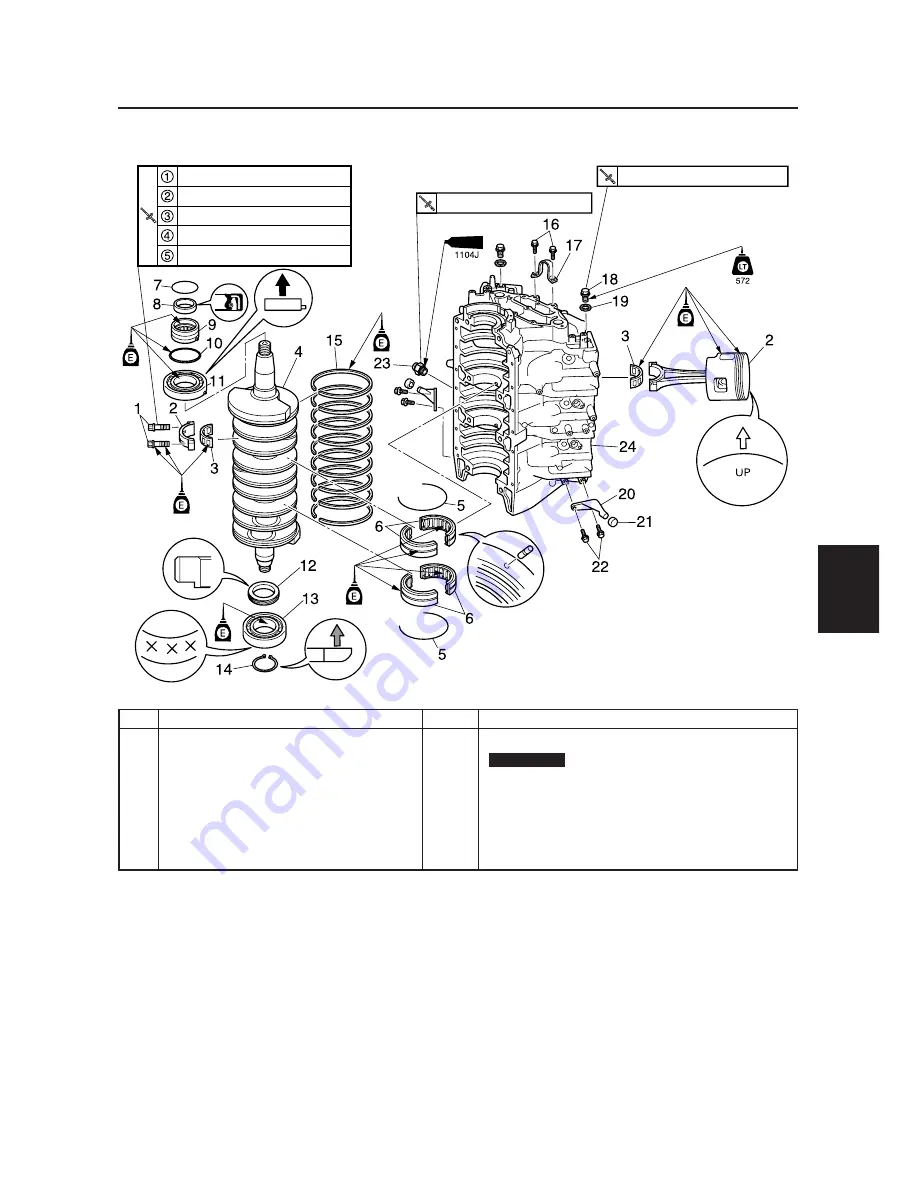
6S35H11
5-26
9
8
7
6
5
4
3
2
1
Crankcase
19 N·m (1.9 kgf·m, 14.0 ft·lb)
36 N·m (3.6 kgf·m, 26.6 ft·lb)
*
19 N·m (1.9 kgf·m, 14.0 ft·lb)
36 N·m (3.6 kgf·m, 26.6 ft·lb)
23 N·m (2.3 kgf·m, 17.0 ft·lb)
8 N·m (0.8 kgf·m, 5.9 ft·lb)
6S35110E
No.
Part name
Q’ty
Remarks
18
Plug
2
19
Gasket
2
20
Stopper
2
21
Cap
2
22
Bolt
4
M6
×
20 mm
23
Joint
1
24
Cylinder block
1
Not reusable
*: Loosen completely
6S35H11_05 9/2/05 10:35 AM Page 29
Summary of Contents for 250GETO
Page 1: ...L250G SERVICE MANUAL 6S3 28197 5H 116 250G 250G L250G ...
Page 4: ......
Page 135: ... MEMO 9 8 7 6 5 4 3 2 1 6S35H11 5 48 ...
Page 201: ...6S35H11 6 64 9 8 7 6 5 4 3 2 1 MEMO ...
Page 291: ......
Page 292: ...YAMAHA MOTOR CO LTD Printed in Japan Aug 2005 1 4 1 E_2 Printed on recycled paper 250G L250G ...