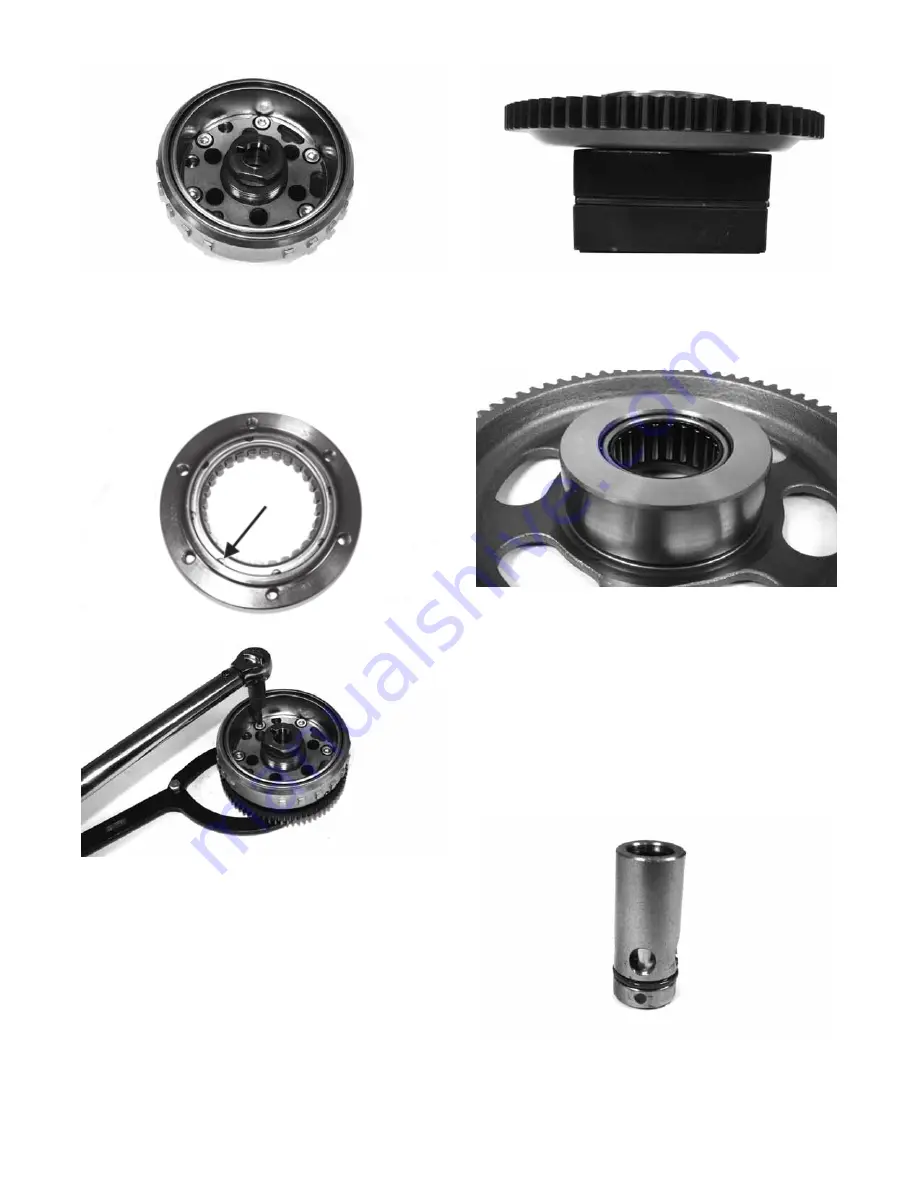
57
FI570
2. Thoroughly clean the rotor/flywheel; then install the
new clutch and secure with the cap screws after
applying a drop of red Loctite #271 to the threads.
Tighten to 26 ft-lb using a crisscross pattern. Make
sure the one-way bearing is installed with the
notches directed away from the rotor/flywheel.
FI576A
FI578
REPLACING STARTER GEAR
BEARING
1. Support the starter clutch gear in a press making sure
to support the hub around the entire circumference;
then using a suitable bearing driver, press the bearing
from the gear.
FI583
2. Thoroughly clean the gear hub; then apply a drop of
green Loctite #620 to the bearing outer race and
press into the gear hub until even with the lower
chamfer radius.
FI580
INSPECTING STATOR/MAGNETO
COVER ASSEMBLY
1. Inspect the stator for burned or discolored wiring, broken
or missing hold-down clips, or loose cap screws.
2. Inspect the bearings in the magneto housing for discolor-
ation, roughness when rotated, and secure fit in bearing
bores.
3. Inspect the oil pressure relief valve for evidence of metal
chips or contamination. Do not disassemble the valve.
FI588
Содержание PROWLER HDX 2015
Страница 3: ......
Страница 191: ...188 NOTES...
Страница 192: ...Printed in U S A Trademarks of Arctic Cat Inc Thief River Falls MN 56701 p n 2260 410...