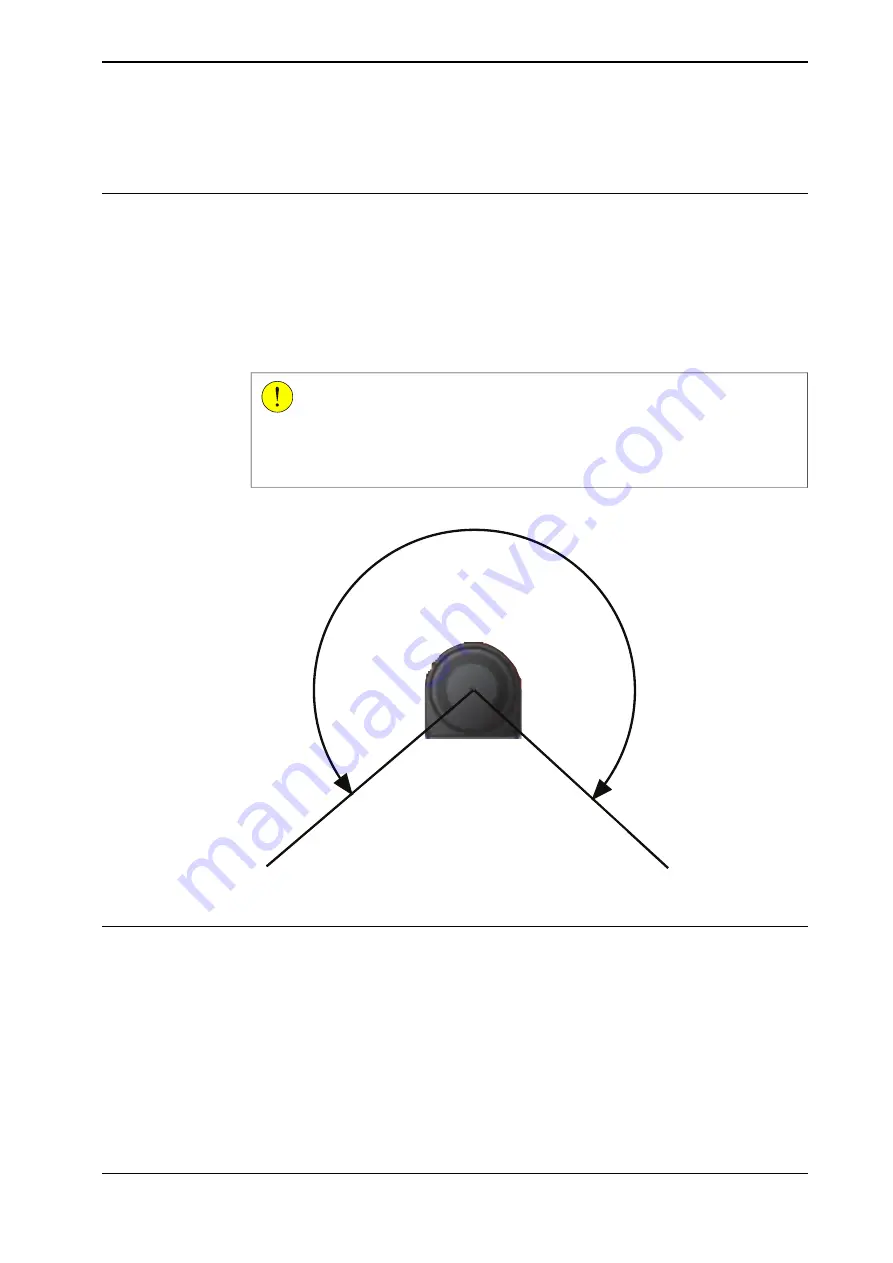
3.3.10 Installation of laser scanner
Overview
The safety separation technology and speed control for CRB 15000 is based on
the connection and communication of one or two safety laser scanners in the robot.
Laser scanner(s) provides a timely and continuous monitor on the activities within
its scanning area and forms a protective field. One laser scanner can provide a
scanning range of approximately 275°. The system integrator shall investigate the
site environment and place the laser scanner to a suitable location according to
the actual requirements.
CAUTION
Safety in the area that not in the scanning range must always be considered.
The system integrator shall assess the potential risks within this area and make
sure that proper measures have been applied to reduce risks.
275°
xx2100000168
Laser scanner types
The following laser scanner package options are available:
•
1 PROFIsafe-based laser scanner (option 3051-1 PROFIsafe scanner)
•
2 PROFIsafe-based laser scanners (option 3051-3 Dual PROFIsafe scanner)
•
1 SafetyIO-based laser scanner (option 3051-2 I/O scanner)
•
2 SafetyIO-based laser scanners (option 3051-4 Dual I/O scanner)
Continues on next page
Product manual - CRB 15000
91
3HAC077389-001 Revision: L
© Copyright 2021 - 2023 ABB. All rights reserved.
3 Installation and commissioning
3.3.10 Installation of laser scanner
Содержание CRB 15000
Страница 1: ...ROBOTICS Product manual CRB 15000 ...
Страница 2: ...Trace back information Workspace 23B version a17 Checked in 2023 06 29 Skribenta version 5 5 019 ...
Страница 8: ...This page is intentionally left blank ...
Страница 16: ...This page is intentionally left blank ...
Страница 38: ...This page is intentionally left blank ...
Страница 54: ...This page is intentionally left blank ...
Страница 182: ...This page is intentionally left blank ...
Страница 200: ...This page is intentionally left blank ...
Страница 1058: ...This page is intentionally left blank ...
Страница 1076: ...This page is intentionally left blank ...
Страница 1095: ......