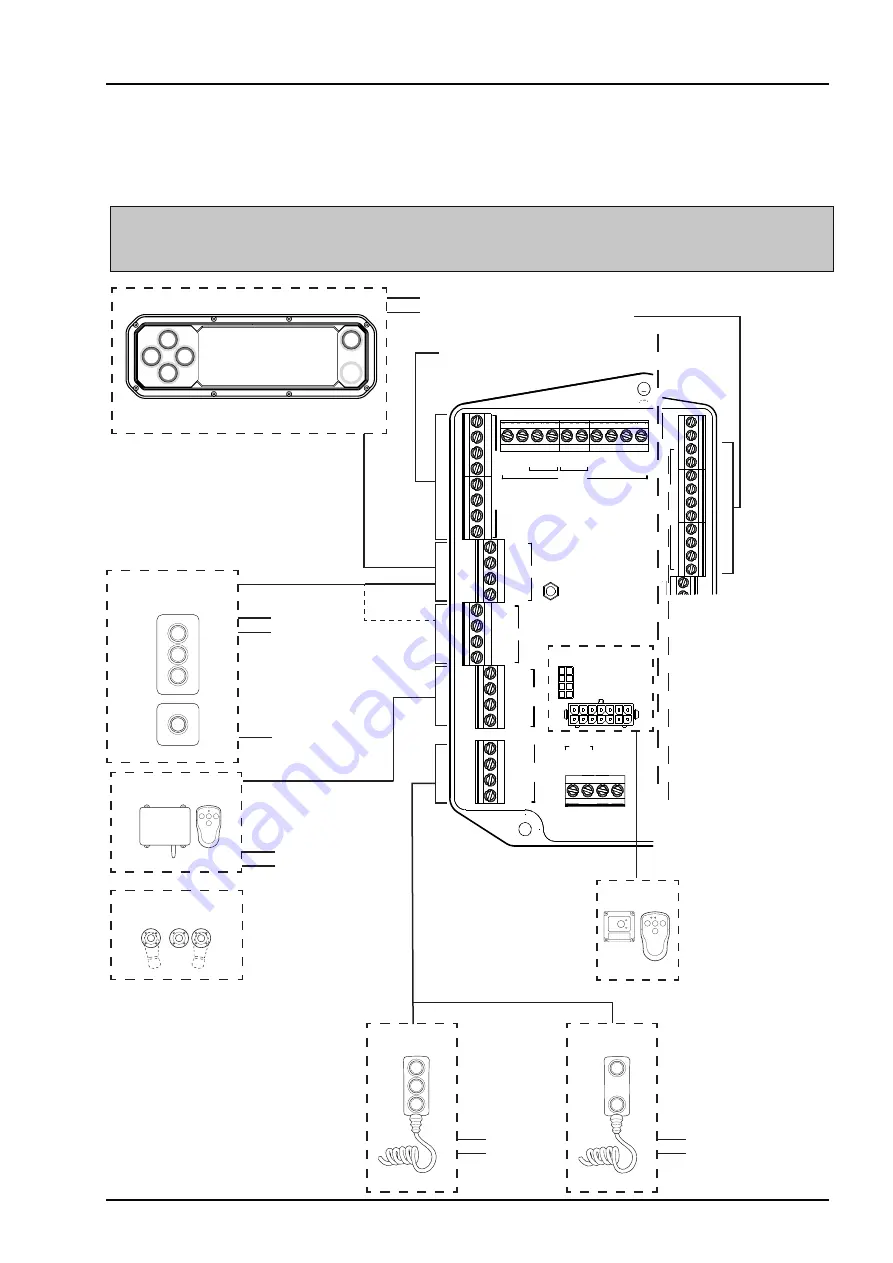
Z 1500/2000-135/155/175
Connection
45
www.zepro.com
6.2.2 Controller (ZePRO1)
The most commonly occurring controller (CD Control Device) models are shown below. Possible controller
models vary depending on lift model, configuration and relevant market.
m
WARNING!
Make sure that the control board is not powered up before connecting. Connecting more than one controller to each connection
is not permitted. Risk of material damage.
Ctrl 4
Spiral
Ctrl 3
Radio
Ctrl 2
Ctrl 1
C
on
tr
l P
ow
er
Sensor Power
G
ro
un
d
IN OUT
Ai 2
Ai 1
Di 1
Di 2
Di 3
Di 4
Di 5
Di 6
PA-
PA+
CSPWR
CS
+
B
E
C
2H1
B
E
C
2H2
B
E
C
Lock
B
E
C
Lock
U
7
U
6
U
5
U
4
U
3
U
5
U
4
U
2
U
1
U
0
Ctrl 6
O
ut
In GND LLED
Ctrl 5
Outputs
Se
ns
or
s
o
CD11
CD1, CD2
B
C
2H1
E
CD15
Black (+)
2H Black (+)
Black (+)
Black (+)
White (-)*
White (-)
CD14
B
S
E
CD12
Ctrl 4
Spiral
Ctrl 3
Radio
Ctrl 2
Ctrl 1
C
on
tr
l P
ow
er
Sensor Power
G
ro
un
d
IN OUT
Ai 2
Ai 1
Di 1
Di 2
Di 3
Di 4
Di 5
Di 6
PA-
PA+
CSPWR
CS
+
B
E
C
2H1
B
E
C
2H2
B
E
C
Lock
B
E
C
Lock
U
7
U
6
U
5
U
4
U
3
U
5
U
4
U
2
U
1
U
0
Ctrl 6
O
ut
In GND LLED
Ctrl 5
Outputs
S
en
so
rs
o
White (-) must be con-
nected to the connec-
tions marked “Ground”.
Brown
B
Yellow
E
Blue
C
Blue
2H
Brown
B
Yellow
E
Blue
C
Grey
Lock
CD9
B
C
E
CD10
B
E
Black (+)
White (-)*
Black (+)
White (-)*
Brown
B
Yellow
E
Blue
C
Brown
B
Yellow
E
Up
Down
Tilt up
Tilt dow
n
2H
Brown
B
Yellow
E
Blue
C
Pink
2H
White (-)
Black (+)
* applies to controllers with heating only
For connection of foot controller and warn-
ing lights, see electrical diagram in Section
6.2.4.
Summary of Contents for Z 1500
Page 2: ......