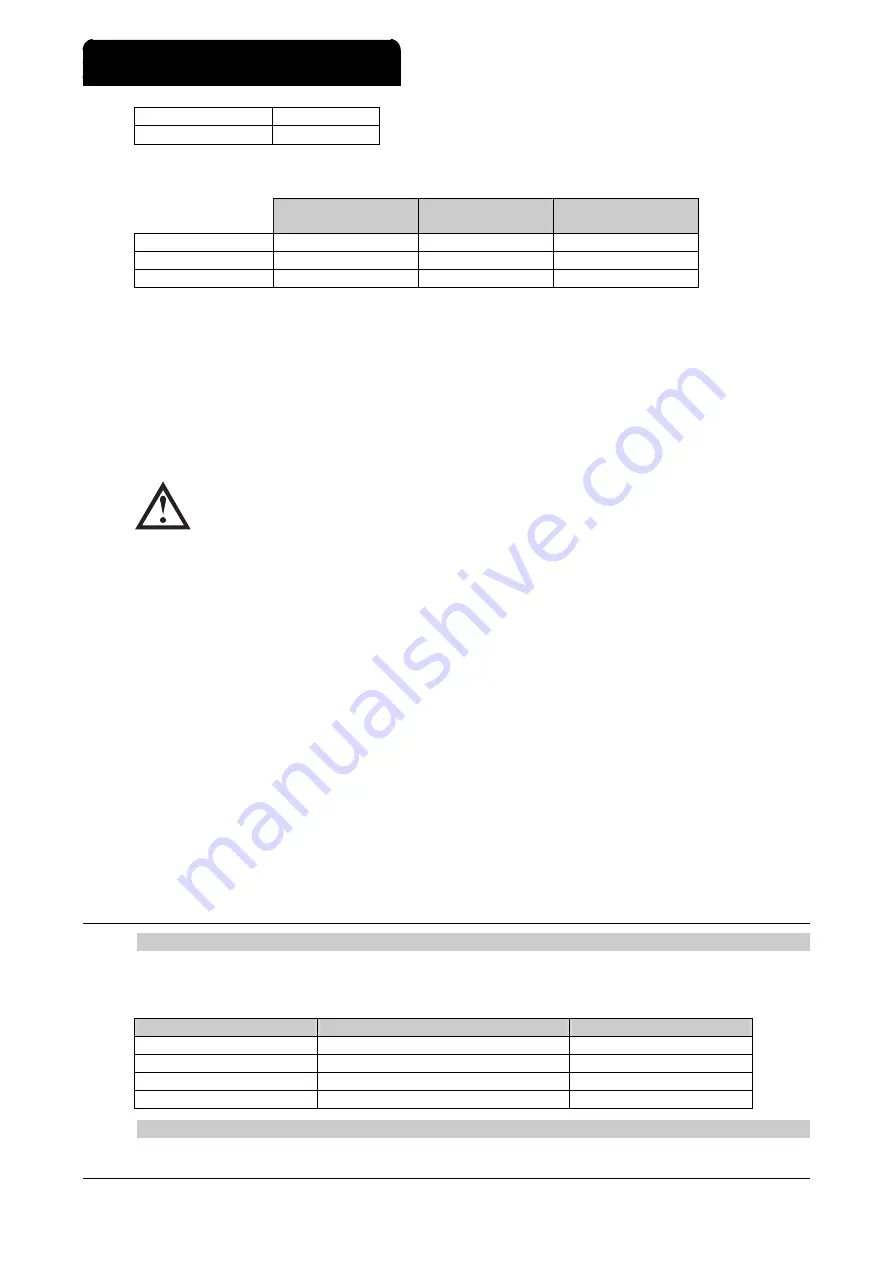
APPENDIX
Page 64
MVS User Manual
710-13019-00A
500 A
–-
600 A
400RC315*
* two fuses in parallel
Fuse type code formats:
System Voltage
2.3 kV
System Voltage
3.3 ~ 4.2 kV
System Voltage
6 ~ 7.2 kV
Ferraz A240Rrr
A480Rrr-1 A072xxDxRO-rr
Bussmann JCK-x-rr JCL-x-rr JCR-x-rr
Siba –
400RC315*
400RC315*
* two fuses in parallel
rr = R rating of the fuse
x = physical format of the fuse (select according to installation requirements)
Examples:
6R fuse for 2.3 kV: A240R6R or JCK-A-6R
12R fuse for 3.3 kV: A480R12R-1 or JCL-B-12R
18R fuse for 6.6 kV: A072B1DARO-18R or JCR-B-18R
Power Factor Correction
NOTE
Do not connect power factor correction capacitors to the output of MVS soft starters. If static power factor
correction is employed, it must be connected to the supply side of the soft starter.
Power factor correction capacitors should be selected based on the motor data and the required final power factor.
If power factor correction capacitors are being used, select a contactor according to the required kVAr. The contactor
must be connected on the supply side of the soft starter. The power factor correction capacitor contactor coil is
associated with output terminals 33, 34 of the soft starter's Interface PCB.
Line Inductors
Output line inductors are required if the cable run between the soft starter and the motor is greater than 200 m. Line
inductors should be installed outside the panel, between the soft starter output (terminals T1, T2, T3) and the motor.
Contact your local supplier for selection details.
Transient/ Overvoltage Protection
Overvoltage protection should be installed if there is a risk of high voltage transients at the installation. Contact your local
supplier for details.
Control Supply Transformer (PT/VT)
The MVS requires a low voltage control supply. If low voltage is not available, a transformer is required. Use a
transformer with primary voltage matching the MV mains voltage, and secondary voltage to suit the MVS starter. Use a
single phase 500 VA transformer with protection fuses on both the primary and secondary sides.
11.3
Maintenance
Maintenance Schedule
The table below lists the minimum maintenance requirements. Your maintenance program may include more frequent
maintenance. In certain environmental conditions (such as dusty or humid environments), increase the frequency of
maintenance to every year.
Part
Instructions
Timing
Control terminals
Check tightness Every
2
years
Earthing terminals
Check tightness Every
2
years
Cable lugs
Check tightness Every
2
years
General MVS
Cleanliness Every
2
years
Tools required
MVS starters can be serviced with the following tools:
Содержание MVS
Страница 1: ......
Страница 67: ...APPENDIX Page 66 MVS User Manual 710 13019 00A ...
Страница 68: ...APPENDIX 710 13019 00A MVS User Manual Page 67 ...
Страница 69: ...APPENDIX Page 68 MVS User Manual 710 13019 00A ...
Страница 70: ...È710 13019 00A ËÍ 7 1 0 1 3 0 1 9 0 0 A ...