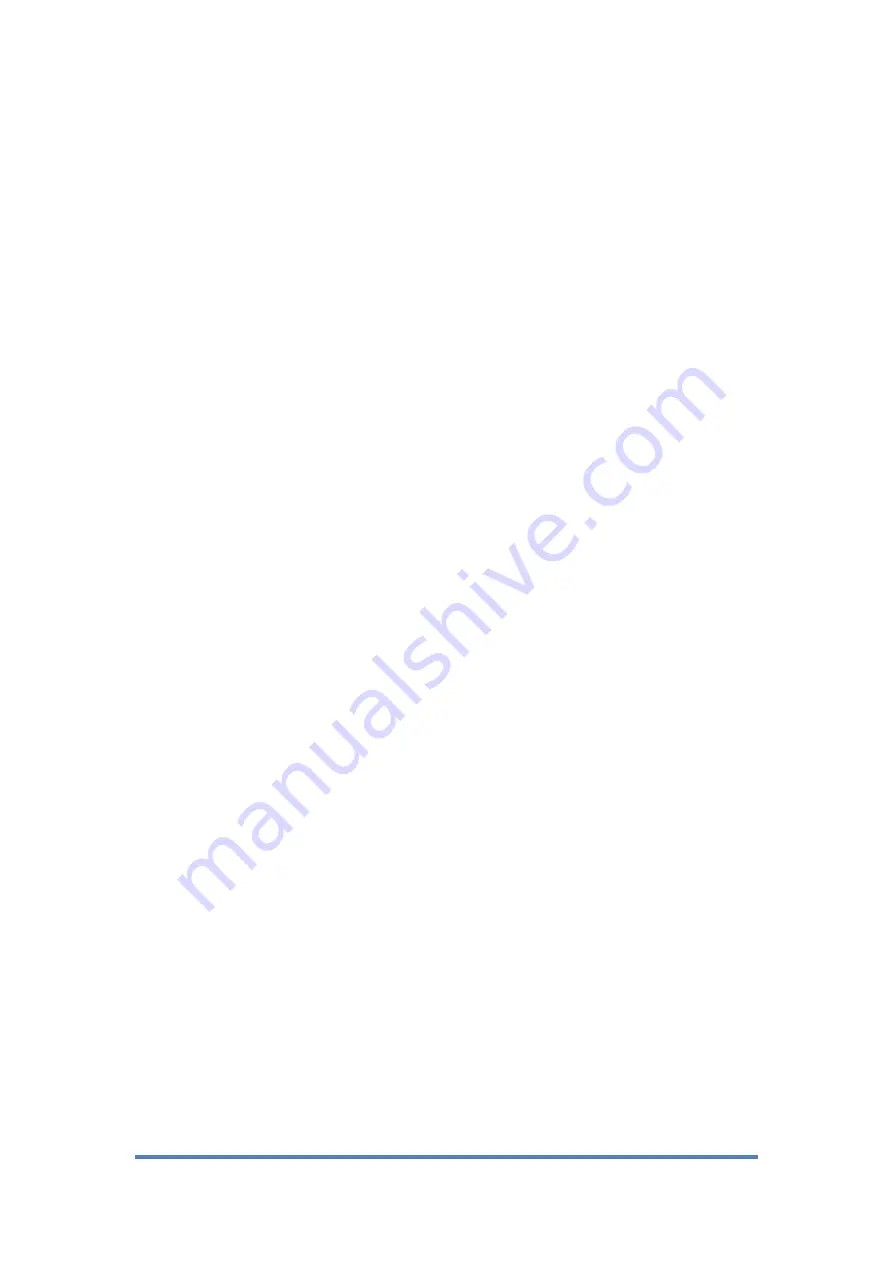
NANOSYSTEM
FABRICATION
FACILITY
(NFF),
HKUST
Version
1.0
Page 12 of 18
10-20 seconds.
b. Wait for the pressure to drop to the crossover pressure, i.e. for the
cryopump to take over at about 150 mTorr. This will take 5 minutes
4. Typically around one hour for the chamber to pump down to about 9.0e-7 Torr
or below.
4.10 Deposition
On the MAXTEK MDC-360C Deposition Controller console:
1. Power “ON” deposition controller.
2. Press “ABORT” and “RESET” for clear previous user’s process record.
3. Select “VIEW/EDIT PROCESS” and entry to make your process for E-Beam
process.
4. The material library is located in “VIEW/EDIT MATERIAL”, we do not open
to public for modify and with a password for protection.
5. Select correct process number (available process number 2 for Au, 3 for Ti, 4
for Al and 6 for Ni, 1, 5, 7-8 are empty).
6. Set deposition thickness (e.g. key 1.234 = 1234A)
7. Deposition Rate is fixed on 1A/s.
8. Check that the correct parameters (e.g. process number & name [=NOTE
column], thickness and material) are displayed at the top of the screen.
9. Back to “MAIN MENU” by “<-“button in Arrow Keys.