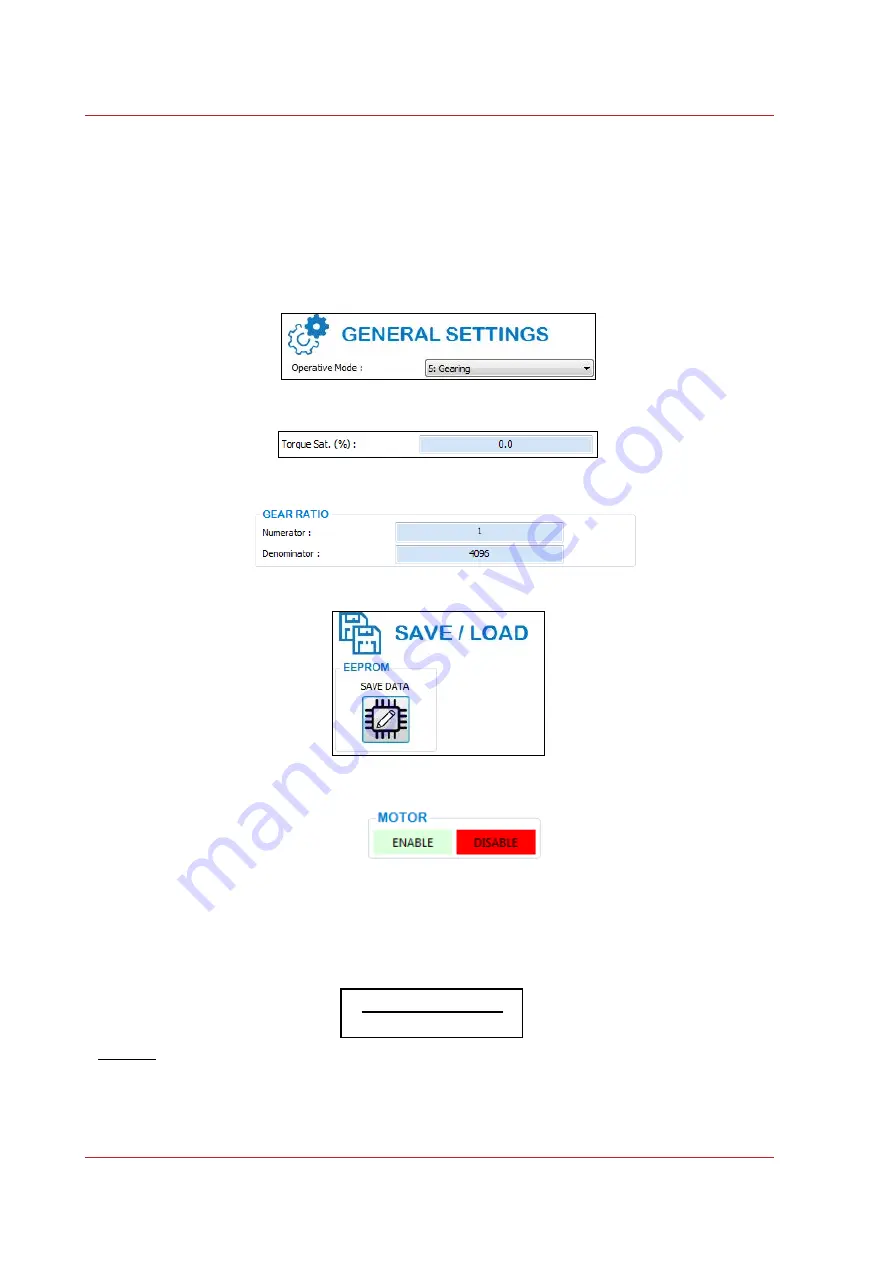
72
AXOR Industries
Service Manual
NanoMack
®
ver.1 rev.11/'19
4.7 Gearing
It is possible to control the drive as a Slave by using the
increasing channels of an external encoder
or
the emulated encoder signals from a CN
, in this case:
1
- Perform the
basic installation procedure (
see cap. 2.5 Basic installation on page 28 )
;
2
- Use the
J1-13/J1-14
pins to connect relatively encoder sCHA / +CHB
(
.
3
- Set the operative mode "
5:Gearing
" in the OP. MODE menu.
4
- It is possible to limit the torque by setting the % of Imax by the value Torque Sat.(the value
0,0% disable this function)(*).
5
- Open the "
Position Loop
" window insert into the numerator and denominator of the
Gear Ratio
,
the ratio that allows you to obtain the desired Slave speed in regards to the encoder.
Example: For 4096 pulses/revolution set as in figure(1/4096)
6
-
Save
Data to Eeprom.
7
-
Enable/disable the drive by using the
Enable
/
Disable
buttons or 24V to the
D.IN1
(
ENABLE
) input. The motor will remain blocked in torque with the position loop inserted and waiting
to move.
8
- When the pulse’s arrive at the inputs the motor will move.
ATTENTION: If the rotation is irregular or noisy, it should be necessary to
adjust the gains
of the speed loop
or
position loop
by using an adequate procedure.
(*) Insert the calculate torque reference using this formula
:
I
desired
x 100
I
peak
Example: Suppose we want to set a digital torque reference equal to 5A, having a drive size of 10/20
(10A=rated current, 20A=peak current)
insert in the window Torque Sat. the value 25, in fact
(5x100)/20=25.
The value 0,0% disable the function.