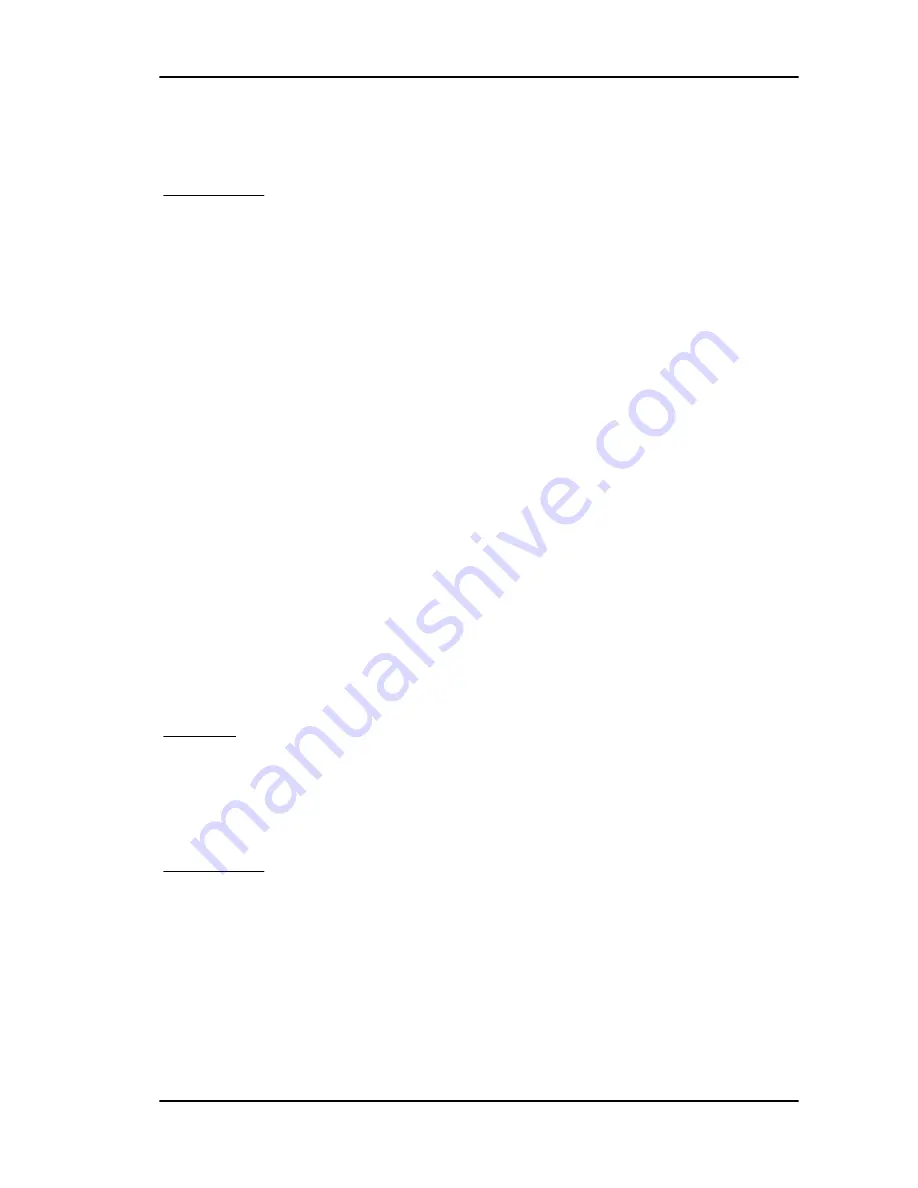
•
If the circuit is open, shorted to negative: voltage equal to zero has been detected at PIN 34
of the VEHICLE connector.
Troubleshooting
•
If short circuit to positive, see that the parameter of the front Cylinder Intake Pressure on
the diagnosis instrument reads approx. 1200 mbar; disconnect the large connector from the
filter casing: if the value does not vary, it means that the cable is shorted between the filter
casing connector and the control unit connector; restore the cable harness. If the value
varies, reconnect the filter casing connector and disconnect the sensor connector: if the
value does not vary, it means that the cable is shorted between the filter casing connector
and the sensor connector; restore the cable harness. Replace the sensor if the value varies.
•
If the circuit is open, short circuit to negative, check filter casing large connector, the Marelli
control unit connector and the sensor connector. If not OK, restore. If everything is OK, and
with key set to OFF, check if there is continuity between the VEHICLE PIN 34 of the Marelli
control unit and the sensor connector PIN 3: if there is no continuity, restore the cable har-
ness. If there is continuity, check the cable earth insulation: if there is continuity to ground,
restore the cable harness; if not, with key set to ON check that the voltage on sensor con-
nector PIN 1 is approx. 5 V: if this is not correct, set the key to OFF and check continuity
between the ENGINE connector PIN 15 and the sensor connector PIN 1: If not OK, restore
the cable harness; if it is OK, replace the control unit. if there is 5V voltage at PIN 1, and
with key set to ON, check the continuity to ground of the sensor connector PIN 3: If not OK,
restore cable harness; if it is OK, replace the sensor.
Rear cylinder air pressure sensor P0106 -
short circuit to positive / open circuit, short circuit to neg-
ative.
Error cause
•
If shorted to positive: excessive voltage has been detected at PIN 5 of the VEHICLE con-
nector.
•
If the circuit is open, shorted to negative: voltage equal to zero has been detected at PIN 5
of the VEHICLE connector.
Troubleshooting
•
If short circuit to positive, see that the parameter of the front Cylinder Intake Pressure on
the diagnosis instrument reads approx. 1200 mbar; disconnect the large connector from the
filter casing: if the value does not vary, it means that the cable is short circuited between the
filter casing connector and the control unit connector; restore the cable harness. If the value
varies, reconnect the filter casing connector and disconnect the sensor connector: if the
value does not vary, it means that the cable is short circuited between the filter casing con-
nector and the sensor connector; restore the cable harness. Replace the sensor if the value
varies.
SL 750 SHIVER
Electrical system
ELE SYS - 41
Содержание SL 750 SHIVER
Страница 1: ...SERVICE STATION MANUAL 854146 SL 750 SHIVER ...
Страница 4: ......
Страница 6: ......
Страница 7: ...INDEX OF TOPICS CHARACTERISTICS CHAR ...
Страница 28: ...Characteristics SL 750 SHIVER CHAR 22 ...
Страница 29: ...INDEX OF TOPICS SPECIAL TOOLS S TOOLS ...
Страница 37: ...INDEX OF TOPICS MAINTENANCE MAIN ...
Страница 50: ...Maintenance SL 750 SHIVER MAIN 14 ...
Страница 51: ...INDEX OF TOPICS TROUBLESHOOTING TROUBL ...
Страница 59: ...INDEX OF TOPICS ELECTRICAL SYSTEM ELE SYS ...
Страница 76: ...Electrical system SL 750 SHIVER ELE SYS 18 ...
Страница 141: ...INDEX OF TOPICS ENGINE FROM VEHICLE ENG VE ...
Страница 148: ...Engine from vehicle SL 750 SHIVER ENG VE 8 ...
Страница 149: ...INDEX OF TOPICS ENGINE ENG ...
Страница 222: ...Engine SL 750 SHIVER ENG 74 ...
Страница 223: ...INDEX OF TOPICS POWER SUPPLY P SUPP ...
Страница 230: ...Power supply SL 750 SHIVER P SUPP 8 ...
Страница 231: ...INDEX OF TOPICS SUSPENSIONS SUSP ...
Страница 257: ...INDEX OF TOPICS CHASSIS CHAS ...
Страница 267: ...INDEX OF TOPICS BRAKING SYSTEM BRAK SYS ...
Страница 274: ...Braking system SL 750 SHIVER BRAK SYS 8 ...
Страница 275: ...INDEX OF TOPICS CLUTCH SYSTEM CLU SYS ...
Страница 277: ...INDEX OF TOPICS COOLING SYSTEM COOL SYS ...
Страница 286: ...Cooling system SL 750 SHIVER COOL SYS 10 ...
Страница 287: ...INDEX OF TOPICS BODYWORK BODYW ...
Страница 290: ... Remove the cover Undo and remove the screw Remove the side fairing Bodywork SL 750 SHIVER BODYW 4 ...