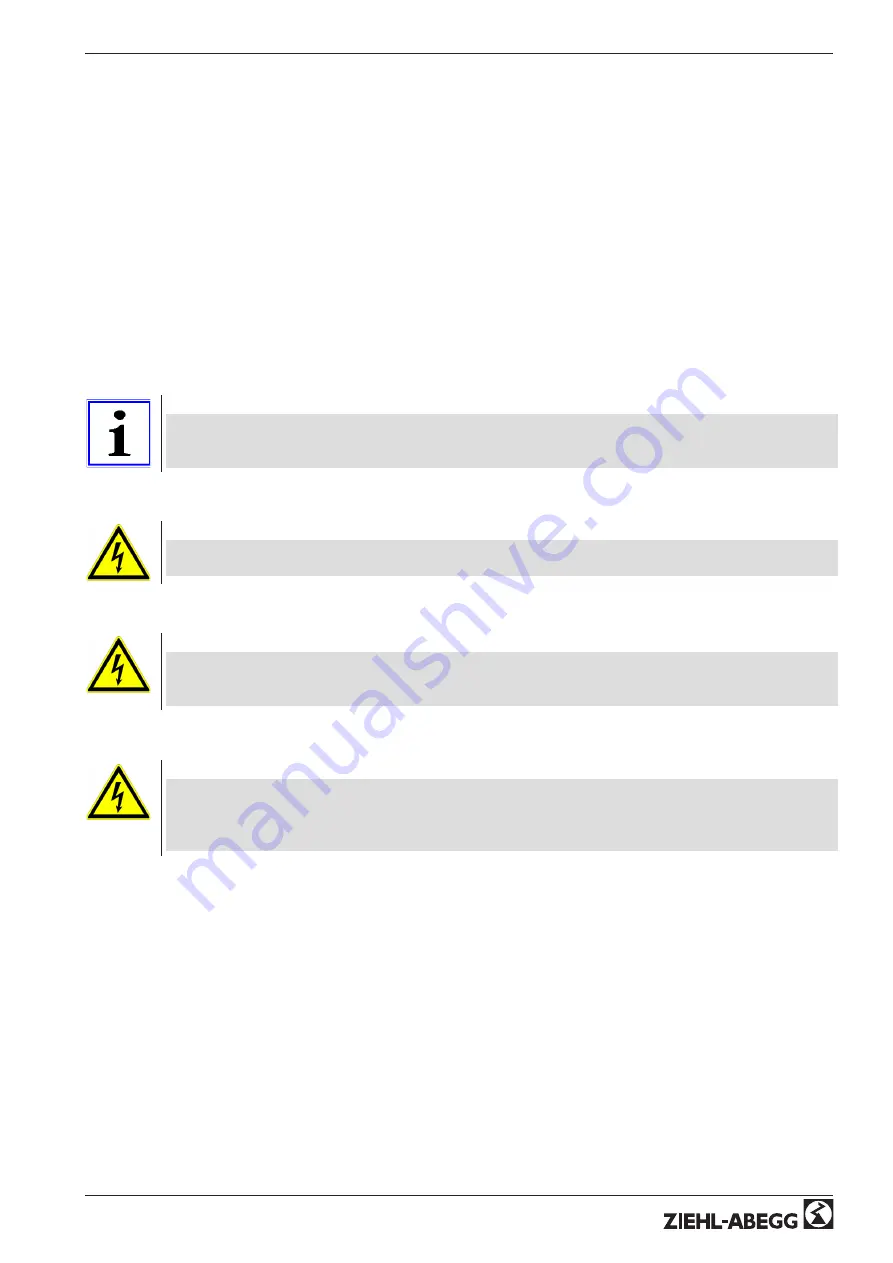
5.2.4Signal cable
Pay attention to suf
cient distance from powerlines and motor wires to prevent interferences. The
control cable may not be longer than 30 m. Screened control cables must be used when the cable
length is longer than 20 m. When using a shielded cable connect the shielding to one side only, i.e.
only to the control unit with the protective ground (keep cable short and with as little inductance as
possible!).
5.3 Mains connection
5.3.1
Line voltage
Power from the mains is connected to terminals: PE, L1, L2, L3 and N. Here, it must be strictly
observed that the mains voltage lies within the allowable tolerance speci
cations (
F
Technical data
and nameplate af
xed to the side).
The neutral conductor connection
“
N
”
is only for the leakage current
´
s reduction. It is of no signicance
for the function of the device. The connection is not applicable for power supply networks without a
neutral conductor. Since higher leakage currents may arise by this across the protective-cable
connection
“
PE
”
, unwanted triggering by mistake may occur in systems with FI protection circuits.
Information
Not suitabble for IT network!
During disconnection of the line voltage the necessary waiting period before renewed
switching on amounts minimum 90 seconds!
5.3.2
Required quality attributes for the mains voltage
Danger owing to electric current
The mains voltage must comply with the DIN EN 50160 quality characteristics and the de
ned
standard voltages in IEC 60038!
5.3.3
Leakage current, securely attached, ground wire double up to 10 mm
²
Danger owing to electric current
In accordance with the de
ned networks in DIN EN 60990, the device has a leakage current >
3.5 mA so it must be permanantly connected. The protective ground must be made double in
accordance with EN 50178 Point 5.2.11and 5.3.2.1 up to a cross section of at least 10 mm
²
.
5.4Residual-current-operated protective device
Danger owing to electric current
For an installation of r.c.d. protection, it shall be observed that this must be of
“
universal-
current sensitivity
”
. In accordance with EN 50 178, Section. 5.2. other types of current-operated
protective devices may not be used. To ensure as high a degree of reliability as possible , we
recommend a tripping current of 300 mA.
Operating Instruction
Econtrol
–
model series EXDM
Electrical installation
L-BAL-E008-GB 0945 Index 005
Part.-No. 00156742-GB
12/85