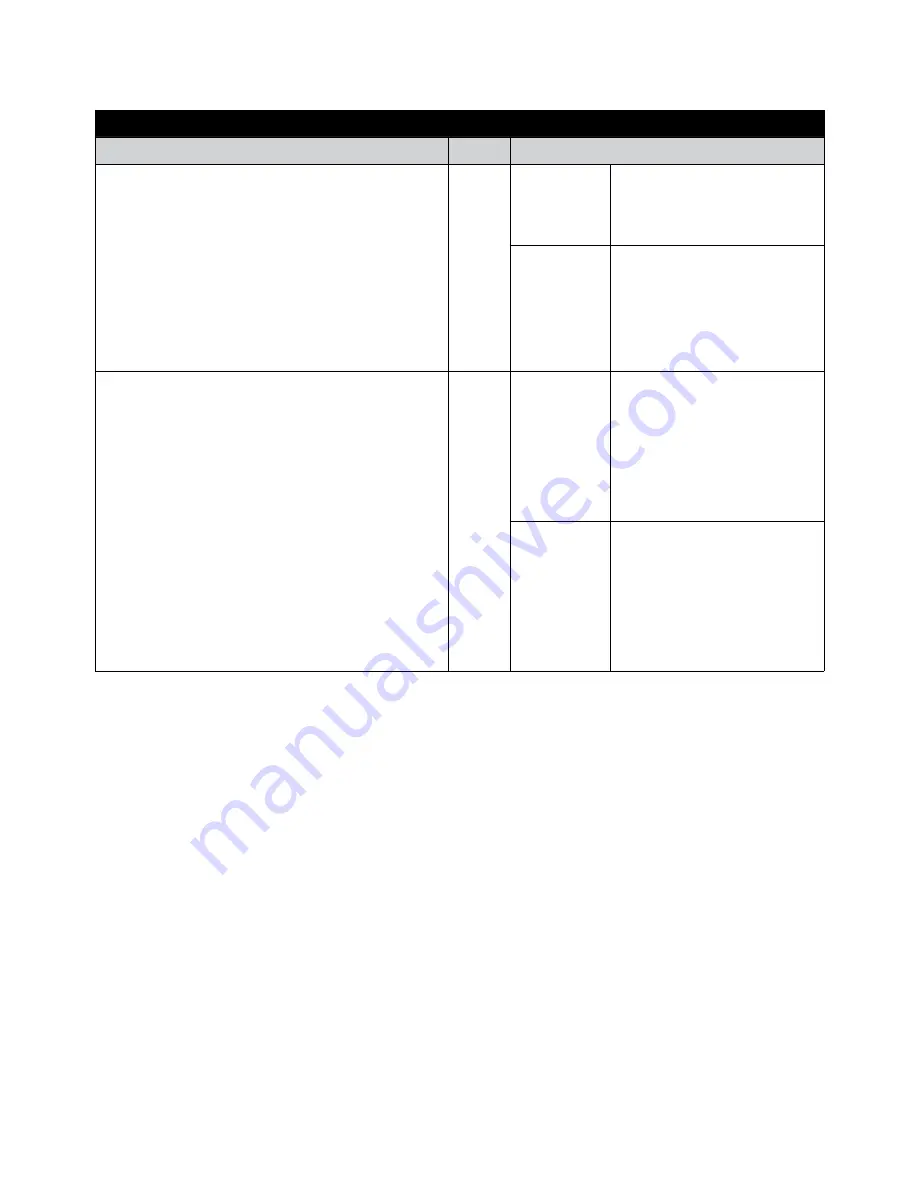
Note 1: A combination of Class I and II parts will satisfy maintenance requirements 85% of the time.
XXVI. Recommended Spare Parts
Table 23: Recommended Spare Parts for 2900 Series POSRV
1
Class
Part Name
Class I Parts should be stocked at the rate of one (1)
per valve. Maintaining this level of spare parts will
provide replacement parts for 70% of possible main-
tenance requirements
I
Pilot Valve
O-Ring Kit
Plug Filter
Main Valve
O-Ring Kit / Gasket Kit
Metal Disc
Nozzle
Bellows (if required)
Disc Retainer
Class II parts should be stocked at the rate of one (1)
part per each five (5) valves in the population. Class II
parts will provide replacement parts for an additional
15% of possible maintenance requirements.
II
Pilot Valve
Main Piston
Tube Fittings (2)
Modulator Stop
O-Ring Retainer
Backflow Preventer Seal Kit
Piston Nose
Main Valve
Disc Holder
O-Ring Retainer (if required)
Guide
Main Valve Piston
1 set of Nuts and Studs
Tube Fittings (2)
90 | BHGE
© 2018 Baker Hughes, a GE company. All Rights Reserved.