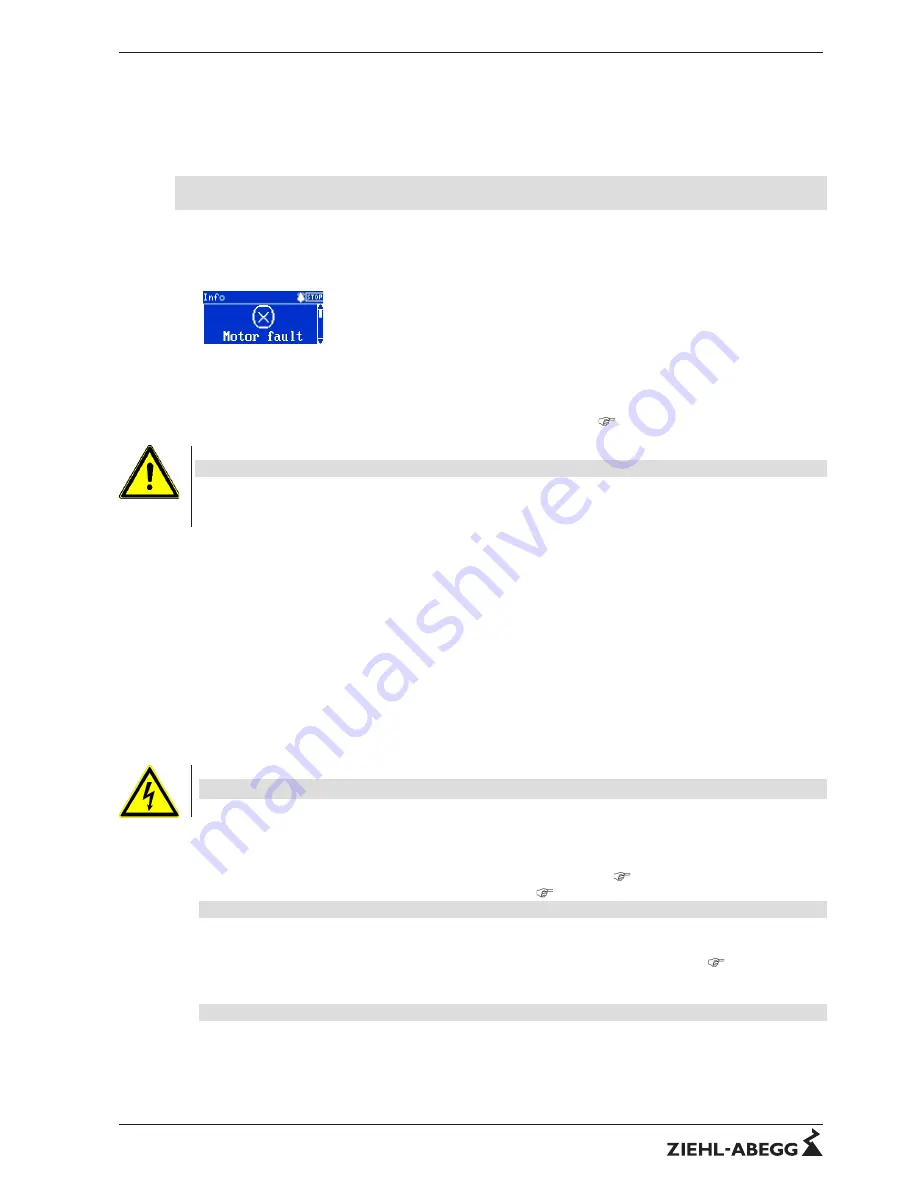
5.7
Motor protection
Motor protection is possible by connecting thermostats
“
TB
”
or thermistors (PTC thermistor)
“
TP
”
.
•
When connecting several motors, always make sure that thremostats
“
TB
”
or thermistors
“
TP
”
are
connected in series. A maximum of six individual thermistors (DIN 44081 or DIN 44082) may be
connected in series to a single device. At least two or three single thermistors are installed depend-
ing on the motor type.
•
Monitoring of motors in Ex zones is not permissible. For systems of this type, an additional posistor
tripping unit is required, with disconnection via a separate motor protection circuit.
The unit switches off when a connected thermostat or thermistor has tripped the circuit (interruption
between both terminals
“
TB/TP
”
. The unit then remains switched off. A programmed fault-indicating
relay is triggering.
Display during motor fault
Possibilities for re-starting after the drive has cooled down terminals
“
TB/TP
”
bridged by:
•
By switching the mains voltage off and then on again.
•
Function
“
Reset
”
Menu group
“
Start
”
•
By digital input for remote (enable ON/OFF) or by Reset-input (
IO Setup - Digital Inputs).
Attention!
•
An outside voltage may never be connected to the terminals
“
TB/TP
”
and/or!
•
If a bypass circuit is installed, or in the
“
100 %
”
position on devices with a main switch, the motor
protection inside the controller has no function. In this case, additional motor monitoring may be
required.
5.8
Signal input or sensor connection (E1, E2)
The unit has two analog inputs: Analog In 1 =
“
E1
”
and Analog In 2 =
“
E2
”
The connection is independent of the programmed operating mode and from the sensor signal
employed.
•
When connecting
passive
temperature sensorsTF.. (KTY81-210) or PT1000 at terminals
“
E1
”
and
“
T
”
or
“
E2
”
und
“
T
”
must be paid attention to no polarity.
For a high interference immunity a capacitor must be connected directly to the sensor (1 nF
parallel). With temperature sensors type TF.. (KTY81-210) a capacitor is integrated.
•
When connecting
aktive
sensors at the terminals
“
E1
”
and
“
GND
”
or
“
E2
”
and
“
GND
”
attention must
be paid to correct polarity, a 24 V DC power supply is integrated.
•
For sensors in two-wire-technology (4 - 20 mA signal), the connection is made on the
“
E1
”
and
“
24 V
”
or
“
E2
”
and
“
24 V
”
,
“
GND
”
terminal is omitted.
Danger due to electric current
Never apply line voltage to analog inputs!
5.9
Analog output (0 - 10 V)
“
A1
”
The analogoutputs 0 - 10 V can be allocated with various functions (
IO Setup: Analog output
“
A
”
).
Connection to terminal
“
A
”
-
“
GND
”
=
“
Analog Out
”
(I
max
technical data / connection diagram).
It is not permissible to connect outputs of several devices to each other!
5.10
Voltage supply for external devices (+24V, GND)
A voltage supply is integrated for external devices e. g. a sensor (max. current load
technical data).
In case of overload or short circuit (24 V
–
GND), the external power supply is shut down (multi-fuse).
The device performs a
“
Reset
”
and continues operation.
It is not permissible to connect outputs of several devices to each other!
Operating Instructions
Fcontrol
–
model series FXDM25/32AM
Electrical installation
L-BAL-E212-GB 1451 Index 003
Part.-No.
16/123