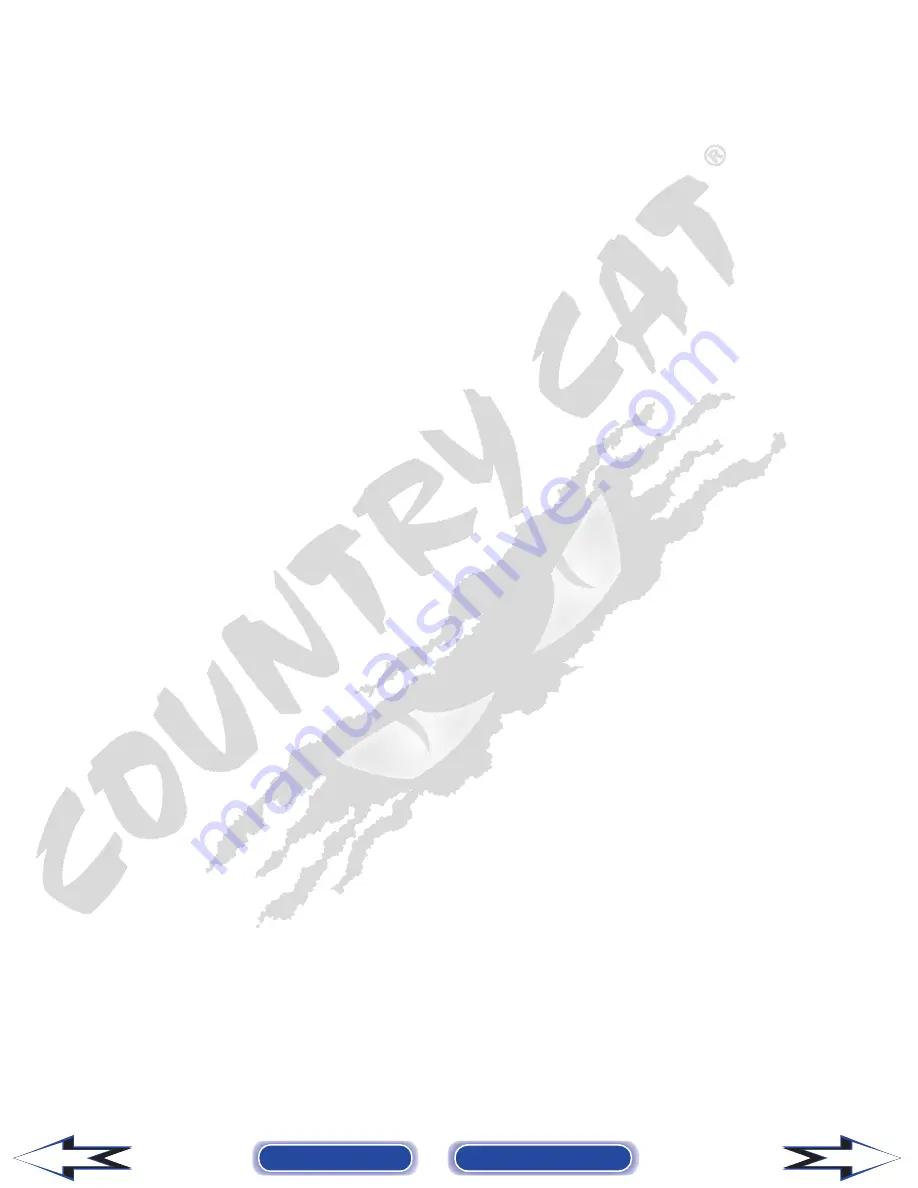
3-48
12. Place the air filter assembly into position and
secure with the self-tapping screws; then connect
the intake boot to the carburetor/throttle body and
the inlet housing boot to the air filter housing.
Tighten the clamps securely.
13. Place the shifter assembly into position and secure
with the four machine screws. Tighten securely.
14. Connect the shifter linkage to the transmission
shift arm placing the washer and bushing in appro-
priate locations (XT) or connecting the cable
(Prowler/XTX); then secure with the E-clip.
NOTE: Before operating vehicle, check and adjust
shifter linkage/cable as required (see Section 2).
15. Fill the engine/transmission with the appropriate
lubricant.
16. Fill the cooling system with the appropriate coolant.
17. Connect the positive battery cable to the battery;
then connect the negative cable.
18. Install the left-side and right-side seat-bases; then
install the center console and seats. Make sure the
seats lock securely.
19. Start the engine and warm up to operating temper-
ature. Check for fluid leaks; then shut off engine
and check oil and coolant levels (see Section 2).
Back to TOC
Back to Section TOC
Next
Back