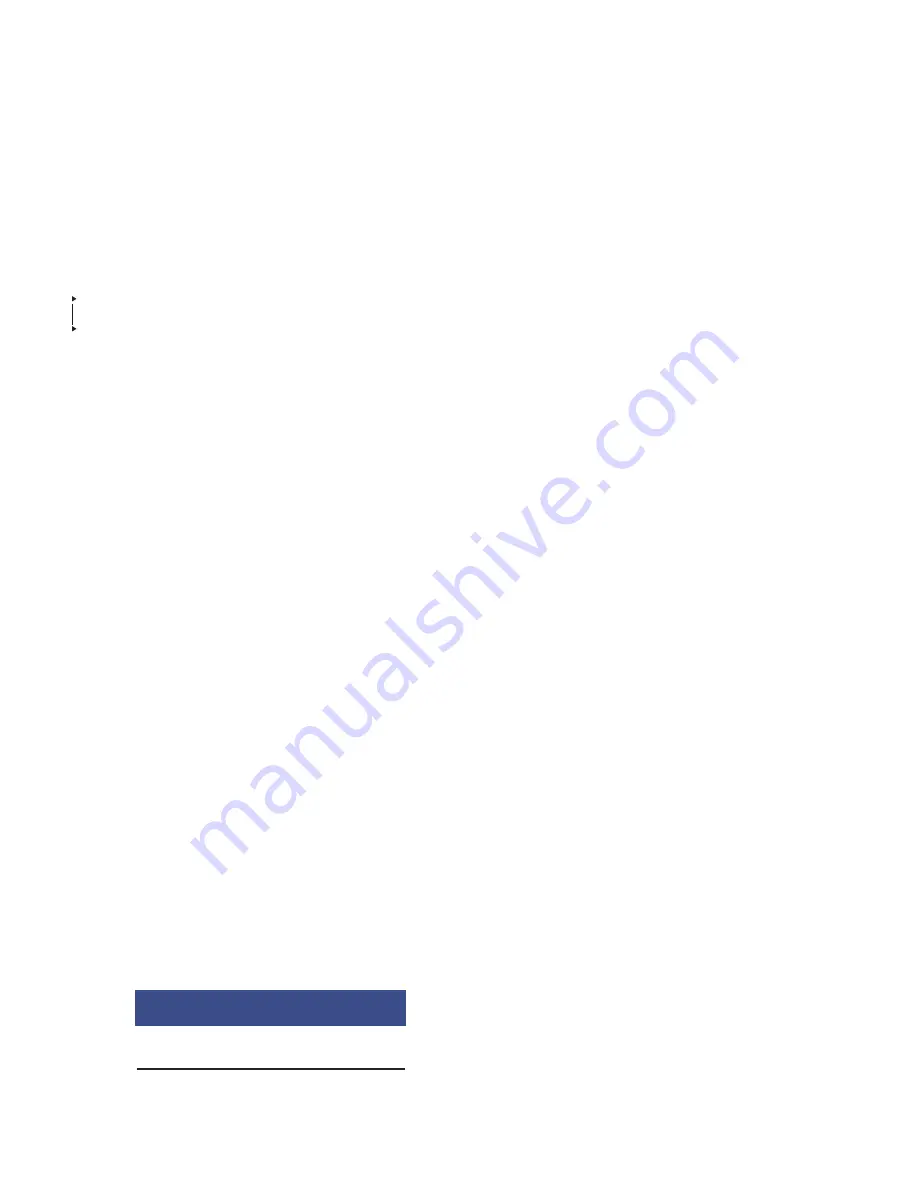
SECTION 4 – SYSTEM PLANNING
2014-AUG-28 rEV. 02 PAGE 4-7
CHECKFIRE 110
Detection and Actuation System
Power Circuit Cables (Green Connectors)
Connects CHECKFIrE 110 Control Module to 12/24 VDC
nominal vehicle power source using the Power Circuit Cable
and the Fused Power Circuit Cable (connects to vehicle power
supply).
1. Determine location of power source that will provide the
following current load capabilities:
sYsTEM CUrrENT DrAW
Nominal < 6 mA @ 10.2 – 28 VDC
• Maximum < 100 mA @ 10.2 – 28 VDC
2. Plan route for the Power Circuit Cable from the control
module to the end point of the Fused Power Circuit Cable
(note end points for both cables). Choose a path in acces-
sible locations providing protection from undue wear,
damage, and heat. Keep the cables as far away as possible
from vehicle electric cables, particularly power cables to and
from generators and electric motors; also avoid:
• Antennas and associated cables
• Fire hazard areas
• Areas exposed to mechanical damage
• Proximity to moving parts
• Areas subject to debris accumulation
• Areas exposed to high temperatures (turbo chargers,
exhaust equipment, etc.)
• Areas requiring access by vehicle service and mainte
-
nance personnel
3. Select appropriate cable lengths for area of installation. See
section 2 - Components, page 2-7, for available sizes.
Alarm Output Circuit Lead – Digital 3.3 VDC
The Digital 3.3 VDC Alarm Output Circuit lead (Yellow plug)
on the CHECKFIrE 110 Control Module is an 18 AWG, two
conductor polarity sensitive cable assembly. The white conduc
-
tor is positive and the black conductor is negative.
This circuit is initiated by an alarm condition. The output is not
intended to directly operate analog devices such as audible
horns, strobes and relays. However, the installer or OEM can
use the circuit as a logic input to a vehicle operating system or
Programmable logic Controller to manage engine shutdown,
cooling fans, hydraulic pumps, notification devices, relays, etc.
The vehicle operating system, control configuration, and field
wiring must be provided and installed by others.
Note:
removal of the yellow plug on the Alarm Output Circuit
Lead may compromise the IP67 rating for this circuit.
NOTICE
Do not remove the yellow plug unless circuit
is intended for use.
Vehicle System Pressure Switch
The Vehicle system Pressure switch is a manually resettable
4-conductor sPDT switch, rated for 6A when used with volt
-
ages between 12 VDC and 36 VDC nominal. The switch can
be used to perform several different tasks on system actuation,
including equipment shutdown, turning on notification appli
-
ances, or providing “Pressure switch Feedback” to a vehicle
control panel. The switch has one integral cable, sealed to the
end of the switch housing with 3-conductors (NO/NO/C/NC) for
field connections.
Install switch in expellant gas actuation line using a 1/4 in.
tee at the inlet port on the agent tank. Make certain to protect
switch and connections from potential damage.
Planner/Installer must verify contact ratings of devices intended
for pressure switch connection. Connections to vehicle
device(s) to be made by others, or with vehicle manufacturer’s
direct instruction and approval.
Note:
Pressure switch activates on expellant gas release.
CHECKFIrE 110 Control Module is unable to monitor or verify
pressure switch operation.
Label Package
Include a label Package (Part No. 440798) to identify specific
procedures of the system to vehicle operators.
System Layout
Once components are selected and locations are determined,
complete a final drawing of the system layout. This drawing
should at a minimum include the following:
• Hazard area locations
• Component locations (include vehicle power source)
• routes for all connecting circuits with cable lengths iden
-
tified.
Indicate areas where cable must pass-through bulkheads.
Use circuit bulkhead connectors to support and protect cables.
(Confirm acceptable pass-through locations with vehicle manu
-
facturer.) The drawing should be as precise as possible to
avoid installation problems later.
Compile a list of components to confirm system includes all
required parts (review Components Planning Checklist, page
4-8). The CHECKFIrE system is complete when all necessary
components combine to provide automatic fire detection and
activation of the fire suppression system for protected areas.
Содержание CHECKFIRE 110
Страница 2: ......
Страница 6: ...REVISION RECORD PAGE 2 REV 0 2014 MAY 01 NOTES CHECKFIRE 110 Detection and Actuation System ...
Страница 22: ...SECTION 3 USER INTERFACE PAGE 3 4 REV 0 2014 APR 30 NOTES CHECKFIRE 110 Detection and Actuation System ...
Страница 68: ...SECTION 7 IN CASE OF FIRE PAGE 7 2 REV 0 2014 APR 30 NOTES CHECKFIRE 110 Detection and Actuation System ...
Страница 84: ...SECTION 9 TROUBLESHOOTING PAGE 9 10 REV 0 2014 APR 30 NOTES CHECKFIRE 110 Detection and Actuation System ...