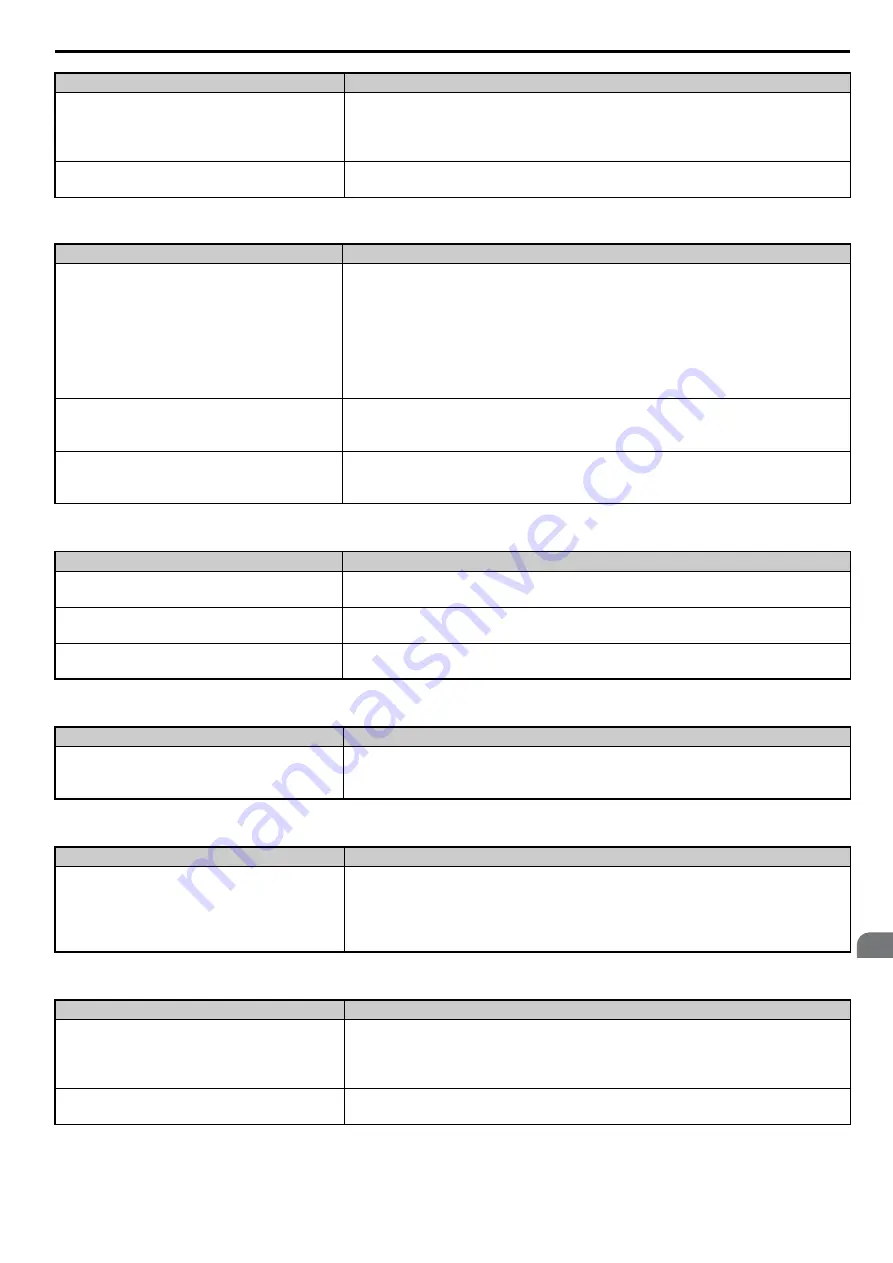
6.9 Troubleshooting without Fault Display
YASKAWA ELECTRIC
SIEP C710606 44B YASKAWA AC Drive T1000V Technical Manual
277
Tr
ouble
sho
ot
in
g
6
■
PID output fault
■
Insufficient Motor Torque
■
Motor Rotates After the Drive Output is Shut Off
■
ov or Speed Loss Occurs When Starting into a Rotating Load
■
Output Frequency is not as High as Frequency Reference
The frequency reference is assigned to an external
source and the signal is noisy.
• Ensure that noise is not affecting the signal lines.
• Separate main circuit wiring and control circuit wiring.
• Use twisted-pair cables or shielded wiring for the control circuit.
• Increase the analog input time filter constant (H3-13).
The cable between the drive and motor is too long.
• Perform Auto-Tuning.
• Reduce the length of the cable.
Cause
Possible Solutions
No PID feedback input.
• Check the multi-function analog input terminal settings.
• Set multi-function analog input terminal A1 or A2 for PID feedback (H3-02 or H3-10 =
“B”).
• A signal input to the terminal selection for PID feedback is necessary.
• Check the connection of the feedback signal.
• Check the various PID-related parameter settings.
• No PID feedback input to the terminal causes the value detected to be 0, causing a PID fault
and the drive to operate at max frequency.
The level of detection and the target value do not
correspond with each other.
• PID control keeps the difference between target and detection values at 0. Set the input
level for the values relative to one another.
• Use analog input gains H3-03 or H3-11 to adjust PID target and feedback signal scaling.
Reverse drive output frequency and speed
detection. When output frequency rises, the sensor
detects a speed decrease.
Set PID output for reverse characteristics (b5-09 = “1”).
Cause
Possible Solutions
Auto-Tuning has not yet been performed (required
for OLV Control).
Perform Auto-Tuning.
The control mode was changed after performing
Auto-Tuning.
Perform Auto-Tuning again.
Only Line-to-Line Resistance Auto-Tuning was
performed.
Perform Rotational Auto-Tuning.
Cause
Possible Solutions
Low DC Injection Braking and the drive cannot
decelerate properly.
• Adjust the DC Injection braking settings.
• Increase the value of b2-02 (DC Injection Braking Current).
• Increase the b2-04 (DC Injection Braking Time at Stop).
Cause
Possible Solutions
The load is already rotating when the drive is trying
to start it.
• Stop the motor using DC Injection braking. Restart the motor.
• Increase the value of b2-03 (DC Injection Braking Time at start).
• Enable Speed Search at start (b3-01 = “1”).
• Set a multi-function input terminal for external Speed Search command (H1-
=“61” or
“62” during restart).
Cause
Possible Solutions
Upper limit for the frequency reference has been
exceeded.
• Set the maximum output frequency and the upper limit for the frequency reference to more
appropriate values (E1-04 and d2-01).
• The following calculation yields the upper value for the output frequency = E1-04 x d2-01
/ 100
Large load triggered Stall Prevention function
during acceleration.
• Reduce the load.
• Adjust the Stall Prevention level during acceleration (L3-02).
Cause
Possible Solutions